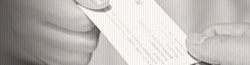
上海申弘阀门有限公司
联系人:李贤
手机:15901754341
传真:86-021-31662735
邮箱:494522509@qq.com
地址:上海市青浦区金泽工业园区
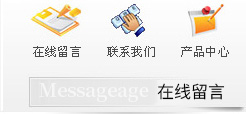
分输站撬装阀门规格书
上海申弘阀门有限公司
1分输站撬装阀门规格书概述
之前介绍自力式压力调节阀在化工行业应用,现在介绍本技术规格书为玉门绿欣农业科技开发有限责任公司西气东输一线玉门市供气工程玉门分输站撬装设备技术规格书。本技术规格书包括玉门分输站撬装设备在设计、制造、检验、运输和验收等方面的zui低要求。撬中单体设备除满足本技术规格书的要求外,还应符合相应标准和技术文件的要求。
承担此项目的供货商应根据本技术规格书和当今*水平,完成一个安全可靠、技术先进、性能稳定、功能强、操作方便、易于扩展及开发、经济合理、性能价格比高的适用于本工程的撬装设备。
供货范围包括(不限于此)设计、供应、制造、工厂测试及系统检定、包装、运输、现场测试、检定、试运行、启动、培训和提供的所有文件,包括操作和维护手册。设备中调压计量系统所采用的仪表、设备必须满足其技术规格书和数据单的要求,除非供货商在投标文件中能充分的说明所推荐产品性能优于其技术规格书的规定。供货商应在投标技术文件中对本技术规格书逐条按顺序响应,并明确说明投标货物的相关技术参数。供货商应在投标技术文件中逐条解释投标货物为满足技术规格书和数据单的技术要求所采取的措施。
2分输站撬装阀门规格书名词定义
本技术规格书用到的名词定义如下:
—业主:项目投资人或其委托的管理方。
—设计方:承担工程项目设计任务的设计公司或组织。
—供货商:为业主设计、制造、提供撬装设备的公司或厂家。
—分包商:设计和制造分包合同所规定的撬装设备的公司或厂家。
—技术规格书:说明向业主提供的撬装设备必须满足的要求,以及验证这些要求所需的程序的书面规定。本技术规格书由技术条件、数据单及附图三个部分组成。
—技术条件:用于规定撬装设备达到的各项性能指标和质量要求的文件。
—数据单:根据各工程项目实际情况,用于描述撬装设备的订货参数的文件及表格;应按照建设项目管理程序,经审批后用于订货。
—技术要求:指项目对撬装设备的特殊要求、业主的专门要求、以及需对“技术条件”规定进行修改或调整的内容。
—质保期:供货商承诺的对所供撬装设备因质量问题而出现故障时提供免费维修及保养的时间段。
3项目要求
3.1总体要求
气动截止阀,电动蝶阀,气动蝶阀本技术规格书对玉门分输站撬装设备及其相关部分的设计、制造、组成、包装、运输、安装、投运、培训、亚博竞彩网站的售后服务等提出的zui低技术要求。承担此项目的供货商应根据本技术规格书和其它相关的设计文件及标准规范,负责从设备设计、系统集成、检定控制系统编程组态、系统测试、包装运输、现场安装到投运、亚博竞彩网站的售后服务及培训的全过程工作,并对所提供的撬装设备的功能、技术、质量、进度、服务负全部责任。
本技术规格书将随着工作的进展进行修订,zui终成为供货合同的一个组成部分。
3.2 供货商要求
承担此项目的供货商应根据本技术规格书和当今*水平,完成一个安全可靠、测量准确度高、技术先进、性能稳定、功能强、操作方便、易于扩展及开发、经济合理、性能价格比高的适用于本工程的撬装设备。
该撬装设备能完全满足设计要求的全部功能、以及本技术规格书的要求和在本技术规格书中未提及的而又是一个完整的分输站撬装设备所*的内容。
供货商是否具有iso09001质量管理体系认证证书和国家质检总局所颁发的《压力管道元件组合装置生产许可证》或部门颁发的同等资质的橇装设备生产许可证书。具有类似于本项目丰富的天然气管道工艺和调压计量系统及其相关自动控制系统方面的经验和业绩,并具有为本项目提供所需的产品以及系统集成和的能力。能根据所提供的资料独立的配置、完成整个系统并使其完全满足本工程的需要。供货商必须具备良好的信誉和亚博竞彩网站的售后服务能力,具有强大的技术实力、系统集成能力、完成本工程的技术能力、充足的人力资源。供货商须提供在近五年来国内高压(≥10.0mpa)天然气管道项目中有总数在5套以上的成功使用业绩,并提供可核实的业绩证明。供货商为本项目委派的项目和主要的技术人员应是在天然气管道调压计量系统方面的专家,他们在zui近5年内有多项与本项目类似的工作业绩,主要技术成员资历证书应交业主审批,作为本项目能力的考评指标。供货商的项目组的主要管理和技术人员,在本项目完工之前不应被随意更换。
成撬设备中中的换热器、气体流量计、流量计算机、安全切断阀、自力式调压阀、电/气动执行机构、温度变送器、压力/差压变送器及阀门(含球阀、放空阀、排污阀及仪表阀门)等核心部件应优先选用在国内重大管道类似项目中具有成功供货业绩的成熟产品,并提供业绩清单及项目信息,并且应得到业主的批准。供货商所提供的所有的软件、硬件和其它辅助设备,在中国境内应有强大的亚博竞彩网站的售后服务能力,并提供保证函件,以方便业主对亚博竞彩网站的售后服务的需求。
在业主认为需要时,将派遣有关专业的专家与供货商一起工作,并监督项目执行的全过程。业主保留对系统设计、选用的设备、材料和选用的软件等提出修改及决定性的意见的权力。业主保留对供货商的系统设计提出修改变更的权力。
在项目实施过程中,某些技术参数和条件的变化是不可避免的,供货商在项目实施过程中应充分考虑到这些因素。业主保留对所提交的技术及其它的资料变更的权力。
4 遵循的标准、规范
本技术规格书产品应遵循的规范、标准法规主要包括但不于以下所列范围:
gb 150 压力容器
gb/t 9115 钢制管法兰
gb/t 9711 石油天然气工业管线输送系统用钢管
gb/t 11062 天然气发热量、密度、相对密度和沃泊指数的计算方法
gb/t 13927 通用阀门压力试验
gb/t 15464 仪器仪表包装通用技术条件
gb/t 17747 天然气压缩因子的计算
gb/t 18603 天然气计量系统技术要求
gb/t 18604 用气体超声流量计测量天然气流量
gb/t 18940 封闭管道中气体流量的测量——涡轮流量计
gb/t 21391 用气体涡轮流量计测量天然气流量
jjg882 压力变送器
jjg829 电动温度变送器
jjg1030 超声流量计
jjg1037 涡轮流量计
gb3836 爆炸性气体环境用电气设备
gb4028 外壳防护等级的分类
gb12237 通用阀门法兰和对焊连接钢制球阀
gb12224 钢制阀门一般要求
gb50251 输气管道工程设计规范
gb/t 13927 通用阀门压力试验
gb12221 法兰连接阀门结构长度
gb/t13927 通用阀门压力试验
jb/t 9092 阀门的检验与试验
jb/t7927 阀门铸钢件外观质量要求
sy/t 0599 天然气地面设施抗硫化物应力开裂金属材料要求
sy/t10043 泄压和减压系统指南
asme b31.8 输气及配气管线系统
api 6d 管线阀门
api 607 软密封和90°转向阀门的耐火试验
api 6fa 阀门耐火测试
api 598 阀门的检测和试验
asme 锅炉和压力容器规范第v、viii、ix部分
asme b16.5 管线法兰和法兰管件
asme b16.20 钢管阀兰的环形垫圈和环形槽
asme b1.20.1 管螺纹
asme b16.25 对焊接头
asme b16.34 法兰、螺纹和焊接端阀门
sspc sp10 金属表面处理
其它未列出的与本产品有关的规范和标准,供货商有义务主动向业主和设计提供。所有规范和标准均应为项目采购期时的有效版本。
5 供货范围及界面
供货商的供货范围包括:与本工程撬装设备有关的全部设备和计量检定软件、 系统设计、培训、系统集成及制造、编程组态、fat、装箱发运、现场安装及通电试验、现场调试、sat、投产、项目管理、亚博竞彩网站的售后服务等。在本技术规格书中未提及但完成本项目所需的内容和工作也在供货商供货范围之内。
供货商的工作范围应包括以下内容,但不局限于此:
1)根据本技术规格书及其它的相关文件进行撬装设备设计,并提供详细的设计文件(设计文件需经业主和设计批准后方可实施);
2)系统集成;
3)为业主和设计提供软件、硬件培训;
4)现场操作员培训;
5)所有应用软件编程组态及调试;为了能够使业主和设计的有关技术人员全面地、深入地掌握该软件,在实际的运行中能够根据需要进一步地开发它, 应用软件的编制和组态采用由供货商、业主、设计三方合作的方式来完成。 应用软件的编制工作在供货商的工厂完成。供货商应对应用软件的结果负责。
6)人—机界面(hmi——human/machine interface)的动态画面设计及制作;
7)与第三方软件或智能设备之间的衔接和测试;
8)工厂验收试验(fat——factory acceptance test);
9)装箱发运;
10)现场安装和试验;
11)现场监督指导与站控系统相关联仪表、设备的接线;
12)现场调试;
13)预投产;
14)现场验收试验(sat——site acceptance test);
15)投产;
16)72 小时的运行监护;
17)提供竣工资料;
18)提供备品备件;
19)亚博竞彩网站的售后服务;
20)项目管理。
—所需全套紧固件 30%裕量,且每种规格不少于10个。
—所需各种规格垫片 200%裕量。
供货商应对所提供产品的完整性负责。
5.1 分输站撬装设备
玉门分输站撬装设备分为进站阀组区、工艺装置区、出站阀组区三部分。进、出站阀组区主要由进、出站紧急切断阀、放空系统、温度变送器、压力(差压)变送器组成;工艺装置区由贸易计量、过滤、分输计量、换热、调压、加臭等组成。撬装设备应具有防爆要求高、调压级数多、用气压力调节范围大、安全性能好、间歇供气、计量要求较高等特点。
撬装设备为露天、水平安装,流量计算机等盘装仪表在站控室内安装。贸易交接流量计用气总量通过站控系统上传至北京油气调控中心和廊坊调控中心。
5.1.1 贸易计量
贸易计量主要由流量计、温度变送器、压力(差压)变送器、流量计上下游截断阀等组成。贸易计量流量计近期选择涡轮流量计,远期选择超声波流量计,在工艺配管时需考虑到远期超声波流量计直管段需求。
5.1.2 过滤
过滤主要由过滤分离器及其配套的放空、排污、上下游截断阀组成。
5.1.3 分输计量
分输计量主要由流量计、温度变送器、压力(差压)变送器、流量计上下游截断阀等组成,分输计量流量计选择涡轮流量计。
5.1.4 换热
换热由水浴式换热器、温度变送器、上下游截断阀组成。
5.1.5 调压系统
调压系统主要由调压器、超压切断阀、压力表、阀位指示与报警、调压器上游截断阀等组成。调压器上游应设置超压切断阀。
5.1.6 加臭系统
加臭系统包括现场设备和控制系统两部分。现场设备应主要包括上料装置、加臭剂储罐(带液位计) 、隔膜式计量泵、流量监视仪、过滤器、配电箱和加臭剂注入喷嘴等,此外至少应包括系统正常工作所需的电气、仪表元件等。控制系统应采用工控机或plc(配文本显示器)或单板机等控制器组成控制系统。
5.1.7 工艺系统
工艺系统主要是由计量、过滤、换热、调压管路组成;每条管路上是由上下游截断阀、直管段等组成。还包括安全阀、节流截止放空阀、压力表等。
各手动放散、安全放散管路汇总至橇外集中排放,橇内外放散管连接采取法兰连接方式。
供货商应提供过滤器、流量计、调压器、截断阀、直管段等与管道连接的所有法兰,以及调压计量橇工艺主管路、集中放散与橇外管道连接的法兰(包括配对法兰及螺栓、螺母、垫片等)。
5.2 供货范围
供货商应为本工程提供一套适应工程需要、性能可靠、稳定、性能价格比高的撬装设备。该设备应能完全满足设计要求的全部功能和设计中遗漏但在实际应用中需要的功能。
1)计量仪表盘用于流量计算机的安装,该仪表盘的设计、制造、接线以及与上位控制系统通信等由供货商完成。
2)现场橇装设备的接线箱到站控室计量仪表盘之间的电缆由第三方提供。供货商应提供传输信号所需电缆的技术要求,并负责指导现场接线箱的电缆接线。
3)通常业主将提供220vac±10%,50hz±5%或380vac±10%, 50hz±5%的电源。撬装设备的配电由供货商负责。
4)在控制室内安装的计量仪表盘,由供货商提供安装要求和尺寸、重量等参数,经业主统一布置后由供货商负责安装。
5)供货商应协助站控系统供货商完成流量计算机与站控系统的数据交换。供货商应提供数据接口类型、信号类型、通信协议等技术数据。
7)供货商应提供调压计量加臭橇的接地要求及接地母线,由第三方完成调压计量加臭橇的接地母线与站场接地系统之间的连接。通常站场接地系统将采用tn-s系统。
6 技术要求
6.1 总则
根据本技术规格书后所提供的分输站带控制点的工艺流程图和撬中各设备详细技术参数,选择合适的系统设备,以满足各站场对本系统的使用要求。
1)保证所提供的撬装设备为全天候连续运行方式,每年运行不少于360 天,在现场条件下服务寿命zui低应保证30年。
2)保证撬装设备的正常工作,保证设备不受装配、运输、安装、调试等外来因素的影响,供货商提供的所有设备应是在工厂组装在一起的成橇装置,并且在工厂已进行过单项设备和橇装整体试压以及整体功能调试。
3)设备调压阀上、下游的差压比较大,为保证安全,供货商可根据计算设置安全阀,安全阀的反应速度及泄放能力应能满足事故时的放空要求,并应符合有关标准及规范的要求。对安全阀的技术要求应参照其技术规格书中的有关技术要求执行。
