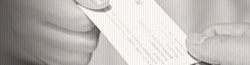
上海申弘阀门有限公司
联系人:李贤
手机:15901754341
传真:86-021-31662735
邮箱:494522509@qq.com
地址:上海市青浦区金泽工业园区
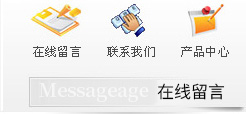
煤化工常用阀门 |
||||||||||||||||
|
||||||||||||||||
详细介绍 | ||||||||||||||||
煤化工常用阀门 上海申弘阀门有限公司 1、煤化工常用阀门引言 直接液化与间接液化的异同点。通过对现代煤化工中的煤液化工艺的分析,提出了在该类装置上使用的阀门的选择要求,还从材料、工艺、抗腐蚀、结构及耐磨特性等方面进行了分析,以期能够为煤化工企业及阀门制造企业提供参考。煤炭、煤化工行业阀门国产化 作为一个现代化的大国和消费大国,我国阀门行业的国产化如在其系列成套方面、特殊工况配套方面与发达国家都存在一定差距。国家许多重点工程用的阀门,如高参数、环保、节能阀门还多依赖于进口。依赖进口总是容易被别人卡脖子的。要实现技术装备水平的持续提升,单靠引进 国外新的技术装备是不够的,必须加速国产先进技术装备的研究与开发,改变这种依赖的状况。中国的阀门企业,要想从根本上改变依赖的状况,必须了解国家其重点行业、工程的阀门国产化情况。从而,努力实现中国阀门的全部国产化。 管道输煤在德国和美国已经不是新闻,而在中国,已经论证了十几年、早已名声在外的输煤管道,依然面临着出生证悬疑。这意味着中国还没有一条管道输煤投入建设。那么,应用于输煤管道上的阀门国产化也无从谈起。
2.煤化工 为了满足我国能源结构调整的需要,研制开发大型煤化工成套设备被列入国家大力发展的16项重大技术装备任务之一,大型煤化工成套设备的国产化也是今后工作的重点内容。 大型煤化工产业的快速发展需要相应的技术装备支持,特别是煤制油、甲醇、合成氨,以及煤制烯烃等煤化工产业需要大量的大型煤化工成套设备。相关技术装备的国产化是降低工程投资、节约外汇、提高产业竞争能力的重要措施。大型煤化工成套设备研制开发的主要攻关项目包括:特大型加氢反应器、煤液化用离心泵和容积泵、煤液化用特种阀门、油煤浆加热炉、大型煤浆均化搅拌器、大推力往复压缩机和大型离心式压缩机、特种废热锅炉、大型备煤设备、油渣气化核心设备、大型天然气制氢核心设备等。 2、现代煤化工工艺 煤制油化工工艺简图 图1 煤制油化工工艺简图 采用直接液化工艺液化油收率高;煤消耗量小;产品馏份油以汽、柴油为主;油煤浆进料,设备体积小,投资低,运行费用低。但是反应条件相对较苛刻,如德国老工艺液化压力甚至高达70mpa,现代工艺如igor、hti、nedol 等液化压力也达到17 ~ 30mpa,液化温度430 ~ 470℃。同时,除液化反应器的产物组成较复杂,液、固两相混合物由于粘度较高,分离相对困难。氢耗量较大。煤的间接液化技术是先将煤全部气化成合成气,然后以煤基合成气( 一氧化碳和氢气) 为原料,在一定温度和压力下,将其催化合成为烃类燃料油、化工原料和产品的工艺,包括煤炭气化制取合成气、气体净化与交换、催化合成烃类产品以及产品分离和改质加工等过程。 采用煤间接液化工艺合成条件较温和,无论是固定床、流化床还是浆态床,反应温度均低于350℃,反应压力2.0~3.0mpa;转化率高,如sasol 公司sas 工艺采用熔铁催化剂,合成气的一次通过转化率达到60% 以上,循环比为2.0时,总转化率即达90% 左右;但是受合成过程链增长转化机理的限制,目标产品的选择性相对较低,合成副产物较多;有效产物-ch2-的理论收率低,工艺废水的理论产量比较高。煤消耗量比直接液化要大。同时反应物均为气相,设备体积庞大,投资高,运行费用高。煤基间接液化全部依赖于煤的气化,没有大规模气化便没有煤基间接液化。 