4)对于所有设备的材质,应选用适合环境温度及工艺条件的材料,不能使用铸铁、半钢或球墨铸铁的材质。在环境温度低于-19℃时,仪表或设备承压部分采用的材料应特别引起注意。
5)橇装设备应固定在钢制结构的底座和支架上,该底座与支架应采用型钢制作。整套橇装系统应有用于吊装用的吊环,底座上应预留用于现场安装的螺栓孔,橇装系统的管道高度应根据现场工艺管线的高度确定。
6)撬装设备为露天、水平安装。供方可根据其中单项设备的具体要求,选择保温或防护箱等对其进行保护。
7)除进、出站阀组区阀门有焊接连接外,各设备之间以及与工艺管道之间,均采用法兰连接。撬装设备与撬外工艺管道采用焊接或法兰连接,若采用法兰连接,供方应提供与现场工艺管道连接用的配对法兰、密封垫、紧固件等。
8)所有电气部分应符合现场防爆及防护等级的要求,防爆等级不应低于exdⅱbt4,防护等级不应低于ip65。如果系统中有本安设备,所需要的安全栅应由供方提供。
9)撬装系统及仪表检测等所有电气部分的控制电缆、电源电缆,都应通过防爆接线箱引入或引出,防爆接线箱应安装在合适的位置,以便于现场接线。信号与电源接线箱应分别设置,接线箱内部的接线端子应留有15%的余量。接线端子应具有防雷、防浪涌保护功能。接线箱应由供货商负责提供,并负责从橇装的每个电气设备到接线箱的接线,连接电缆和接线方式应符合有关的防爆标准的规定。所有电缆均应穿保护管敷设,电源电缆与信号电缆不应共用一根电缆保护管。电缆保护管应采用dn20、dn25 的钢管。电缆保护管与仪表、设备等的连接处应采用防爆挠性连接管,并设电缆夹紧装置以防电缆脱落或扭转。电缆保护管与接线箱连接,在它们之间450mm 以内应设隔离密封接头。电缆保护管上应设排除冷凝水的密封接头。
10)所有信号、电源电缆应采用铜芯多股绞合软导体,它们的绝缘耐压等级应为额定电压的2 倍且不小于500v。它们应为阻燃型。信号电缆的线芯截面积不应小于1.5 mm2,电源电缆的线芯截面积不应小于2.5mm2。
11)保证设备安全和系统的可靠,在有可能将雷电感应所引起的过电流与过电压引入系统的部位(仪表信号传输接口、执行机构信号接口、数据通信接口、供电接口等),应安装浪涌保护器。所选用的浪涌保护器必须能承受预期通过的雷电流,并有能力熄灭在雷电流通过后产生的工频续流。对于电源接口要求抗电涌的主要技术指标:标称放电电流≥60ka(8/20μs),测试电流10ka。数据通信接口和其它的i/o点抗电涌的主要技术指标:标称放电电流≥10ka(8/20μs),测试电流3ka。橇上电气设备的浪涌保护器通常安装在防爆接线箱中。
12)橇中的工艺管路法兰应跨接,确保电气导通,所有电气设备均应有可靠的接地,并统一汇接于一处,系统的橇体应设有防静电接地点。
13)设备检修或事故时,系统中若有放空需要,其所有的放空管线应汇成一根放空管,终端连接法兰,供货商应提供配对法兰及紧固件,以便与现场工艺放空管线连接。
14)撬中应有相应的排污措施,所有排污管线应汇接在一起,终端连接法兰,供货商应提供配对法兰及紧固件,以便与现场工艺排污管线连接。
15)正常工作时,撬中不得有气体泄漏。
16)撬中所有管道、设备及橇体外表,均要涂上耐腐蚀性好的涂料,至少应保证使用年限为5年。
17)撬中所有管道、设备及橇体的喷漆,应符合厂家的标准,并应事先得到买方的批准。通常,天然气管道为黄色,放空管线为红色,排污管线为黑色,支架为灰色。
18)撬中所有设备、管路均应布置合理,其整体外形尺寸应便于现场安装,并应满足运输的要求。若一个橇体无法满足运输要求时,可将整个系统分为多个橇,其整体组装由施工单位现场完成,由供货商派人指导安装。
19)站撬中的每项设备都至少应遵从本技术规格书及相关设备的技术规格书中对相应设备的技术要求。系统中的测量仪表的准确度、量程范围、输出信号、安装方式、安装位置等应满足现场的使用要求。
20)供货商应负责提供向站控系统传输的所有信号的类型和通信接口类型及数量,并负责协助站控系统集成商完成双方数据的通信交换。
6.2 流量计
本工程对外贸易计量仪表采用超声波流量计、内部计量仪表采用气体涡轮流量计,去站内自用气计量仪表采用涡街流量计。超声波流量计、气体涡轮流量计和涡街流量计及其相关的组件(温度、压力传感器及流量体积修正仪)应适合燃气流量的连续测量,适应被测燃气流量、压力、温度的变化,满足现场安装、使用环境的需求。
6.2.1、超声波流量计
1 )总则
供货商提供的由超声波流量计及其相关的附件组成的流量检测系统应适合本项目中天然气的连续测量,适应被测介质的流量、压力、温度的变化,满足现场安装、使用环境的需求。
有关管道材质、壁厚、内外防腐涂层材料和厚度等参数,将在相应的数据表中列出,供货商应根据本技术规格书和相应数据表的技术要求向用户供货。
超声波流量计和信号处理单元(流量变送器)在室外露天安装,并处于爆炸危险场所区域内,其防爆等级不应低于exdⅱct4或exiaⅱct4,防护等级不应低于ip65。
流量检测系统的设计应保证具有尽可能长的使用寿命、稳定的性能,以及尽可能高的系统计量准确度。
2)测量精度与制造要求
超声波流量计应采用双声道、时差式测量原理,测量准确度不应受输送介质的压力、温度、流量等影响。
仪表应能以分辨率1/200000检测超声波传播的速度。该仪表在流速等于或大于0.4572m/s时,测量流量的精度应达到±0.5%,在流速小于0.4572m/s时,精度应不低于±1.5%。
当qt<qi≤qmax时,超声波流量计的重复性<0.1 %,当qmin≤qi≤qt ,超声波流量计的重复性<0.3 %。
流量计系统应按zui大运行流量设计,流量计运行范围不大于流量计zui大量程的80%。
为确保流量检测系统达到*的测量准确度,供方应根据现场具体情况,推荐流量计上、下游直管段长度及对其详细的技术要求(如直管段的粗糙度、圆度、线膨胀系数等),以及温度、压力检测点的安装位置。
为提高流量测量的准确度,超声波流量计应具有动态自动调零功能,能够消除零点漂移对测量结果的影响。
供货商应提供超声波流量计的zui低安装要求,同时说明噪声及振动对超声波流量计的影响。
供货商应提供对信号传输电缆的zui低技术要求,从传感器到流量变送器的信号传输电缆由供货商提供。
流量计传感器与流量变送器的连接电缆应采用阻燃电缆,电缆护套、橡胶、塑料和其它暴露部分应能抗紫外光、火焰、油类和油脂。
在不降低流量计性能的前提下,制造商应说明为保证超声波流量计的声波在天然气中正常传播所需的zui低及zui高工作压力限制要求。
流量计供电电源要求采用24vdc。
该计量系统应能够避免在声波传播速度计算时或者在空管中恢复流量、失电以及液体中含有气泡的条件下计算流量时发生误差。而且,在发生诸如泵启动或关闭压力下降、或者其他原因引起的变化时,流量计的准确度不应超出标称准确度。
流量计系统应配备温度检测仪表,以便能根据温度和雷诺数的变化进行补偿计算,确保流量计系统输出数据的准确性。
3)传感器
超声波流量计应为宽波束或时差传感器。
流量计传感器的探头应可以通过耦合剂粘在管道上,与管道间无缝隙,并采用铰链将其固定在管道上。供货商应根据现场实际情况推荐传感器探头之间的安装间距,此间距应是可调的,并可通过传感器附带的标尺进行定位,探头定位后应能用定位销将其锁紧,不可随意移动。
在现场更换传感器探头不应导致流量计性能变化。
供货商应提供更换传感器探头的操作程序和所需进行机械、电子及其它方面调整的详细说明。
流量计的所有零部件应该用抗腐蚀材料制造或者用适合在流量计所处环境中使用的抗腐蚀涂层进行保护。
为防止流量计不受外部侵害,供货商应配套提供传感器的外防护罩,防护罩应采用不锈钢罩,并便于安装及拆卸。
供货商/制造商应提供每一对传感器的测试文件,测试文件至少应包括测试数据、测试/校验方法、性能参数等。每一对传感器应标有*性的编号和主要的技术规格(如主要的尺寸、允许的压力、温度的范围等)。
4)流量变送器(处理单元)
流量变送器应是以微处理器为核心,准确、稳定、可靠的将被测介质的流量转换为标准的高频脉冲信号、数字信号(rs-485)及模拟信号(4~20ma)的装置。
流量变送器能具备打印显示现场设置的参数和诊断的数据的功能,并能将选择的数据传送至站场控制系统。
流量变送器应采用手持式编程器或计算机,完成用来实现现场设置和根据输入密码权限来修改参数。
流量变送器应能够保存初始的设置参数并能够重新设置,修正液体的声波特性,在失电、空管和液体中含有一定数量气泡的情况下,流量计的准确度不应超出标称准确度。当气泡数量超过60%时应能报警。
流量变送器应能运行于液体中含有气泡的情况下,并能检测出含气泡的比例。
流量变送器应提供满足要求的声波和流体温度数据传送给站控制系统,能够测量流体的密度,来实现流量计算的补偿,并计算标准状态下液体的体积流量和质量流量。
流量变送器应适于在户外和爆炸危险性场所安装,其防爆、防护等级应符合现场要求。
流量变送器现场安装并应通过rs-485或rs-232c接口zui少将有关的流量、密度、介质温度、声波传播的速度、流体的流向、故障等信号传送至站控制系统。
5) 软件
供货商应提供与流量计配套的组态、测试及远程诊断软件。
配套软件要求:软件应具有良好的人机界面(mmi),可实时在线监测、检测超声波流量计的工作状态。软件至少应能显示和记录以下测量数据:管输条件下的流量、平均流速、平均声速、以及由每一个传感器接收到的超声信号的质量。在超声波流量计处于非正常工作状态时,可及时提供报警。软件的修改、参数设置和操作应设立分级保密码。
6)材料
超声波流量计传感器本身应为金属结构,在声波通道中不得有塑料材料。
7)检验和测试
(1)工厂验收试验
所有仪表在出厂前应根据有关规范进行工厂试验,以证明所提供的设备在各方面均能完全符合买方的要求。
超声波流量计应依据相应的工业标准或其它的管理规范进行测试。
供货商应向买方提供每台仪表的出厂测试报告及质量检验报告,应是具有签署和日期的正式报告。
供方必须对所供设备进行100%的试验和检验,其内容至少应包括:
①静态测试
数量检查(包括附件);
外观检验(包括漆面质量、表面光洁度等检验);
尺寸检测;
标牌标识是否完整、清晰;
防爆等级的认证证书;
紧固件等是否有松动现象;
连接件形式、尺寸是否符合标准;
是否遵从焊接规范和标准;
材质是否与供货商提供的证明相符(内部件,外壳、连接件等)。
②动态测试
准确度;
滞后性;
复现性;
绝缘性能试验;
仪表功能测试;
其它内容测试。
(2) 现场验收试验
仪表设备运抵安装现场后,由供方与买方共同开箱检查,发现问题,由供方负责解决(即使在供货商工厂已试验过且已通过出厂验收)。
在现场验收试验前两星期,供方应事先提出试验计划,并须征得业主的批准。现场试验合格后,由用户预验收。
8)供货范围及界面
供货商应提供超声波流量计及配套的附件。
9)标记与铭牌
每一个超声波流量计成品都应有指示流量方向的标记和铭牌,单位应为单位制。下列数据应在铭牌中标出:
—制造商和原产地名称
—产品名称、型号和系列号
—公称直径和zui大流速
—zui大工作压力
—出厂编码和生产标志
—制造测量仪器的许可证
—商标
6.2.2、涡轮流量计
1) 总则
为保证涡轮流量计的测量准确度和安装质量,流量计及附件采用成套整体供货方式。流量计应选择准确度高、维护量少的产品,其它配套设备应合理、可靠。供货商提供的涡轮流量计及相关的附属设备能够适合天然气流量的连续测量,适应管道内介质的组分、流量、压力、温度的变化,满足现场安装、使用环境的要求。
气体涡轮流量计应满足gb/t 21391、gb/t 18940、iso 9951和a.g.a no.7的要求,并将它们作为zui低要求。 若这三个标准之间有冲突,则应优先采用gb/t 21391。
流量计处于爆炸危险场所区域内,其防爆等级不应低于exdⅱbt 4,防护等级不应低于ip 65。
所有设备的压力等级应不低于管道的设计压力。所有设备和附件的材料选择应考虑在zui低环境温度条件下运行,还应考虑介质温度和介质组分的影响。
流量计的口径根据站场实际介质流速确定,一般不超过dn300。在zui大设计流量运行时,流量计测量管内天然气的计算流速不宜超过15 m/s。
气体涡轮流量计经过实流校准,流量测量准确度等级必须达到0.5级要求,即:
zui大允许误差: zui大允许误差≤±0.5 %, qt≤qi≤qmax;
zui大允许误差≤±1.0 %, qmin≤qi<qt;
流量测量重复性: ≤0.16 %, qt≤qi≤qmax;
≤0.33 %,qmin≤qi<qt;
其中流量计的分界流量qt应小于0.2 qmax。
供货商应提供被测天然气中各组分对流量测量的影响。
供货商应提供说明振动和脉动流对流量计流量测量准确度产生的影响,并推荐解决措施。
供货商应提供涡轮流量计的过载能力指标。
贸易计量用涡轮流量计应自带整流器的流量计,流动调整器材质应采用不锈钢。如流量计不具备自带流量计,供货商应参照设计单位所提供的流动调整器技术规书要求进行加工制造。
供货商必须负责提供向站控系统传输的所有信号类型和通信接口类型及数量,并负责协助scada系统集成商共同完成双方数据的通信交换。
2)涡轮流量计
流量计表体和其它所有部件,包括承压构件和电子元件,应当选用适合于流量计工作条件的材料进行设计和制造,确保使用寿命和持续准确度。
流量计的zui大设计工作压力应当是下列部件的zui大工作压力中的zui小者:流量计表体、法兰、转换器及其安装联接件。
流量计的表体应进行强度试验,试验介质为水,试验压力为1.5倍的公称压力,并至少保证5分钟,经检查无泄漏和损坏。
对出厂的涡轮流量计应进行气密性试验,试验介质为干空气或者氮气,试验压力为1.05倍的公称压力,并至少保证5分钟,经检查无泄漏。
流量计上游用过滤器滤掉较大杂质后,流量计不应受介质中所含固体颗粒的影响,无论在何种情况下,流量计都不应该被介质中所含杂质卡死。供货商应推荐过滤器的目数与过滤面积。
供货商应提供各个压力等级和口径下的流量计表体的标准长度。为了与已有的管路相匹配,用户可不同的长度和口径。流量计的设计结构和制造公差应满足允许相同尺寸和类型的流量计的测量部分可互换。为减少维修及维护的成本及时间,减轻操作人员的劳动强度,流量计必须易于维修,在不将流量计整体拆下线的情况下就可对其内部运动部件进行维修及维护。
流量计表体的联接法兰应当符合通用的行业标准、国家标准或标准。用户应当给制造厂提供安装现场的适用标准和其它要求。
流量计上应有至少一个用于测量静压的取压孔,用于连接压力补偿计算用压力变送器。取压孔结构、位置应符合gb/t 18940、gb/t 21391的相关规定。取压孔应带有取压截止阀。取压截止阀的材料应为不锈钢,公称直径为dn 15,连接螺纹为1/2 npt (f),压力等级应不小于流量计zui大操作压力。
流量计还应设计成在运输和安装期间容易安全搬动,并应设计有吊孔和吊索放置的空间。如流量计需要安装支架,支架由供货商提供。
所有设备和附件的材料选择应考虑在zui低环境温度条件下运行。
供货商应提供在安装、启动、维修维护和操作过程中,对流量计的降压和升压速率给予明确的说明。
如果具有可卸机芯流量计结构,应能确保更换机芯后或拆卸并重新安装同一型号机芯后,流量计性能特性不发生变化。供货商应需要提供更换机芯的操作程序和所需进行机械、电子及其它方面调整的详细说明。
供货商应提供说明涡轮流量计的叶片型式。
为使流量计运行良好,其结构应使所需的任何润滑装置密封不泄漏,推荐采用*性免维护方式。如采用外部加注泵形式,供货商应提供润滑油的类型和数量以及润滑油更换时间的详细说明。润滑系统采用防水设计。
为防止计量数据的丢失;提高计量数据的可信度;对于可能影响计量准确度的地方;都必须提供可加封印的条件。
流量计和变送器的连接电缆应采用阻燃电缆,电缆护套、橡胶、塑料和其它暴露部分应能抗紫外光、火焰、油类和油脂。
供货商应提供对信号传输电缆的zui低技术要求,并对所提的技术指标负责。
供货商应提供流量计在zui大流量下的压力损失数据。
流量计应具备同时输出至少2路以上高频探头信号功能,以满足在线实流检定的要求。
流量计应具备自诊断功能。
3) 一体化智能流量计
一体化智能流量计应具备以下功能:
——就地显示被测介质压力、温度、标况下的瞬时流量和累积流量;
——实时远传相关数据;
——数据储存功能;
——参数设置及管理权限设置。
一体化智能流量计至少能储存一年内每个月的累积流量和zui近300次的瞬时流量数据,一般包括时间、温度、压力、瞬时标准状态下的体积流量和标准状态下的累计流量。
具备远传功能应提供通信协议和接口型式。一般信号形式为模拟信号、串行数据信号、频率信号等。
电源可采用内电源供电或外电源供电,如果采用内电源供电,电池可以连续使用一年以上;外电源供电一般采用24vdc。
流量积算仪需获得oiml、ptb、nel或api贸易计量认证。
4)材料
供货商应对涡轮流量计工作在zui高设计压力条件下所采用的材料耐压等级是否能满足要求进行核算并提供充分的书面依据。如果不能满足,应提高流量计的耐压等级或采用适当的材料。
涡轮流量计与天然气接触的所有部件的材质应使用适用于天然气的材料制造,它们既不能影响天然气的性质,又不能受天然气的影响。
涡轮流量计内部的所有与天然气介质接触表面应用抗腐蚀材料制造,尤其选用能够抗硫化氢腐蚀的防腐材料。
涡轮流量计外部应选用适应环境条件的抗腐蚀涂层进行保护。
供货商应提供主要零部件材料化学成分、机械性能、无损检测报告。
6)检验和测试
(1)工厂验收试验
所有涡轮流量计及辅助设备在出厂前应根据有关规范进行工厂试验,以证明所提供的设备在各方面均能完全符合买方的要求。
涡轮流量计应依据相应的工业标准、国家计量检定规程或其它的管理规范进行测试,所依据的检定规程、标准应征得用户的同意。
供货商应向买方提供每台涡轮流量计的出厂测试报告及质量检验报告,应是具有签署和日期的正式报告。
供方必须对所供涡轮流量计进行100%的试验和检验,其内容至少应包括:
①静态测试
数量检查(包括附件);
外观检验(包括漆面质量、表面光洁度等检验);
标牌标识是否完整、清晰;
防爆等级或本质安全设备的认证证书;
紧固件、连接管路等是否有松动现象;
电源及接线是否满足要求;
连接件形式、尺寸是否符合标准;
是否遵从焊接规范和标准;
无损探伤检验及其报告;
材质是否与供货商提供的证明相符(内部件,外壳、连接件等)。
②动态测试
准确度;
重复性;
强度试验;
气密性试验;
绝缘性能试验;
压力测试(包括附件);
系统性能测试并提供检验测试报告;
仪表功能测试;
其它内容测试。
(2) 现场验收试验
涡轮流量计及辅助设备运抵安装现场后,由供方与买方共同开箱检查,发现问题,由供方负责解决(即使在供货商工厂已试验过且已通过出厂验收)。
在现场验收试验前两星期,供方应事先提出试验计划,并须征得业主的批准。现场试验合格后,由用户预验收。
(3)涡轮流量计的检定
每台流量计在安装使用前应在国内的法定计量检定部门进行实流检定(校准),不合格者由供方负全部责任。
流量计的实流检定应依据现行的国家计量检定规程,采用的介质、温度、压力、测量条件和环境条件应尽量接近现场工作条件。
检定的流量点至少包括qmin ,qt,0.25 qmax,0.40 qmax,0.70 qmax和qmax。量程比大于20:1的流量计,还应增加一检定点,其流量为0.10 qmax。
每个流量点检定次数不能低于6次。
检定后,应使用新流量计系数消除测量偏差,保证流量计计量性能。
供货商应提供法定计量检定部门出具的实流检定/校准证书,并以书面形式提供调整系数的详细说明。
7)供货范围及界面
供货商应提供涡轮流量计、信号处理单元,流量计算机、流动调整器、配对法兰、垫片、螺栓、螺母、配套监控软件等。
8)标记与铭牌
每一个涡轮流量计成品都应有指示流量方向的标记和铭牌,单位应为单位制。下列数据应在铭牌中标出:
—制造商和原产地名称
—产品名称、型号和系列号
—公称直径和zui大流速
—zui大工作压力
—出厂编码和生产标志
—制造测量仪器的许可证
—商标
6.2.3、涡街流量计
1)定义
涡街流量计:在流体中设置旋涡发生体,从旋涡发生体两侧交替地产生有规则的旋涡,这种旋涡称为卡曼涡街(karman vortex street),旋涡的频率与流体的速度成一定比例,从而计算出体积流量。
分辨率:仪表能显示的流速变化的zui小程度。
准确度:测量结果与被测量(约定)的真值之间的一致程度。
重复性:在整个刻度范围内,并在相同操作条件和相同参比流量下,对同一被测量进行连续多次测量所得结果之间的一致性。
复现性:在改变了的测量条件下,同一被测量的测量结果之间的一致性。
偏差:由被检流量计测得的实际体积流量(例如工程单位为m3/h的流量)与标准流量计测得的实际体积流量之差。
误差:测量结果减去被测量的真值。百分比误差按以下公式计算:
百分比误差=[(被测仪表读数-标准仪表读数)÷标准仪表读数]×100%
zui大误差:在规定的仪表操作范围内的允许误差极限。
q:可测得的通过涡街流量计的体积流量。
qm:可测得的通过涡街流量计的质量流量。
qvn:标准状态下(20ºc,101.325kpa)体积流量。
2)总则
(1)供货商提供的涡街流量计及其相关的附件应适合本项目中的流体流量的连续测量,适应被测流体的流量、压力、温度的变化,满足现场安装、使用环境的需求。
(2) 所有设备的压力等级应不低于管道的设计压力。所有设备和附件的材料选择应考虑在zui低环境温度条件下运行,还应考虑介质温度和介质组分的影响。
(3)涡街流量计和信号处理单元(流量变送器)在室外露天安装,并处于爆炸危险场所区域内,其防爆等级应不低于exdⅱbt4,防护等级不低于ip65。
(4 ) 为确保计量达到*的测量准确度,供方应根据现场具体情况,推荐流量计上、下游直管段长度及对其详细的技术要求(如直管段内径与流量计内径之间zui大允许偏差、直管段的粗糙度、圆度、线膨胀系数等),以及温度、压力检测点的位置,同时,应提出对整流器的安装要求。
(5)供货商应提供对涡街流量计zui低安装要求,说明噪声及振动对涡街流量计的影响因素。
(6)涡街流量计的口径应根据被测介质的工况流量确定。
(7)供货商应提供对信号传输电缆的zui低技术要求。
(8)涡街流量计的准确度应优于±1.0%。
(9)涡街流量计的重复性应优于±0.2%。
(10) 供货商应提供被测介质的压力、组份不同对测量精度的影响。
(11) 正常运行时涡街流量计安装处不得有流体泄漏。
(12) 流量计的供电电源应采用24vdc。
3)流量计
(1)涡街流量计是速度式流量仪表,即通过旋涡的频率与流过流量计介质的平均流速成正比的关系,来测量介质的体积流量,适用于洁净液体的大中流量测量。
(2)流量计的设计结构和制造公差应满足允许相同尺寸和类型的流量计的测量部分可互换。应易于维修,可以方便地更换零部件。
(3)流量计的zui高设计工作压力应取所有承压部件(如流量计壳体、法兰等)中zui高设计工作压力zui低者。
(4) 流量计的内径应与买方提供的前、后直管段的内径保持一致。
(5)流量计与工艺管道采用法兰连接,供方应提供所有配对法兰及密封垫、紧固件等。
(6)供货商/制造商应提供流量计在zui大流量下的压力损失数据。
(7)流量计外壳上应有明确的流向标志。
(8)较大流量计应带有吊装用的吊环。
4)信号处理单元
(1)涡街流量计的信号处理单元(流量变送器)是将被测介质的流量准确、稳定、可靠的转换为标准的高频脉冲信号、数字信号(rs-485)、模拟信号(4~20ma)的装置。
(2)信号处理单元的供电电源应采用24vdc。
(3)信号处理单元应适于在户外和爆炸危险性场所安装,其防爆等级、防护等级应符合:第四部分4.2.3条的要求。
(4)信号处理单元应具有在现场对系统参数、各种常数进行重设的能力。且参数修改记录不可删除。
(5)信号处理单元应具有自诊断功能。至少应具有故障报警输出。
5)材料
(1) 流量计处于环境温度低于-25℃的条件下时,供货商/制造商应对流量计工作在zui高设计压力条件下所采用的材料耐压等级是否能满足要求进行核算并提供充分的书面依据。如果不能满足,应提高流量计的耐压等级或采用适当的材料。
(2)流量计与流体接触的所有部件的材质应使用适用于流体的材料制造,它们既不能影响流体的性质,又不能受流体的影响。
(3)流量计的所有外部零部件应该用抗腐蚀材料制造。
6)检验和测试
(1)工厂验收试验
所有仪表在出厂前应根据有关规范进行工厂试验,以证明所提供的设备在各方面均能完全符合买方的要求。
涡街流量计应依据相应的工业标准或其它的管理规范进行测试。
供货商应向买方提供每台仪表的出厂测试报告及质量检验报告,应是具有签署和日期的正式报告。
供方必须对所供设备进行100%的试验和检验,其内容至少应包括:
① 静态测试
数量检查(包括附件);
外观检验(包括漆面质量、表面光洁度等检验);
尺寸检测;
标牌标识是否完整、清晰;
防爆等级或本质安全设备的认证证书;
紧固件等是否有松动现象;
连接件形式、尺寸是否符合标准;
是否遵从焊接规范和标准;
材质是否与供货商提供的证明相符(内部件,外壳、连接件等)。
②动态测试
准确度;
滞后性;
复现性;
绝缘性能试验;
压力测试;
仪表功能测试;
其它内容测试。
③流量计标定
涡街流量计出厂验收时的标定方式为:100%样气(如空气)标定。流量计在安装前应在国内被授权的法定计量标定部门进行100%实流标定,标定不合格者由供方负全部责任。
实流标定的工况应与实际使用的工况类似,如流量、压力、温度、介质组份等,并应提供标定装置的测量不确定度数据。
流量计实流标定后,应采用标定系数消除仪表偏差,使流量计的性能达到*。流量计实流检定后应提供校准后的流量计系数。
供货商应提供法定计量标定部门出具的实流标定报告,并应以书面形式提供调整系数的详细说明。提供检定机构出具的附带原始检定数据和流量计校准系数的有效检定证书。
④现场验收试验
仪表设备运抵安装现场后,由供方与买方共同开箱检查,发现问题,由供方负责解决(即使在供货商工厂已试验过且已通过出厂验收)。
在现场验收试验前两星期,供方应事先提出试验计划,并须征得业主的批准。现场试验合格后,由用户预验收。
7)供货范围及界面
供货商应提供涡轮流量计和信号处理单元。
8)标记与铭牌
涡街流量计成品都应有指示流量方向的标记和铭牌,单位应为单位制。下列数据应在铭牌中标出:
—制造商和原产地名称
—产品名称、型号和系列号
—公称直径和zui大流速
—zui大工作压力
—出厂编码和生产标志
—制造测量仪器的许可证
—商标
6.3 过滤分离器
过滤分离器的设计与制造应遵循本技术规格书及相关标准规范的要求。
6.3.1 性能要求
1)在设计温度和设计压力下满足规定的强度要求,使用安全可靠,检查、维修方便。
2)设备应去除输送气体夹带的固体颗粒、粉尘和液滴。要求其过滤效率为:
粉尘: 1μm 99%;
3μm及3μm以下 99.1%;
5μm及5μm以下 99.9%。
液滴: 1μm 98%;
3μm及3μm以下 98.6%;
5μm及5μm以下 99.0%。
3)要求过滤设备正常操作的压降低于0.015mpa,且过滤元件的使用周期不少于12个整月。
4)为便于操作和更换滤芯,本过滤分离器应为带有快开盲板的卧式结构。
5)所配快开盲板应满足开闭灵活、轻便,密封可靠无泄漏,且有安全自动联锁装置。
6)单台过滤分离器的天然气处理量(详见数据单)。
7)设备外形美观。
6.3.2 强度计算
1)强度计算按gb150的规定执行。
2)焊接接头系数见过滤分离器数据单。
3)腐蚀裕量:2mm。
4)由支座、管系和内外部附件引起的应力集中,应采用垫板、加强件等降低此类局部应力,且需满足规范要求。
6.3.3 制造
1)在制造开始前,供货商应向业主提供设计总图,主要材质的性能,锻件及短节材料的化学成份及供货检验项目,制造工艺,质量保证措施等技术文件,提交份数按合同要求。对于国外承包商,还应提供各类相关标准原件或复印件。待业主书面审查同意后,方可开工制造。
2)过滤分离器的制造应严格按照gb150《钢制压力容器》的有关规定进行。设备的制造、检验与验收还应符合设计文件和图样的要求。
3)除遵照gb150的规定外,尚应满足下列要求:
①焊工资格应按《固定式压力容器安全技术监察规程》执行。
②壳体的对接焊接接头应采用gb/t985.1或gb/t985.2中规定的焊接形式。焊接中所选用的焊接方法及坡口形状应能保证焊接接头全焊透,不允许焊缝根部未熔合、未焊透及裂纹等缺陷存在。
③所有的对接焊接坡口必须机加工成型。
④焊接接头应做设计规定温度下的冲击试验,三个试样夏比v型缺口冲击功的平均值和单个试样夏比v型缺口冲击功的zui低值按数据单要求。
⑤焊缝余高应达到gb150的规定。
6.3.4 接管
1)所有壳体的开口接管(压力表接管除外)均采用对焊法兰连接。法兰等级应由分离器设计压力和设计温度确定,且应符合规范要求。
2)过滤分离器顶部和底部的接管、检测孔、放气孔、排污孔、清扫孔和人孔应与过滤分离器内壁齐平。
3)所有接管的开口不应位于纵焊缝上,并应避开环焊缝。
6.3.5 其他附件
1)在进行水压试验之前,所有的内部和外部附件都应先焊到过滤分离器上;
2)焊接附件与壳体连接,采用垫板和加强件时,应采用连续焊缝。
6.3.6 材料
制造过滤分离器的所有金属材料(锻件、板材或管材)应符合下列规定,并满足相应材料标准的其它要求。
1)金属材料用钢应采用电炉或氧气转炉冶炼的镇静钢。
2)不允许使用低价劣质材料,材料来源应经业主审批。
3)设计规定温度下材料及焊接接头三个试样夏比v型缺口冲击功的平均值和单个试样夏比v型缺口冲击功的zui低值按数据单要求。
4)产品用钢制锻件至少应符合nb/t 47008、nb/t 47009 相应级别锻件及以上的各项检验要求及其它技术要求。
5)当使用nb/t 47008、nb/t 47009、gb713标准规定以外的材料时,还应符合以下规定:
钢材的化学成份(熔炼分析):
c≤0.20%,p≤0.025%,s≤0.015%,
c.e.≤0.42 (c.e.=c mn/6 (cr mo v)/5 (ni cu)/15)。
6.3.7 检验
1)过滤分离器a、b类焊接接头应进行100%射线检测,符合nb/t47013规定的ⅱ级。必要时应进行≥20%超声复验,符合nb/t47013规定的ⅰ级,zui终的无损检测要求应满足数据单的要求。
2)接管与筒体的角焊缝表面应进行磁粉或渗透检测,符合nb/t47013规定的ⅰ级。
3)筒体内经dn≥800,接管公称直径dn≥200时,角焊缝进行超声波检测,符合nb/t47013规定的ⅰ级。
4)设备法兰、螺柱、螺母应做磁粉检测,确认无裂纹为合格。
6.3.8 组装
1)组装前应对全部零件进行检验,合格后才允许组装。
2)热处理后,不允许再在设备上施焊。
6.3.9 热处理
当设备需进行整体消除应力热处理时,热处理后不允许再在设备上施焊。随炉焊接试板热处理后,在设计规定温度下焊接接头三个试样夏比v型缺口冲击功的平均值和单个试样夏比v型缺口冲击功的zui低值按数据单要求。
6.3.10 压力试验
压力试验应采用水压试验。试验压力按站场工艺系统试验压力,但壳体的应力不超过0.9倍的标准屈服强度。
6.3.11 外观、尺寸
1)目测外形美观、表面光滑无凹坑。
2)焊接接头应打磨圆滑。
3)尺寸及公差满足规范及施工图要求。
4)快开盲板开、闭灵活。
6.3.12 铭牌
1)过滤分离器应配设铭牌。铭牌由耐腐材料制做,铭牌支架焊于过滤分离器外壁上,其位置应便于观察和接近。铭牌至少应包括以下内容:
(a)设计压力;
(b)容器类型;
(c)设计温度;
(d)介质;
(e)试验压力;
(f)制造日期;
(g)过滤分离器净质量;
(h)容积;
(i)设备编号;
(j)制造单位名称和制造许可证号码;
(k)制造单位对该过滤分离器产品编号。
2)铭牌上的文字应在现场条件下长期保持清晰可读。
3)铭牌上文字为中文,单位制为单位制。
6.4 快开盲板
快开盲板的设计与制造应遵循本技术规格书及相关标准规范的要求。
6.4.1 性能要求
1)在设计温度、设计压力下满足规定的强度要求,和耐腐蚀要求,应保证使用安全可靠。
2)能承受管线清管时清管器所产生的冲击力,而不致发生安全事故。
3)采用快开盲板,其快开盲板应开闭灵活,并带安全自锁装置,保证带压时无法开启。泄压为零并启动安全自锁装置后,快开盲板才能开启。安全自锁装置未安装好,设备无法升压。并在适当位置有警示标记。
4)快开盲板应带操作手轮或扳手,保证开闭灵活、方便、密封可靠、无泄露。
5)当快开盲板打开时应有定位装置,固定门锁,防止意外关闭。
6)快开盲板的关闭机构和转臂应固定在盲板上边缘法兰上,而不允许固定在设备筒体上。
7)应有安全设施来防止清管器接收器放压之前快开盲板的意外打开。
8)环形密封圈应保证在设计工况及以下的任何范围内,都应密封可靠,无泄漏。
9)所采用的人造橡胶的环形密封圈应能承受介质爆炸压力。并且满足在设计工况下输送流体的要求。
10)密封圈的材料应和输送流体兼容。
11)设备外表美观。
12)在安装环境下能全天候使用。
6.4.2 强度计算
强度计算与结构设计按gb150规定,并有必要进行分析设计或其它如应力测试。
6.4.3 制造
1)在制造开始前,供货商应向业主提供设计总图,主要材质的性能,锻件及短节材料的化学成份及供货检验项目,制造工艺,质量保证措施等技术文件,提交份数按合同要求。对于国外承包商,还应提供各类相关标准原件或复印件。待业主书面审查同意后,方可开工制造。
2)按gb150对主要受压元件及联接件的材质证明书进行确认,应按规定进行复检。
3)与外部壳体焊接连接的坡口,应机加工成形。坡口形式及尺寸见设计数据单。
4)外购产品到设备制造厂后,应由设备制造商组织,通知业主对产品进行验收,合格后方可进行组装。
5)供货商应提交快开盲板焊接工艺程序、焊接工艺评定、无损检测程序、焊后热处理程序供业主审查。供货商的焊接程序在业主发出书面同意后方可开始焊接。
①焊工资格及焊接程序应按《固定式压力容器安全技术监察规程》规定进行审查。
②快开盲板与外部的材质应具有良好的焊接性能。
③如有焊接接头应做冲击试验。其冲击值要求按数据单进行。
④角焊缝腰高应等于两相焊中较薄件的厚度,且为连续焊。
6)组装前应对全部零件进行检验,合格后才允许组装。
7)组装后应对组装焊缝进行消除应力热处理,热处理后和水压实验后应进行磁粉或着色渗透检测,符合jnb/t47013中i级规定。
6.4.4 材料
1)快开盲板与壳体连接端的材料应与壳体材料相匹配,并具有良好的可焊性。锻件性能应不低于nb/t 47008、nb/t 47009中的相应要求。
2)快开盲板受压元件的化学成分及力学性能。
3)化学成分:受压元件用钢应为由电炉、氧气转炉的全镇静钢,炉前分析应满足:
c≤0.23%、p≤0.025%,s≤0.015%。
4)锻件力学性能
锻件级别为nb/t 47008、nb/t 47009中的iii级或iv级的规定。
a. 抗拉强度:rm=450~600mpa
屈服强度:rt0.5≥270mpa
b. 冲击试验(夏比v型缺口)除常温冲击值满足nb/t 47008、nb/t 47009规定外,还应满足设计工况下的冲击功。
c. 热处理状态:正火 回火
d. 硬度检查:hb≤200
e. 超声检测
·检验区域:全部表面
·方法和标准:jb/t 4730
f. 满足gb150及其引用标准要求。
4)密封元件应采用耐温度性能较好的氟橡胶。并且满足材料的抗老化性能。
5)材料的其他性能还应满足相应规范、标准和本技术规格书的要求
6.4.5 检验
1)快开盲板所有a、b类焊接接头应按jb/t4730的规定进行射线检测;必要时还应进行超声复验。无损检测的比例和合格等级符合相应规范和标准的规定。
2)所有无损检测应遵循jb/t4730或asme ⅸ的规定的要求,并按照焊接工艺指导书规定进行。焊缝质量验收标准按gb150《钢制压力容器》对a类或b类接头的规定,x射线100%检测ii级合格,超声波100%检测i级合格。
3)无损检测的操作和分析应由具有资格的技术人员担任。
6.4.6 压力试验
每个快开盲板应在制造完毕后进行水压试验。压力试验程序按gb150执行。试验压力为1.5倍设计压力。水压试验应使用洁净水。
6.4.7 外观、尺寸及开闭检查
1)目测外形美观。
2)焊接接头光滑平整。
3)尺寸及公差满足规范要求。
4)快开盲板开、闭灵活。
5)满足本文件规定的功能要求。
6.4.8 铭牌
每一个快开盲板应使业主认可的方法进行标识。标识的位置易于观察,内容清晰,其安装可采用不锈钢支架和螺栓固定,但不允许直接将标识焊到设备上。需要标识的信息如下:
1)产品的名称和型号
2)设计压力和设计温度
3)适用介质
4)外形尺寸(外径×壁厚×总长)
5)产品质量
6)制造商名称
7)出厂日期和出厂编号。
7.2标识上的文字应在现场条件下长期保持清晰可读。
7.3标识上文字为中文,单位制为单位制。
6.5 水浴式换热器
水浴式换热器的设计与制造应遵循本技术规格书及相关标准规范的要求。
6.5.1 性能要求
1)在设计温度和设计压力下满足规定的强度要求,使用安全可靠,检查、维修方便。
2)在工作压力下,能达到规定的换热温度。
3)要求在正常操作工况下,压降小。
4)换热器应便于拆卸、更换、检查和维修方便。
5)供货商应考虑环境对设备的影响。
6)单台换热器的天然气处理量(详见数据单)。
7)设备外形美观。
6.5.2 强度计算
1)强度计算按gb150的规定执行。
2)焊接接头系数见过换热器数据单。
3)腐蚀裕量:2mm。
4)由支座、管系和内外部附件引起的应力集中,应采用垫板、加强件等降低此类局部应力,且需满足规范要求。
6.5.3 制造
1)在制造开始前,供货商应向业主提供设计总图,主要材质的性能,锻件及短节材料的化学成份及供货检验项目,制造工艺,质量保证措施等技术文件,提交份数按合同要求。对于国外承包商,还应提供各类相关标准原件或复印件。待业主书面审查同意后,方可开工制造。
2)换热器的制造应严格按照gb150《钢制压力容器》的有关规定进行。设备的制造、检验与验收还应符合设计文件和图样的要求。
3)除遵照gb150的规定外,尚应满足下列要求:
①焊工资格应按《固定式压力容器安全技术监察规程》执行。
②壳体的对接焊接接头应采用gb/t985.1或gb/t985.2中规定的焊接形式。焊接中所选用的焊接方法及坡口形状应能保证焊接接头全焊透,不允许焊缝根部未熔合、未焊透及裂纹等缺陷存在。
③所有的对接焊接坡口必须机加工成型。
④焊接接头应做设计规定温度下的冲击试验,三个试样夏比v型缺口冲击功的平均值和单个试样夏比v型缺口冲击功的zui低值按数据单要求。
⑤焊缝余高应达到gb150的规定。
6.5.4 接管
1)所有壳体的开口接管(压力表接管除外)均采用对焊法兰连接。法兰等级应由换热器设计压力和设计温度确定,且应符合规范要求。
2)所有接管的开口不应位于纵焊缝上,并应避开环焊缝。
6.5.5 其他附件
1)在进行水压试验之前,所有的内部和外部附件都应先焊到换热器上;
2)焊接附件与壳体连接,采用垫板和加强件时,应采用连续焊缝。
6.5.6 材料
制造过换热器的所有金属材料(锻件、板材或管材)应符合下列规定,并满足相应材料标准的其它要求。
1)金属材料用钢应采用电炉或氧气转炉冶炼的镇静钢。
2)不允许使用低价劣质材料,材料来源应经业主审批。
3)设计规定温度下材料及焊接接头三个试样夏比v型缺口冲击功的平均值和单个试样夏比v型缺口冲击功的zui低值按数据单要求。
4)产品用钢制锻件至少应符合nb/t 47008、nb/t 47009 相应级别锻件及以上的各项检验要求及其它技术要求。
5)当使用nb/t 47008、nb/t 47009、gb713标准规定以外的材料时,还应符合以下规定:
钢材的化学成份(熔炼分析):
c≤0.20%,p≤0.025%,s≤0.015%,
c.e.≤0.42 (c.e.=c mn/6 (cr mo v)/5 (ni cu)/15)。
6.5.7 检验
1)换热器a、b类焊接接头应进行100%射线检测,符合nb/t47013规定的ⅱ级。必要时应进行≥20%超声复验,符合nb/t47013规定的ⅰ级,zui终的无损检测要求应满足数据单的要求。