无论是直接液化还是间接液化,工艺介质中不仅有煤粉,而且,还含有h2、o2、h2s、co、nh3、co2、cl -、hn - 等易燃易爆及腐蚀性介质。而直接液化的温度在400℃以上、压力在10mpa 以上;间接液化的温度低于350℃,反应压力2.0 ~3.0mpa;这么多复杂的成分与工况要求,对其装置中使用的阀门从材料到制造加工都会提出一些特殊要求。 3、现代煤化工对阀门产品的技术要求 直接液化也叫加氢液化。在加氢过程中,其阀门、管道及相关设备处于高温高压氢气中,氢损伤就是一个很大的问题。高温高压硫化氢与氢共存时的腐蚀也很严重。正因为如此,为抗高温硫化氢的腐蚀通常阀门材料会选用奥氏体不锈钢。这样又有可能出现不锈钢的氢脆、奥氏体不锈钢的硫化物应力腐蚀开裂及堆焊层氢致剥离现象等损伤。另外还有cr-mo 钢的回火脆性破坏的问题。而且,物流中存在的氨和硫化氢等腐蚀介质可能引起的损伤等也是必须加以慎重考虑的。由于煤直接液化反应中有油煤浆的存在,煤浆对阀门、管道等设备材料的磨损问题必须要进行考虑。因此要求用于制造阀门的材料要具有符合使用要求的综合性能。具体来说,应该具有: ( 1) 作为描述材料内质特性的致密性、纯洁性和均质性性能要优越,这对于厚( 或大断面) 钢材尤为重要。 ( 2) 要具备满足设计规范要求的化学成分、室温和高温力学性能的要求。 ( 3) 要具有能够在苛刻环境下长期使用的抗环境脆化性能。 在阀门招标文件中对于阀门的致密度有明确的要求,对于锻造阀门,一般会通过对锻件的锻造比、晶粒度等要求,来实现控制致密度的要求。但是,对于铸造阀门,只是在相关的技术文件中,提到应使铸件体致密度均匀,消除铸件的缩孔与缩松,少有见到量化指标。其实恰恰是铸造阀门,往往因为对铸造工艺的质量控制不同,造成阀门铸件的质量差别很大,主要影响因素有: 成型材料的选择不同,浇冒口的设置不同,冷铁位置与数量的选择不同,凝固顺序的差异,以及冷却时间的不同等,都会导致其致密度、均质性性能差别很大。后续的热处理工艺也是阀门质量保证的非常关键的步骤之一,热处理炉的温控、铸件在热处理炉中的码放、保温时间及冷却方式与速度等因素都会影响zui终阀门铸件的机械性能。 3.2、工艺要求 煤直接液化既有加氢装置高温、高压、临氢的特性,又有煤化工腐蚀磨损工况并存的特点,因此,原材料的来源非常关键,目前,还没有找到一个行之有效的方法来控制原材料的选用,一般来讲,对阀门材质的成分尤其是有害元素含量,如s、p、o、n 及总碳当量等,提出相应的明确的指标要求,虽然这种要求往往高于材料的基本普通要求,但是,对于zui终产品质量,仅靠这些成分指标还是不够的,因为影响原材料机械性能的微量元素远不止这些。严格的讲,我们的要求仅是对常见的危害材料机械性能的微量元素予以控制,并没有也不可能完全将所有可能出现的对金属材料机械性能有害元素成分全部罗列出来。因此,铸造厂应该严格控制原料来源,对于所加工的原料不仅应该进行熔炼,还应该进一步进行精炼,特别是加强炉前控制,只有这样才有可能保证铸件质量。 在保证原材料质量的前提下,针对该类装置还有一些特殊的要求: (1) 对于现代煤化工装置的铸造阀门不能采用精密铸造工艺。因为煤液化即是加氢裂化工艺,由于氢分子对金属材料特殊的穿透性,而精密铸造出来的铸件比较疏松,均匀性也较差,因此,对于临氢工况和高温高压工况都不适宜采用精密铸造工艺取得阀门铸件; (2) 奥氏体不锈钢要进行固溶化热处理( 固溶化热处理温度为1050 ± 10℃) ,对于321 和347材料,还应进行稳定化热处理( 稳定化温度为900± 10℃); (3) 热处理炉不应采用燃煤加热炉,应采用电加热炉或者是天然气加热炉,铸件在加热炉内码放应利于炉内气流循环。由于煤加热炉会加大炉体各部位的温差,因此,不能采用燃煤加热炉; (4) 铸件试棒的选取应为联体试件。“分体”试棒无论是浇铸过程还是热处理过程都无法真正代表铸件本身的特性,与铸件本身实际的机械性能存在较大的误差,因此,不能采用“分体”试棒检验; (5) 所有阀门必须对铸件进行射线检查,检查的范围包括阀体、密封元件、阀盖,铸钢件在凝固过程中易产生缺陷,尤其对于铸钢件的关键部位、应力集中区域、承压能力薄弱的部位等,应特别加以关注。对于碳钢、合金钢铸造阀门,应逐件进行磁粉或液体渗透检查。检查范围: 阀体、阀盖和密封元件的外表面及可触及的内表面和阀杆。对于不锈钢铸造阀门,应逐件进行液体渗透检查。检查范围: 阀体、阀盖和密封件的外表面及可触及的内表面和阀杆; (6) 每个承压铸件的所有补焊面积总和应不超过铸件的表面积的10%;每个承压铸件的重大补焊数量,dn50~dn100 不超过1个;dn150 ~dn250 不超过2 个;dn300 ~dn350 不超过3 个。 上述铸造缺陷的补焊应在zui终热处理之前进行;当在射线探伤时发现有缺陷,且属于可补焊修复的,允许进行1 次补焊。补焊后应重新拍片检验,检验合格后该铸件必须重新进行热处理。补焊应具备焊接规程及工艺鉴定证书,填充金属的物理、化学性能及耐腐蚀性均应与母体金属接近。所有受压组件的缺陷zui终热处理之后,均不允许通过焊补进行修理。 3.3、要具有能够在苛刻环境下长期使用的抗环境脆化性能 对于操作在高温高压氢环境下的阀门,在操作状态下,阀门内壁中会吸收一定量的氢。在停工的过程中,若冷却速度太快,使吸附的氢来不及扩散出来,造成过饱和氢残留在器壁内,就可能在温度低于150℃时引起亚临界裂纹扩展,给阀门的安全使用带来威胁。阀门制造厂在阀门焊接时需要注意控制tp347 中δ 铁素体含量,焊态时zui大值以10%为宜( 为防止焊接中产生热裂纹,下限可控制不低于3% ) ,以避免含量过多时在焊后zui终热处理过程发生较多的相变,而产生脆性。 3.4、阀门结构要求 上海申弘阀门有限公司主营阀门有:亚博安卓-亚博竞彩网站,电动截止阀阀门结构的设计应避免煤浆结焦使阀门失效并方便清洗。油煤浆有一个特点: 如果流通不畅或者静止不动,也就是介质的流况不好,将会沉积并有可能发生聚合反应,从而出现结焦并使阀门抱死。目前在直接液化煤浆管道上使用的切断阀门全部是球阀,当操作需要切断管道将球阀关闭时,阀球内部的油煤浆因为无法排出,沉积在球腔内,就有可能结焦抱死。当球阀关闭后,煤浆因为沉积结焦而致阀球无法再次打并将球阀的耐磨层毁损剥落。所以,其实在此工况下选用球阀并不是zui合适的选择。 3.5、阀门耐磨要求 浆料工况下使用的球阀应采用金属硬密封形式,且阀座与球的材质相同,确保两者有相同的膨胀系数,在高温的条件下不会出现球体‘卡死’的现象。由于阀门的很多使用工况是在高温高压下的,根据使用经验,有些阀门在常温下测试没有问题,但是在高温工况下发生启闭操作困难,究其原因是阀芯与阀体之间产生不同步热胀造成的。所以,生产厂在出厂前应做高温启闭试验。但高温启闭试验绝不是将整个阀门投入热源中,使阀门整个温度升高,这样所得到的测试结果与实际情况是不符合的。因为,在真正使用过程中,阀门是因介质温度高而升温的,此时是阀芯先热而阀体外表面随后慢热起来,如果将整个阀门投入热源中,则阀体先热而阀芯后热,与实际工况正好相反,起不到测试的目的。高温启闭试验应建立与实践工况相一致的温度梯度。 涂层与基本材质的膨胀率应相近。否则,在高温和常温交变过程或者高温下,易产生龟裂,从而更易使涂层剥落。对超音速喷涂(hvof) 或类似的方法,涂层表面硬度为64~68hrc,结合强度不小于10mpa;对冶金熔合或类似的方法,涂层表面硬度为62 ~68hrc,结合强度不小于70 mpa。涂层的有效厚度(不包括过渡层) 为0.2 ~0.5mm。阀座应采用刮刀式设计。在球体转动时可提供一个挂刷的动作,防止阀球与阀座间的颗粒沉积。在设计时,应该注意,利用刮刀可以将球体与阀座间的颗粒挂刷掉,但是,这种刮刀设计在有的工况下会带来另一个问题: 因为附带了刮刀设计,在刮刀处形成了一个锐角,而这种锐角势必产生应力集中现象,更加不利于涂层与基材之间的结合,在磨蚀工况下,更易导致涂层的剥落,致使阀座毁损。 4、结语 |