2)接管与筒体的角焊缝表面应进行磁粉或渗透检测,符合nb/t47013规定的ⅰ级。
3)筒体内经dn≥800,接管公称直径dn≥200时,角焊缝进行超声波检测,符合nb/t47013规定的ⅰ级。
4)设备法兰、螺柱、螺母应做磁粉检测,确认无裂纹为合格。
6.5.8 组装
1)组装前应对全部零件进行检验,合格后才允许组装。
2)热处理后,不允许再在设备上施焊。
6.5.9 热处理
当设备需进行整体消除应力热处理时,热处理后不允许再在设备上施焊。随炉焊接试板热处理后,在设计规定温度下焊接接头三个试样夏比v型缺口冲击功的平均值和单个试样夏比v型缺口冲击功的zui低值按数据单要求。
6.5.10 压力试验
压力试验应采用水压试验。试验压力按站场工艺系统试验压力,但壳体的应力不超过0.9倍的标准屈服强度。
6.5.11 外观、尺寸
1)目测外形美观、表面光滑无凹坑。
2)焊接接头应打磨圆滑。
3)尺寸及公差满足规范及施工图要求。
6.5.12 铭牌
1)换热器应配设铭牌。铭牌由耐腐材料制做,铭牌支架焊于过滤分离器外壁上,其位置应便于观察和接近。铭牌至少应包括以下内容:
(a)设计压力;
(b)容器类型;
(c)设计温度;
(d)介质;
(e)试验压力;
(f)制造日期;
(g)换热器净质量;
(h)容积;
(i)设备编号;
(j)制造单位名称和制造许可证号码;
(k)制造单位对该换热器产品编号。
2)铭牌上的文字应在现场条件下长期保持清晰可读。
3)铭牌上文字为中文,单位制为单位制。
6.6 调压系统
6.6.1 调压阀
1)应选用高可靠性的自力式调压阀,该自力式调压阀应是带有指挥器的调压阀。阀体、阀内件及密封件的材质及耐压等级应符合调压阀安装处的工艺条件及现场的环境要求。
2)自力式调压阀的指挥器动力源取自阀门的上游,为保证调节精度及指挥器的使用寿命,在指挥器的入口处应随设备配套带有互为备用的精细过滤器。
3)自力式调压阀在结构上应选用流通能力大的阀门,其调节范围应在zui大流通能力的5%~95%之间。其流通能力及可调比应满足工艺要求。
4)在zui恶劣的工况下,在距阀1m处的噪音不得超过85db。
5)自力式调压阀的调节精度应优于±2.5%。
6)自力式调压阀应附带位置变送器,可以将阀门的开度转换为4~20madc的标准模拟信号,输出至控制系统进行显示。该位置变送器的配置应合理,尽量选用标准、成型的产品,应能够正确反映阀门的开度。如果是本安信号,厂家负责配置安全栅。
7)位置变送器的防爆等级应不低于exdⅱbt4、防护等级不低于ip65。
8)自力式调压阀应带有就地机械指示装置,可就地指示阀门的开度。
9)自力式调压阀的所有测量管路应由供方提供,测量管路应采用不锈钢材质。若由于环境温度、水露点等原因,将导致指挥器、测量管路发生结冰现象时,应对指挥器、测量管路通过电加热器进行加热。供方在做管路系统配置时,应充分考虑杜绝和消除冰堵的措施。
10)应能通过调整单元或更换弹簧及其它部件(不必拆卸阀体),快捷、方便地改变调压阀的设定值,以保证今后压力改变时,仍能满足工艺要求。用于现场改变设定值的调整单元应具有保护措施,设定值设定后应能锁定,以免由于人为误操作造成压力控制系统异常工作。
11)自力式调压阀应易于维护、维修。
12)自力式调压阀阀座的泄漏应能够达到asme fci 70-2标准中的第ⅳ级。阀座的泄漏应根据标准asme fci-70-2 或mss-sp-61 分类。当阀门出现故障时,应处于关闭位置。
13)正常运行时,调压阀安装处不得有天然气泄漏,由于工作膜片损坏而导致的故障,其泄漏量不得超过30l/h。
14)自力式调压阀阀体上应有明确的流向标志。
6.6.2 超压切断阀
1)超压切断阀宜与调压器分体串联,设置于调压器上游;
2)超压切断阀宜采用阀口通径结构设计。
3)超压切断阀控制方式为自力式,人工复位。
4)超压切断阀切断精度≤±1%(ag1),切断响应时间≤1.0秒。
5)超压切断阀的开关带阀位显示且其信号具有远传功能, 切断信号输出装置为隔爆型,防爆等级不低于 exdⅱbt4。切断信号输出接点(无源)容量为 24vdc 2a(zui小)。
6)超压切断阀阀座、阀杆、导压管应为不锈钢材料,皮膜和密封应为丁腈橡胶。也可使用与上述性能相当或更好的材料。 其它部件材料应符合相关标准的要求。 承压部件材料应根据相关标准提供化学成分分析和机械性能试验的证书。
7)超压切断阀的制造、试验应符合标准要求并提供有关认证。超压切断阀必须进行强度试验、气密性试验和耐久性试验,试验要求应符合相关标准的规定并提供有关测试报告。
6.7 加臭系统
6.7.1 性能要求
1)加臭系统单独成橇,并安装在调压计量加臭橇上。
2)加臭装置应能够满足环境温度使用条件。
3)加臭装置应适应使用符合 cjj/t 148 要求质量的加臭剂,且加臭能力应满足该规程的要求;
4)加臭装置应能够自动将加臭剂注入到燃气管道内,对于不同燃气流量,应保持加臭剂浓度基本恒定,加臭精度±5%,并能保证加臭连续运行;
5)加臭装置应能对加臭剂的输出量进行监测和标定;
6)加臭装置应具有自动加臭、手动加臭和编程定量加臭三种运行模式;
7)加臭装置应具有燃气流量、加臭剂注入量等相关运行参数的储存、打印和数据通讯功能;
8)如业主或设计提出多点加臭的功能要求,加臭装置应能够满足。
6.7.2 组装
设备组装在钢结构底座上。
6.7.3 加臭剂注入喷嘴
1)加臭剂注入喷嘴结构设计应能够保证臭味剂进入管道后迅速气化,与燃气充分混合,不允许在管道内出现液滴。
2)加臭剂注入喷嘴上部应设置截止阀和止回阀。
3)加臭剂注入喷嘴与燃气管道接口尺寸应不小于dn15,压力级别与燃气管道设计压力相同。
4)加臭剂注入喷嘴应设置在调压计量设备后的水平钢制管道上。
6.7.4 隔膜计量泵
1)为每个加臭点配置的隔膜计量泵应设置备用。
2)隔膜计量泵输出加臭剂的压力宜比加注点燃气管道zui高工作压力高 1.0mpa 以上。柱塞式隔膜计量泵应设有无级设定的安全阀。
3)隔膜计量泵单行程输出流量应可调节,并配置单行程输出量的标定器。隔膜计量泵的输出频次应能够通过控制系统进行控制和调节,其冲程频率应不低于100次/秒。
4)需自动切换的隔膜计量泵入口必须设置电磁阀。
5)隔膜计量泵入口设置过滤器。
6)隔膜计量泵出口设置与加臭剂储罐连通的回流管。
7)隔膜计量泵及电磁阀安装位置为爆炸性气体环境危险区域 i 区,电气防爆等级不得低于exdⅱbt4。
8)隔膜计量泵应有故障报警反馈至控制器。
6.7.5 加臭剂储罐
1)加臭剂储罐应按cjj/t 148 的规定,执行国家现行标准gb150进行设计、制造、检验、验收。
2)加臭剂储罐为常压使用,其设计压力不得低于0.1mpa,并应配备呼吸阀或避免罐内超压和负压的装置。加臭剂储罐配置相应的检测仪表及安全保护装置,并按cjj/t 148的规定标有危险警示标志。
3)加臭剂储罐容积应符合cjj/t 148的规定,能够保证加臭剂充装量不大于 90%,且储存时间不超过加臭剂的保质期。
4)加臭剂储罐应有显示加臭剂储量的液位计。其液位计宜采用磁浮子液位计。磁浮子液位计应符合gb/t 25153的规定。
5)加臭剂储罐应配备具有就地显示及远传显示功能的液位计,其远传信号(4~20ma)送至加臭控制系统。
6)加臭剂储罐应设置呼吸阀和排空管,呼吸阀和排空管出口须配备吸收器,吸收器出气管路应装设阻火器。
7)加臭剂储罐应按 cjj/t 148 的规定设快速上料接口和气体压料接口。
6.7.6 阀门与管道
1)输送加臭剂的不锈钢管zui小内径应大于10mm,其标准应采用gb/t 14976。
2)管道焊接及无损检测应按照gb 50235 规定执行。
6.7.7 控制器
1)控制器安装在非防爆区的控制室内,plc 或单片机控制器宜为盘装式。
2)加臭装置控制器应具有 cjj/t 148 的基本功能,自动—手动—编程三种运行模式控制计量泵开关和加臭剂输出量、 计量泵故障报警和显示、 加臭剂储罐液位显示和高低限液位报警等功能;
3)控制器应根据燃气流量自动控制注入的加臭剂量, 其燃气流量信号为标况瞬时流量,控制器应有燃气流量信号输入接口,如接收4~20madc模拟电流信号,输入接口应3路以上。
4)控制器要求有两个数据通讯接口,一路通往站区控制系统通讯,一路通往打印设备。
5)控制器运行数据的通讯接口标准和协议为modbus rtu,rs485。
6.7.8 其他
1)加臭装置应配置气体压料装置及相关的压力表、连接管、阀门、接头等配件;
2)电气设备防护等级不低于 ip65;
3)加臭装置应与场站的防雷和防静电接地系统相连接,且接地电阻应小于 10ω;
4)供电电源:交流(ac)50hz 220v±10v,工作电流≤1a,功率≤1kw;
5)置于防爆区域内的现场设备接线应配置防爆接线盒。
6.7.9 材料
1)橇座
橇座材料采用型钢,型钢应满足强度和刚度要求,且厚度不应小于5mm。
2)加臭剂储罐
加臭剂储罐材料采用不锈钢304或316。
3)阀门
与加臭剂直接接触的阀门材质采用不锈钢304或316。
4)隔膜计量泵
泵体材料应采用不锈钢。
5)管道、管件
与加臭剂直接接触的管道、管件材质应采用不锈钢 304 或 316。
6)密封件
与液态或接近饱和浓度气态加臭剂接触的密封材料,应采用聚四氟乙烯(hg/t 2899)。
8)紧固件
紧固件材料应符合hg/t 20613规定。
9)电缆及仪表接线
电缆及绝缘导线应采用铜芯阻燃电缆,信号电缆的线芯截面积不应小于 1.5 mm2,电源电缆的线芯截面积不应小于2.5mm2。
10)其他
与液态加臭剂非直接接触的金属部件,可采用碳素钢材质,材料标准应符合 gb/t710的规定,外表面应做防腐处理。
6.7.10 铭牌
加臭系统应设置铭牌,铭牌由不锈钢制作,其位置应便于观察,内容至少应包括以下项目:
—装置名称;
—工作压力;
—额定加注量;
—额定电压、功率;
—储罐公称容积;
—外形尺寸、重量;
—生产厂名、制造年月;
—商标。
6.8 阀门
6.8.1 通用性能要求
1)阀门的设计与制造应遵循本技术条件及相关标准规范的要求。
2)阀门应能满足连续运行30年以上,且相关性能(操作与密封)能长期满足工况要求。
3)阀门操作维护方便,同时其维护工作应不能影响其所配执行机构或控制系统的正常工作。
6.8.2 球阀
6.8.2.1 性能要求
1)对焊连接阀门的焊接坡口应执行asme b31.8的规定,法兰连接阀门配对法兰执行标准为asme b16.5,法兰与管道的连接端应保证材质强度的适配性和可焊性,配对法兰焊接端外径与接管尺寸一致(阀体结构形式、端部连接方式、焊接端接管规格及材质详见数据单)。
2)配执行机构的阀门及其阀杆应能承受执行机构的输出扭矩,阀门能承受的zui大扭矩由阀门供货商提供给执行机构供货商供选型用。阀门供货商应给执行机构供货商提供开关阀门所需的扭矩。执行机构输出的zui小扭矩能保证阀门在全差压下的开启。
3)供货商应提供阀门能承受的zui大弯矩。所有阀门选材除应符合api 6d和有关阀门材料标准的要求外,还应能适应气候条件、环境温度、工作介质及操作条件。
4)对于与管线的连接采用焊接形式的阀门,阀门与管道的连接端应保证材质强度的适配性和可焊性,阀门对焊连接端坡口应执行asme b31.8(接管规格及材质详见数据单)。
5)阀座和阀杆应有二次密封,阀座应有独立的注脂口,注脂口可带压更换。作为紧急需要时使用,推荐的密封脂应能满足功能要求,密封脂应能保证在技术条件和数据单中规定工况条件下性能稳定,且在天然气中不挥发、干裂,在油中不溶解,不起化学变化。
6)直径≥4″的阀门应为固定球双截断和泄放(dbb)的阀门,配有双活塞效应的阀座, 以保证进口端和出口端的密封,并要求达到零泄漏,同时要求每一侧都能承受全压差,并应定期检查阀腔泄压阀的泄压能力。
7)手动操作的阀门应便于人工操作,公称直径为3″及以上球阀应带蜗轮蜗杆齿轮传动机构、手轮,公称直径为2″及以下球阀应带手柄,手柄长度≤600mm。手轮和手柄的操作力不大于250n。
8)所有≥6″的阀门应便于在维修、更换、运输或安装过程中用机械装置吊装。
9)所有阀门均应为防火安全型,且能满足api6fa和api 607的要求并提供其证书,具体密封形式见数据单。
10)阀门应装有现场阀位指示器,以确定阀门的开关位置。所有配有执行机构的阀门应满足以下要求:
(1)开、关扭矩限位器应与阀门和执行机构的类型保持一致。
(2)应装有开、关的机械限位装置。
(3)阀门应装有阀位指示器,以确定阀门的开关位置。
11)运输前裸露金属面的部件和设备应涂上防锈剂保护(袖管距管道焊接端150mm除外),该防锈剂在现场条件下不会融化成液体而流失。
12)供货商应在投标技术文件中详细解释阀杆防爆喷设计原理及结构。
6.8.2.2 材料
1)除非另有规定,用于制造阀门的材料均应符合api 6d和有关阀门材料标准的要求,使阀门的性能能适应气候条件、环境温度、工作介质及操作条件的要求,并能保证使用寿命。
2)主要零部件和标准件应提供材料化学成分、机械性能、无损检测报告。
3)阀体应采用锻钢,对端部连接为焊接的阀门,应保证阀体与相应管道、管件之间的可焊性(供货商应提供焊接工艺评定或焊接试板)。
4)阀杆的材料应为aisi 4140 、aisi 1040或aisi 4130,球体和阀座应是锻钢。球体、阀座、阀杆和其他内件表面应化学镀镍,涂层厚度不小于50μm(0.002inch),硬度达到hv 650~750,涂层厚度均匀,以保持硬度和强度。
5)阀座软密封材料采用防压力爆破橡胶材料、ptfe或nylon。
6)阀座预紧弹簧应采用inconel x-750材料制成。
7)不排除制造商也可以使用经实践证明性能更优的上述阀件的制造材料以保证制造商对阀门质量、性能与使用寿命承诺,但应事先得到业主认可。
6.8.2.3 检验和测试
1)所有组装完后的阀门出厂之前都需经过检验。阀门的检验与测试均应遵循api 6d、api 598、ansi b16.34的要求。这些检验应根据业主认可的供货商的书面检验程序执行。进行阀座试压前应首先开关阀门2~3次,试验压力和试验时间应遵照api 6d第五章的要求。在测试后,应排净阀体内的试验介质。所有的试验均应在不使用密封脂的情况下进行。
投标商应在标书中提供测试大纲,测试至少应具有以下内容:
a 阀体水试压
b 全压差下开阀试验,记录开阀时所需扭矩
c 阀座水压密封试验(包括试压前3次以上的无故障启闭试验)
d 双截断和排放(dbb)功能阀座水试压
e 双活塞效应功能阀座水试压
f 阀座低压气密封试验
g 内腔清洁度检验
2)所有的检验和测试应在阀门表面处理和喷漆前进行。
3)所有的焊接均应按照美国焊接协会以及asme锅炉和压力容器标准第ix章的要求进行。所有焊缝应有消除焊接应力的措施。供货商应向业主提交焊缝检验标准与验收报告。
4)对配有执行机构的阀门应由阀门供货商将阀门与执行机构在工厂内组装后进行整体功能测试,以确保阀门在数据单规定下的zui大压差条件下具有满意的开、关性能。
5)配有执行机构的阀门装配后应在0到100%的额定行程中进行全开、全关操作的检查。所有附件的状态包括机械阀位指示应被确认和记录。
6)阀门和执行机构在工厂调试后应做*性定位标志,确保现场组装时不致于发生开关位置的变化。
7)球阀应能承受1.5倍设计压力/4小时的现场试验压力要求。所有阀门需要现场进行强度和气密性试验。供货商需提供现场进行水压试验和气密性试验的试验程序。
6.8.3 贸易计量后阀门
贸易计量后阀门选用dbb球阀或强制密封球阀。
6.8.3.1 性能要求
1)dbb球阀和强制密封球阀阀座和阀杆应有二次密封,作为紧急需要时使用,阀座应有独立的注脂口,注脂口可带压更换。注脂系统内部应设止回阀,并保证注脂过程及注脂阀门更换过程中性能安全可靠。各注脂系统应通畅、出脂口正确。推荐的密封脂应能满足功能要求,密封脂应能保证在技术条件和数据单中规定工况条件下性能稳定,且在天然气中不挥发、干裂,在油中不溶解,不起化学变化。
2)阀门密封应采用金属密封 软密封结构,泄漏等级应满足gb/t13927 中的a 级或iso 5208 中*的要求,并应具有在阀门关闭后可对其密封泄漏进行检测的功能。
3)所有≥6″的阀门应便于在维修、更换、运输或安装过程中用机械装置吊装。
4)所有阀门均应为防火安全型,且能满足api6fa 或api 607 的要求并提供其证书,具体密封形式见数据单。
5)所有配有执行机构的阀门应满足以下要求:
(1)开、关扭矩限位器应与阀门和执行机构的类型保持一致。
(2)应装有开、关的机械限位装置。
(3)阀门应装有阀位指示器。
6)在运输前,裸露金属面的部件和设备应涂上防锈剂保护,该防锈剂在现场条件下不会融化成液体而流失。
7)手动操作的阀门应便于人工操作,阀门应带蜗轮蜗杆齿轮传动机构、手轮或手柄,手柄长度≤600mm。手轮和手柄的操作力不大于250n。(规定手柄手轮的使用范围)
8)阀门应有防静电设计。防静电实验应满足api 6d 中的要求。
9)阀门应有加锁装置
10)阀门采用法兰连接形式与管线进行连接时,数据单中无特殊要求的情况下,供应商应提供相应配对法兰及配套螺栓、螺母、垫片,并应满足以下要求(具体要求详见数据单):
a)dn600 及以下法兰执行标准为asme b16.5。
b)dn550 法兰执行标准为mss-sp-44。
c)dn600 以上法兰执行标准为asme b16.47 a 系列。
d)法兰的端部坡口应遵守asme 的要求。
e)法兰与管道的连接端应保证材质强度的适配性和可焊性。
f)class600 及class600 以下压力等级法兰优先采用rf\wn 形式。
g)class900 压力等级法兰优先采用rtj\wn 形式。
6.8.3.2 dbb 球阀要求
1)阀门应为固定球双截断和泄放(dbb)的全通径阀门,且满足双向零泄漏的要求。
2)用于输气管道的阀门应配有双活塞效应的阀座, 且每一侧应承受全压差。
3)位于防火区域内的球阀宜设置外泄压阀。
4)公称直径大于或等于dn100 的阀门应设阀腔放空、排污,排污管应由阀门底部开口以便将阀体内的杂质排出,放空管应在阀体顶部开口安装以便对阀腔进行放空和清洗。阀门供货商需考虑阀体本身排污的操作方便性,地上安装的公称直径大于或等于dn300 的阀门本体排污管线应引出至阀门本体外。放空管、排污管与阀体应采用焊接连接。放空和排污管线均应安装双阀,靠近阀体的阀门为焊接连接的球阀,末端应设置螺纹连接的放空阀或排污阀,端部应配朝向地面的弯头(带堵头)。地上dn250 以下阀门放空口、排污口只安装隔离球阀,采用螺纹连接。阀门放空和排污的方向不应影响阀门操作维护,同时其维护工作应不能影响其所配执行机构或控制系统的正常工作。
5)球阀及其附带的辅助阀门(如放空、排污管线上的球阀等)的泄漏等级均应达到gb/t13927 中的a 级,在试验压力持续时间内无可见泄漏,球阀阀座的密封应采用金属密封加非金属密封的组合密封方式。
6)除非数据单中另有规定,dn200 及以上的阀门上应有支座。
6.8.3.3强制密封球阀要求
1)强制密封阀应该满足单向零泄漏的要求,应采用强制密封的形式。
2)阀门应采用提升式轨道阀杆,达到无摩擦操作方式。阀的密封是由执行机构提供的强制力实现的,不依赖于管线的压力。
3)阀门应采用顶装结构,阀门的设计与制造应遵循本技术规格书及api 6d、api 607、api 6fa 等相关标准规范的要求。
4)阀门应内嵌阀球销钉。销钉要求与阀门同寿命。拆卸阀门的内部零件时,应通过拆卸阀门顶装式的阀盖实现
5)阀门应配有检测泄漏装置,通过泄漏排放口可以动态检测自身密封性。泄漏排放口的连接尺寸为npt1/2″或npt1/4″。
6)阀门应设计成自清洗式,即当阀门在关闭和开启时,高速流体冲刷可以对阀门的球体表面和阀座实现自动的清洗。
7)为了便于阀门现场维护,特别是管线带压情况下对阀杆密封的修复,阀杆的密封设计应采用可注入式盘根设计或压盖式设计。
8)阀座结构应为可更换设计,确保阀门关闭时可在线检验阀座密封的完好性。
9)在阀体一侧应标注阀门安装方向。
6.8.3.4 材料
1)除非另有规定,用于制造阀门的材料均应符合api 6d 和有关阀门材料标准的要求,使阀门的性能能适应气候条件、环境温度、工作介质及操作条件的要求,并能保证使用寿命。
2)主要零部件和标准件应提供材料化学成分、机械性能、无损检测报告。
3)dbb 球阀阀体及阀球应采用锻钢。不锈钢阀座表面硬化处理可不限于镀镍方式。
4)强制密封球阀阀体/阀盖/阀球采用铸造碳钢wcb/wcc/lcc 或锻钢astm a350 lf2 或同等材料。参与密封的球体和阀座密封面处应堆焊硬质合金或其他更好硬化工艺,应进行消除应力热处理,硬度、厚度等机械性能满足工况要求,并能保证在使用期间对阀门密封与操作性能的要求。
5) dbb 球阀的阀杆的材料应为aisi 4140 或aisi 4130。强制密封球阀的阀杆的材料应为aisi 8620或astm a564 630 或同等材料。强制密封旋塞阀的阀杆的材料应与旋塞一致或采用更好材料。
6)阀门的配对法兰、螺栓、螺母和垫片应由阀门制造商提供。配对法兰的材质与管线具有可焊性,接管管线的尺寸、规格标准见数据表。配对的法兰材质zui小屈服强度应≥70%管线zui小屈服强度,并保证在zui高使用温度下其许用工作压力不低于管道设计压力。阀门配对法兰常用材质见下表:
接管材质 配对法兰材质
常温工况 低温工况
l245 astm a105(-29℃以上)、16mn 锻钢(-20℃以上)
astm a350 lf2 ( -29~-46 ℃ )、16mnd 锻钢(-20~-40℃)
l360 astm a350 lf6 class1(-29℃以上)、16mn 锻钢(-20℃以上)
astm a350 lf6 class1(-29~-46℃)、16mnd 锻钢(-20~-40℃)
l415/l450/l485 astm a350 lf6 class2(-29℃以上)、16mn 锻钢(-20℃以上)
astm a350 lf6 class2(-29~-46℃)、16mnd 锻钢(-20~-40℃)
7)螺栓材料为 astm a193 gr. b7/ astm a320 gr. l7,螺母材料为astm a194 gr. 2h/ astm a194 gr.7。阀门上所有螺栓螺母要求镀锌,保证其防腐性能,并保证螺栓螺母的机械性能。
8)阀座软密封材料采用防压力爆破橡胶材料(对于输油管道,要求橡胶材料耐油)、ptfe 或nylon。
9)阀座预紧弹簧应采用inconel x-750 材料制成;阀座板式预紧弹簧应采用aisi 4130 材料制作,并进行化学镀镍防腐处理。
10)不排除制造商也可以使用经实践证明性能更优的上述阀件的制造材料以保证制造商对阀门质量、性能与使用寿命承诺,但应事先得到业主认可。
6.8.3.5 检验和测试
1)所有组装完后的阀门出厂之前都需经过检验。阀门的检验与测试均应遵循api 6d、api 598、ansib16.34、gb/t 13927、iso 5208 的要求。这些检验应根据业主认可的供货商的书面检验程序执行。进行阀座试压前应首先开关阀门2~3 次,试验压力和试验时间应遵照api 6d 第五章的要求。在测试后,应排净阀体内的试验介质。所有的试验均应在不使用密封脂的情况下进行。
投标商应在标书中提供测试大纲,测试至少应具有以下内容:
dbb 球阀:
a 阀体水试压
b 全压差下开阀试验,记录开阀时所需扭矩
c 阀座水压密封试验(包括试压前3 次以上的无故障启闭试验)
d 双截断和排放(dbb)功能阀座水试压
e 双活塞效应功能阀座水试压
f 阀座低压气密封试验
g 内腔清洁度检验
强制密封球阀:
a 阀体水试压;
b 全压差下开阀试验,记录开阀时所需扭矩;
c 阀座水试压(包括试压前3 次以上的无故障启闭试验);
d 阀座低压气密封试验;
e 内腔清洁度检验。
2)所有的检验和测试应在阀门表面处理和喷漆前进行。
3)所有的焊接均应按照美国焊接协会以及asme 锅炉和压力容器标准第ix 章的要求进行。所有焊缝应有消除焊接应力的措施。供货商应向业主提交焊缝检验标准与验收报告。
4)阀门应能承受1.5 倍设计压力/4 小时的现场试验压力要求。所有阀门需要现场进行强度和气密性试验。供货商需提供现场进行水压试验和气密性试验的试验程序。
6.8.4 节流截止放空阀
6.8.4.1 性能要求
1)阀门主要用于紧急情况下或检修时的放空以及手动节流的工况。同时要求阀门全开时,流通面积不少于阀门公称通径相应面积的80%。
2) cv值要求详见数据单。
3)阀门应同时具有节流与截止作用,在控制流量时应能连续的平稳操作,在关闭时应能达到零泄漏的要求。同时,零泄漏的功能不能以频繁更换密封材料来实现。
4)节流截止放空阀设计应考虑在启/闭全压差条件下稳定操作,操作扭矩小,耐气流冲刷、耐擦伤、耐磨损、耐腐蚀,使用寿命长。
5)应尽量减少噪音,其要求见数据单。
6)为节省工艺管线安装空间,便于操作,要求所有手动阀门均为手轮操作,手轮的操作力不大于250n。
7)所有阀门均为法兰连接,配对法兰制造标准详见数据单。供货商提供配对的对焊法兰、螺栓、螺母和垫片,法兰与管道的连接端应保证材质强度的适配性和可焊性(接管规格及材质详见数据单)。要求法兰能够承受的zui大压力不小于阀门的公称压力。
8)阀座和阀杆应有二次密封,阀座应有独立的注脂口,注脂口可带压更换。作为紧急需要时使用,推荐的密封脂应能满足功能要求,密封脂应能保证在技术条件和数据单中规定工况条件下性能稳定,且在天然气中不挥发、干裂,在油中不溶解,不起化学变化。
9)采用金属和非金属双重密封,以保证密封性能。
10)所有的辅助连接件应该与阀门的压力等级相一致。连接件采用适当的支架和支撑安全地固定在阀体上。
11)dn150及以上的阀门上应设有吊耳,以便维修、更换、运输和安装。
12)所有阀门应有足够的强度和刚度,能保证阀门在现场使用条件下安全运行。
6.8.4.2 材料
1)阀门的材料应能满足阀门所处工况的要求,并能保证使用寿命。
2)主要零部件和标准件应提供材料化学成分、机械性能、无损检测报告。
3)阀体材质应为铸钢,阀芯、阀芯套、阀座和阀杆材料为不锈钢,阀座密封面、阀芯和节流孔表面堆焊钴铬钨合金。
4)软密封材料采用viton、ptfe。
5)阀门配套的紧固件材质应满足本技术条件和数据单中规定工况条件下的要求。
6)不排除制造商也可以使用经实践证明性能更优的上述阀件的制造材料以保证制造商对阀门质量、性能与使用寿命承诺,但应事先得到业主认可。
6.8.4.3 检验和测试
1)阀门的检验和测试应严格按gb/t13927、jb/t9092与 api std.598执行。投标商应在标书中提供测试大纲。
2)所有组装完后的阀门出厂之前都需经过检验。这些检验应根据供货商的书面检验程序执行。且进行阀座试压前应首先开关阀门2~3次,在测试后,应排净阀体内的试验介质。阀门试压应包括以下内容(a-e)。
a 阀体水试压
b 全压差下开阀试验,记录开阀时所需扭矩
c 阀座水压密封试验(包括试压前3次以上的无故障启闭试验)
d 阀座低压气密封试验
e 内腔清洁度检验
3)业主有权随时根据需要进行检查。
4)所有的检验和测试应在阀门表面处理和喷漆前进行。
5)对配有执行机构的阀门应由阀门供货商将阀门与执行机构在工厂内组装后进行整体功能测试,以确保阀门在数据单规定下的zui大压差条件下具有满意的开、关性能。
6)配有执行机构的阀门装配后应在0到100%的额定行程中进行全开、全关操作的检查。所有附件的状态包括机械阀位指示应被确认和记录。
7)阀门和执行机构在工厂调试后应做*性定位标志,确保现场组装时不致于发生开关位置的变化。
8)阀门应能承受1.5倍设计压力/4小时的现场试验压力要求。所有阀门需要现场进行强度和气密性试验。供货商需提供现场进行水压试验和气密性试验的试验程序。
6.8.5 阀套式排污阀
6.8.5.1 性能要求
1)阀门主要用于紧急情况下或检修时的排污。同时要求阀门全开时,流通面积不少于阀门公称通径相应面积的80%。
2)阀套式排污阀应同时具有节流与截止作用,在控制排污流量时应能连续的平稳操作,在关闭时应能达到零泄漏的要求。同时,零泄漏的功能不能以频繁更换密封材料来实现。
3)阀套式排污阀要求密封可靠、耐冲刷、排污性能好、使用寿命长,阀门至少满足30年的设计寿命与相应的性能指标。
4) 排污阀应设排污孔,必要时可以打开,清理阀内污物,并防止污物堵塞。
5)为节省工艺管线安装空间,便于操作,要求所有手动阀门均为手轮操作。手轮的操作力不大于250n。
6)所有阀门均为法兰连接,阀门端部法兰制造标准按照asme b16.5 执行。供货商提供配对的凸面对焊法兰、螺栓、螺母和垫片,法兰与管道的连接端应保证材质强度的适配性和可焊性(接管规格及材质详见数据单)。
7)采用金属和非金属双重密封,以保证密封性能。
8)所有阀门应便于在维修、更换、运输或安装过程中用机械装置吊装。阀门应有足够的强度和刚度,能保证阀门在现场使用条件下安全运行。
6.8.5.2 检验和测试
1)阀门的检验和测试应严格按gb/t13927与jb/t9092执行。检验和测试应在阀门表面处理和喷漆前进行。
2)所有组装完后的阀门出厂之前都需经过检验。这些检验应根据供货商的书面检验程序执行。投标商应在标书中提供测试大纲。
3)业主有权随时根据需要进行检查。
6.8.6 先导式安全泄放阀
6.8.6.1 性能要求
1)安全阀应是全启式、先导型(寒冷地区和气质不达标的情况除外),应为失效开,开启形式应符合输气站场的需求。
2)应由主阀和外部的导阀组成,当主阀开启时,不允许有主气流流经导阀放空。导阀失效时不影响主阀的开启。
3)安全阀应有设定值调节装置,使安全阀的设定值可以调节。
4)先导式安全阀应安装导阀入口过滤器,导阀应有放空口。
5)安全阀应配有现场测试接口。
6)安全阀的进口和出口应采用法兰连接,按照asme b16.5规定执行。供货商提供配对的凸面对焊法兰、螺栓、螺母和垫片,法兰与管道的连接端应保证材质强度的适配性和可焊性(接管规格及材质详见数据单)。
7)进、出口端面到阀门中心的尺寸应遵照api 526的规定。
8)阀门规格尺寸选择应依据api 520规范,并根据数据单中提供的参数进行选型,制造商应保证所供阀门有足够的安全可靠性。
9)当管线压力小于等于zui大操作压力时,安全阀应能保证密封,达到零泄漏。
当安全阀达到设定值时应能迅速起跳泄放压力,安全阀起跳压力和设定值之间的精度为±1%~3%,回座压力精度为4%~6%;厂家应提供具体指标及机构对该指标的测试证明报告,并得到业主认可。
当管线压力回落至zui大操作压力时,安全阀应关闭。
要求安全阀在多次操作后,应仍能准确起跳和复位,且关闭严密。
10)制造商应根据数据单的参数核算安全阀进出口尺寸。
6.8.6.2 材料
1)阀门材料的选择应使阀门的性能满足阀门所处工况的要求,并能保证使用寿命。
2)主要零部件和标准件应提供材料化学成分、机械性能、无损检测报告。
3)主阀阀体材料应为碳钢,材质详见数据单。
4)喷嘴应为不锈钢堆焊硬质合金,喷嘴组件应具有足够的耐冲刷能力。
5)活塞、主阀和导阀间的接管材料为不锈钢。
6)导阀主要金属部件材料为不锈钢。
7)弹簧为inconel x-750。
8)阀座软密封材料采用viton、ptfe或nylon。
9)不排除制造商使用经实践证明性能更优的上述阀件的制造材料以保证制造商对阀门质量、性能与使用寿命承诺,但应事先得到业主认可。
6.8.6.3 检验和测试
1)所有组装完后的阀门出厂之前都需经过检验。阀门的检验与测试均应遵循api 520、api 526、api 527、asme code 和ansi b16.34的相关要求,这些检验应根据业主认可的供货商的书面检验程序执行。业主认为必要时,可参照相应国家标准。
2)这些检验应根据制造商的书面检验程序执行。在测试后,应排净阀体内的试验介质。
投标商应在标书中提供测试大纲,测试至少应具有以下内容:
—阀体水压试验
—阀座气压试验
—阀座泄漏试验(零泄漏)
—功能测试
—设定压力测试(包括起跳压力,排放压力,回座压力等)
—突开试验、稳定性试验、精度测试
—规范规定的其它试验。
3)所有的检验和测试应在阀门表面处理和喷漆前进行。
4)业主有权随时根据需要进行检查。
6.8.7 止回阀
止回阀选用旋启式全通径止回阀。
6.8.7.1 性能要求
1)旋启式全通径止回阀应是api spec 6d 图8所示的类型。
2)旋启式全通径止回阀应装配有外伸的手动操作装置、液压阻尼缸和平衡锤,并通过旋转枢轴与舌板连接。平衡锤的位置应是可调整的,并具有阀门开位锁定功能。阀门关闭应无回流、撞击现象。
3)液压阻尼缸内的液体介质应适合于阀门工作环境条件的要求。液压阻尼缸应为整体免维护式,带导杆和外部液压管的阻尼器不应被采用。阀门的关闭速度可以通过液压阻尼装置进行调节。供货商应在投标技术文件中提供调节方法及液压阻尼缸内的液体介质类型和技术参数,如适用的温度范围等。
4)供货商应在投标技术文件中提供舌板旋转枢轴防锈死措施。
5)旋启式全通径止回阀应有螺栓紧固的阀盖,可在线维修或更换舌板和密封,阀盖应满足api 规范的标准产品,其端面、垫片等应是标准产品,以便更换。
6)旋启式全通径止回阀的密封性能应通过旋启舌板和阀座的紧密配合和相应的密封来达到。
7)旋启式全通径止回阀上与旋启舌板相接触的阀座密封应制造成两部分:硬质合金和适用于输送介质的软材料;在旋启舌板和阀座密封表面应堆焊一层硬质合金(如slite合金或同等性能的材料),使阀门在关闭时阀座和舌板保持精密接触,并应装配成在软密封材料过度磨损或损坏时保证密封。
8)止回阀舌板旋转枢轴应采用o型圈或v型密封和填料密封,旋转枢轴的填料可在线更换。旋转枢轴应具有密封脂注入口及其他辅助密封措施以保证旋转枢轴无泄漏。当旋转枢轴密封失效后,能够带压注脂。密封材料应抗腐蚀、抗老化,具有较长的寿命。供货商应在投标技术文件中提供密封材料的类型和相关性能指标,并加以说明。
9)旋启式全通径止回阀两端与管道干线采用焊接方式连接。
10)供货商应为直径≥20″阀门的两端分别提供一个袖管,长度为500mm ,其它阀门的袖管长度为1倍管径,并在工厂完成焊接和防腐,过渡短节的防腐应和阀体防腐一致,并且应在工厂和阀门一起进行强度和密封水压测试,阀门单独进行水压试验后再焊接过渡短节是不允许的。过渡短节应符合api spec 5l标准。
11)阀门接管材质见数据单。
12)阀门焊接端应做好预处理以满足设计条件和api spec 6d 6.7.2部分描述的接管要求。与管线焊接连接的阀门焊接端应符合asme31.4坡口要求,除非另有规定。对于厚壁阀门应根据asme b16.25加工对焊坡口。
13)阀门的所有部件应针对气候因素进行防护,并在投标技术文件中详细说明采取的防护措施,以保证阀门在安装现场的环境条件下应能够灵活操作。
14)所有的辅助连接件应该与阀门的压力等级相一致。连接件采用适当的支架和支撑安全地固定在阀体上。
15)在阀体上应有用铸造清晰可见的箭头,以表示介质流经阀门的流向。
6.8.7.2 材料
1)材料选择
除非技术规格书和数据单中另有规定外,用于制造阀门的材料均应满足api spec 6d/api594的要求。碳钢均须经过正火或回火处理。
根据操作条件阀门采用铸钢材料。
2)碳当量
焊接连接阀门的端部的化学性能应满足api6d中7.4所进行的要求。其中焊接连接阀门的端部检验分析不应超过下述碳当量极限:
根据公式计算的碳当量应小于0.46。
阀门配带的袖管,其碳当量应和与阀门连接的管材一致或相近。
3)用于密封的软密封材料和密封脂应适合于所输送的流体介质。
4)阀门材料应满足环境温度要求,若采用低温材质,所有辅助材料性能均应能满足使用要求。
5)舌板材质采用316ss不锈钢材料,密封面堆焊slite合金,硬度不低于26hrc,堆焊层厚度不低于1.6mm。阀体内所有的密封圈都应是可更换的。
6)舌板旋臂应采用316ss不锈钢,旋转枢轴材质采用17-4ph不锈钢。
6.8.7.3 检验和测试
1)阀门的检验和测试应严格按api 6d、api 598、ansi b16.34执行。
2)所有铸件都要求进行无损探伤检验。
3)阀门的检验与测试均应根据已由业主批准的检验与测试计划进行。
4)厂方至少应提前25天通知业主阀门的试验日期,如有必要,业主可以到制造厂进行过程监造及出厂前验收。
5)业主有权根据工程的需要,随时对所购产品的全过程进行监造。
6.9 汇管
6.9.1 性能要求
1)在设计温度和设计压力下满足规定的强度要求,使用安全可靠,检查、维修方便。
2)汇管应为直管或筒体上模压拨制开孔的结构型式。
3)汇管的支管内径应与所接管道的内径相同。
4)汇管具备排污排水的功能。
5)供货商应保证汇管同管线具有良好的可焊性。
6)设备外形美观。
6.9.2 强度计算
1)强度计算按gb150的规定执行。
2)腐蚀裕量:2mm。
6.9.3 制造
1)在制造开始前,供货商应向业主提供设计总图,主要受压元件的力学性能、化学成份及供货检验项目,制造工艺,质量保证措施等技术文件,提交份数按合同要求。待设计/业主书面审查同意后,方可开工制造。
2)同一支管的拔制次数不宜超过4次。
3)焊接
除遵照gb150的规定外,尚应满足下列要求:
(1)焊工资格应按tsg r0004-2009执行。
(2)正式焊接前应进行焊接工艺评定,评审至少包括焊态和热处理两种形式,评审合格的焊接工艺方可用于产品制造。
(3)壳体的对接焊接接头应采用gb/t985.1或gb/t985.2中规定的坡口型式。焊接中所选用的焊接方法及坡口形状应能保证焊接接头全焊透,不允许焊缝根部未熔合、未焊透及裂纹等缺陷存在。
(4)所有受压元件的对接焊接坡口必须机加工成型。
(6)焊缝余高应符合gb150.4的规定。
6.9.4 材料要求
1)制造拔制汇管的所有金属材料应满足相应材料标准的要求。
2)受压元件金属材料用钢应是电炉或氧气转炉冶炼的镇静钢。
3)不允许使用低价劣质材料,材料来源应经业主审批。
4)产品用钢制锻件至少应符合nb/t47008、 nb/t47009 ii级锻件及以上的各项检验要求及其它技术要求。
5)当受压元件使用nb/t47008、 nb/t47009、gb713、gb/t9711标准规定以外的材料时,还应符合以下规定:钢材的化学成份(熔炼分析):
c≤0.20%,p≤0.025%,s≤0.015%,
c.e.≤0.43 (c.e.=c mn/6 (cr mo v)/5 (ni cu)/15)
6.9.5 检验和测试
1)a、b类焊接接头应至少进行100%射线检测,符合nb/t47013规定的ⅱ级,技术检测等级为ab级。必要时应进行≥20%超声检测复验,符合nb/t47013规定的ⅰ级,技术检测等级为b级。不能进行射线和超声检测的焊缝,应进行表面检测,采用磁粉、渗透或其它可靠的方法进行,确认无裂纹或其他危害性的缺陷存在。zui终的无损检测要求应满足数据单的要求。
2)所有无损检测应遵循nb/t47013的要求。焊缝质量验收标准按gb 150对a类或b类接头的规定,符合nb/t47013 100%射线检测ii级合格,100%超声检测i级合格,表面检测i级合格。无损检测的操作和分析应由具有资格的技术人员担任。
3)管端坡口应经磁粉、渗透或超声检测,确认无裂纹和分层存在。
4)拔制区域应进行100%超声检测和磁粉检测,符合nb/t47013规定的ⅰ级。
6.9.6 组装
对全部零件检验合格后方能进行组装。
6.9.7 热处理
1)设备应进行整体热处理。
2)设备焊接工作全部结束且经检验合格后,方可进行热处理。
3)热处理后不允许再在设备上施焊。
4)所有焊接试件都应随设备进行热处理并按设计文件要求进行力学性能检验,指标不低于对母材的要求。
5)长度超过16m的拔制汇管允许分段热处理,现场组焊后对焊缝进行局部热处理。
6.9.8 压力试验
耐压试验应采用水压试验,水压试验的方法按gb150.4中11.4.9规定执行。设备壳体的应力值不超过0.9倍的标准屈服强度。
6.9.9 硬度检查
拔制汇管壳体和对接焊接接头的维氏硬度值应满足下列要求:
1)强度级别x80/l555 ≤300 hv10
2)强度级别x70/l485 ≤280 hv10
3)强度级别x65/l450 ≤265 hv10
4)强度级别x60/l415~b/l245 ≤255 hv10
6.9.10外观、尺寸
1)目测外形美观、表面光滑无凹坑。
2)焊接接头应打磨圆滑。
3)尺寸及公差满足规范及施工图要求。
6.10工艺配管
6.10.1 管材及管件
工艺管道的规格、材质及壁厚,供货商应根据本规格书表6.9-1的要求选择,允许供货商根的优化和变更需经业主确认后方可实施。
管件应采用无缝管件,管件标准为 gb/t 12459,管件材质、壁厚应根据规范要求计算选取,端部外径采用ⅰ系列。
表6.9-1 工艺管道材料与制管标准
序号 设计压力(mpa) 公称直径
(mm) 管线规格
(mm) 管型 材料 标准
1 10 dn350 d323.9×13 无缝钢管 l360n gb/t9711-2011 psl2
2 10 dn150 d168.3×7.1 无缝钢管 l245n gb/t9711-2011 psl2
3 6.3 dn200 d219.1×6.3 无缝钢管 l245n gb/t9711-2011 psl2
4 1.6 dn250 d273.1×5.6 无缝钢管 l245n gb/t9711-2011 psl2
5 1.6 dn150 d168.3×5.6 无缝钢管 l245n gb/t9711-2011 psl2
6 10/6.3/1.6 dn100 d114.3×5.6 无缝钢管 l245n gb/t9711-2011 psl2
7 10/6.3/1.6 dn80 d88.9×5.0 无缝钢管 l245n gb/t9711-2011 psl2
8 10/6.3/1.6 dn50 d60.3×5.0 无缝钢管 l245n gb/t9711-2011 psl2
9 10/6.3/1.6 dn40 d60.3×3.6 无缝钢管 l245n gb/t9711-2011 psl2
10 10/6.3/1.6 dn25 d33.7×3.2 无缝钢管 l245n gb/t9711-2011 psl2
6.10.2 安装要求
1)工艺管道连接采用焊接方式,与设备连接采用法兰连接,法兰形式为突面带颈对焊法兰,法兰垫片选用金属缠绕垫片。法兰、紧固件、密封件应符合gb 9112~9131标准要求;
2)管道焊接应按 sy/t 4103 的规定执行, 焊缝间距不小于1倍管道外径且不小于150mm。施工安装其他技术要求应按 gb 50540 的规定执行。工艺管道环焊缝应进行100%手工超声波探伤和100%射线探伤,焊缝质量应分别达到sy/t4109 中的ⅱ级质量标准为合格。
3)调压器、流量计上下游直管段长度应符合设备要求。至少应满足以下条件:
(1)调压器下游直管段长度不应小于5dn;
(2)流量计上、下游应有足够的直管段长度,贸易交接流量计上下游直管段长度应考虑到远期使用的超声波流量计。
4)橇内工艺管路放散应按压力级制不同分别汇至橇外至站场放空系统集中排放;
5)过滤器应设置排污,排污管汇总至橇外站场排污池。还应根据需要考虑设置为排污管路保温的电伴热带。
6.11 仪表
6.11.1 压力(差压)变送器
1)设计与制造
供货商提供的压力(差压)变送器应采用先进的传感器技术和微处理器为基础的智能型压力(差压)变送器,应确保外观、密封性、基本误差、回程误差、静压影响、输出开路影响、输出交流影响、绝缘电阻、绝缘强度满足标准要求;同时可靠性、稳定性、可调量程范围、带负载能力、抗干扰能力、通信能力等方面,具有优良的性能。
应选用智能型变送器,其测量原理宜为电容式或单晶硅谐振式等;其中用于贸易计量的应选用电容式,其它场所使用可选用单晶硅谐振式等。
压力(差压)变送器的测量压力(差压)范围见数据表。
选用灵敏度高的变送器,信号分辨率应大于0.025%,准确度要不低于±0.075%,用于贸易计量补偿运算的变送器精度应提高至±0.04%。变送器准确度要适应流量测量准确度要求。
输出信号为4~20madc(二线制),选择线性,并能输出基于hart通信协议的数字信号;或输出信号为基于现场总线的数字信号。供电电源应为24vdc。
变送器应具有自诊断功能。可用手持编程操作器对其进行零点及量程的调整。
应具有长期的稳定性。在变送器安装后其零点及量程应不受安装位置的影响,不易发生零点漂移且极少需要重新校准。
环境温度变化以及静压力对变送器的测量准确度影响应尽量小。通常压力(差压)变送器采用露天安装方式、保温箱内安装或室内安装,环境温度对其的影响不可小视,尤其是用于计量系统的压力(差压)变送器。压力(差压)变送器应具有良好的温度特性,其零点和量程在环境温度发生变化时所受的影响,环境温度每变化50°f(28℃)的影响应优于:±(0.025%量程上限 0.125%量程)。静压每变化1000psi(6.9mpa)的影响应优于:±0.1%量程上限。供货商在投标时应提供温度特性、静压特性曲线和报告。
变送器应适合在环境温度-40℃~75℃下正常工作。当环境温度高于-20℃时,根据需要可选用就地显示功能,即采用lcd液晶显示器。当环境温度低于-20℃时,应采取保温措施。
变送器应具有承受zui大量程的1.5倍的过载能力。
变送器测量室中的灌充液应能适应现场环境温度的要求。灌充液应采用对温度不敏感的硅油介质作为灌充液。
变送器应具有防止瞬变电压的保护功能,如需要防雷端子,应优先采用内置式防雷端子。
变送器应能在危险区域内安装并正常使用,其防爆等级不应低于exdiict4或exiaiict4,防护等级不应低于ip65。
与介质接触的部分应选用316不锈钢材质。
变送器需要支架安装时,应提供适于安装在2"钢管上的不锈钢支架及紧固件。
变送器电气接口应为1/2"npt(f)、g3/4〞(f)或m20×1.5(f),并应配带进线口的金属密封堵头一个。
供货商应根据需要配套提供压力(差压)变送器的一体化阀组。差压变送器的一体化阀组的高低压连通阀应为2个串联的截止阀,以防泄漏。一体化阀组材质应为不锈钢,过程连接螺纹应为1/2"npt(f)。
2)材料
供货商应对压力(差压)变送器工作在zui高设计压力条件下所采用的材料耐压等级是否能满足要求进行核算并提供充分的书面依据。如果不能满足,应提高变送器的耐压等级或采用适当的材料。
压力(差压)变送器与天然气接触的所有部件的材质应使用适用于天然气的材料制造,它们既不能影响天然气的性质,又不能受天然气的影响。
压力(差压)变送器内部的所有与天然气介质接触表面应用抗腐蚀材料制造,尤其选用能够抗硫化氢腐蚀的防腐材料。
压力(差压)变送器外部应选用适应环境条件的抗腐蚀涂层进行保护。
3)检验和测试
(1)工厂验收试验
所有压力(差压)变送器在出厂前应根据有关规范进行工厂试验,以证明所提供的设备在各方面均能完全符合买方的要求。
压力(差压)变送器应依据相应的工业标准、计量检定规程或其它的管理规范进行测试,所依据的检定规程、标准等应征得买方同意。
供货商应向买方提供每台压力(差压)变送器的出厂测试报告、计量检定证书及质量检验报告,应是具有签署和日期的正式报告。
供方必须对所供设备进行100%的试验和检验,其内容至少应包括:
① 静态测试
数量检查(包括附件);
外观检验(包括漆面质量、表面光洁度等检验);
尺寸检测;
接线端子板应有接线标志;
电源及接线是否满足要求;
标牌标识是否完整、清晰;
防爆等级或本质安全设备的认证证书;
紧固件等是否有松动现象;
连接件形式、尺寸是否符合标准;
是否遵从焊接规范和标准;
材质是否与供货商提供的证明相符(内部件,外壳、连接件等)。
② 动态测试
基本误差;;
密封性;
回程误差;
输出开路影响;
输出交流影响;
绝缘电阻测试;
绝缘强度测试;
电磁干扰试验;
压力测试(包括附带的外保护套管);
带负载能力(20~30vdc)试验;
振动试验;
高、低温和湿度环境试验;
仪表测量准确度受环境温度变化及介质温度变化影响试验;
仪表功能测试;
其它内容测试。
(2) 现场验收试验
仪表设备运抵安装现场后,由供方与买方共同开箱检查,发现问题,由供方负责解决(即使在供货商工厂已试验过且已通过出厂验收)。
在现场验收试验前两星期,供方应事先提出试验计划,并须征得业主的批准。现场试验合格后,由用户预验收。
(3)压力(差压)变送器检定
压力(差压)变送器在安装前应在国内,由授权的法定计量检定部门进行检定,检定不合格者由供方负全部责任。供货商应提供法定计量检定部门出具的检定证书。
4)供货范围及界面
供货商应提供压力(差压)变送器及配套附件。
6.11.2 一体化热电阻温度变送器
1)设计与制造
供货商提供的一体化温度变送器应采用微处理机为基础的智能型温度变送器,应确保外观、基本误差、回程误差、负载变化影响、电源变化影响、输出交流分量、绝缘电阻、绝缘强度满足标准要求;同时可靠性、稳定性(稳定性达到3年内不大于±0.5℃,在变送模块安装后其零点及量程应不受安装位置的影响)、可调量程范围、带负载能力、抗干扰能力、通信能力等方面,具有优良的性能。
供货商提供的一体化温度变送器主要包括变送器、温度传感器(铂电阻pt100 α=0.00385 )、传感器保护套管等,供货商提供的温度变送器应为一体化温度组件,包括变送器、传感器、传感器保护套管组合在一起进行成套供货。
(1)变送器的技术特性应能满足以下要求:
应选用智能型温度变送器,其测量准确度:用于贸易计量补偿运算的变送器要优于±0.2﹪,信号分辨率应大于0.025%,变送器准确度要适应流量测量准确度要求;其它场所使用的变送器要优于±0.5﹪。
输出信号为4~20madc(二线制),并能输出基于hart通信协议的数字信号;或输出信号为基于现场总线的数字信号。供电电源应为24vdc。
变送器应具有自诊断功能;可用手持编程操作器对其进行零点及量程的调整。
应具有长期的稳定性,在变送器安装后其零点及量程应不受安装位置的影响,不易发生零点漂移且极少需要重新校准。
用于计量系统的温度变送器应具有输入rtd校准常数,产生一条与传感器曲线相匹配的定制曲线,提高传感器的精度。
变送器应能接收3线制或4线制rtd输入信号。
环境温度变化对变送器的测量准确度影响应尽量小。通常温度变送器采用露天安装方式,环境温度对其的影响不可小视,尤其是用于计量系统的温度变送器。温度变送器应具有良好的温度特性,其零点和量程在环境温度发生变化时所受的影响,在zui大量程的条件下环境温度影响应小于:0.0015℃/1.0℃。供货商在投标时应提供温度特性曲线和报告。
变送器应适合在环境温度-40℃~70℃下正常工作。当环境温度高于-20℃时,根据需要可选用就地显示功能,即采用lcd液晶显示器。当环境温度低于-20℃时(尽量不选用就地显示的lcd液晶显示器),应采取保温措施。
应具有防止瞬变电压的保护功能,如需要防雷端子,应优先采用内置式防雷端子。
变送器应能在危险区域内安装并正常使用,其防爆等级不应低于exdiict6,防护等级不应低于ip65。
变送器电气接口应为1/2npt(f)或g3/4〞(f),变送器应配带进线口的金属密封堵头一个。
变送器与传感器的连接采用1/2npt(f)或m20×1.5螺纹连接。
特殊情况下,变送器与温度传感器也可分开安装。
(2)传感器
传感器的检测元件应选用铂热电阻(rtd),测量温度应能达到-200~650℃。rtd元件应选用在0℃时,电阻值为100ω,α=0.00385 的铂热电阻。rtd元件的特性应符合iec 60751 class a标准,校验应符合iec 60751标准。
rtd的输出通常贸易计量选用4线制,其它场所可选用3线制。
铂热电阻的常温绝缘电阻值不应小于100mω。
传感器的探头直径一般为φ6mm的不锈钢套管,其弹顶式结构传感器采用1/2npt(m)螺纹与变送器的连接。
温度传感器保护套管的长度应根据相应的数据表中提供的传感器安装位置处的管径和外保护套管长度来确定。
通常,在测量管线中,温度变送器应垂直向上安装,并且要求供货商在出厂前将lcd就地指示表头(液晶显示器)和铭牌(商标)按垂直安装方式调好。当测量管路为dn80以下时,尽量采用45度、迎流安装方式。
(3)随温度变送器应提供下述附件:
应提供用于温度传感器与变送器连接的可调整的过渡组件,该组件与温度传感器、变送器的连接采用螺纹连接,材质应为不锈钢。
应提供与传感器配套的外保护套管(管嘴一体化),根据管道的设计压力,外保护套管可以直接焊接在管道上,其材质应与安装位置的管道材质一致;也可选择螺纹连接,这时传感器安装处管道应焊接凸台。外保护套管的压力等级应为管道的设计压力。
如测量管路需要保温时,管嘴长度应为120mm(保温层厚度约为50mm)。
传感器探头与外保护套管采用螺纹连接方式,外保护套管的长度应根据温度传感器探头的长度进行配套。
2)材料
供货商应对温度传感器工作在zui高设计压力条件下所采用的材料耐压等级是否能满足要求进行核算并提供充分的书面依据。如果不能满足,应提高温度传感器的耐压等级或采用适当的材料。
温度传感器与介质接触的所有部件的材质应适用于油品、天然气的材料制造,它们既不能影响油品、天然气的性质,又不能受油品、天然气的影响。
温度传感器内部的所有与油品、天然气介质接触表面应用抗腐蚀材料制造,尤其选用能够抗硫化氢腐蚀的防腐材料。
温度变送器外部应选用适应环境条件的抗腐蚀涂层进行保护。
供货商应提供主要零部件材料化学成分、机械性能、无损检测报告。
3)检验和测试
(1)工厂验收试验
所有温度变送器在出厂前应根据有关规范进行工厂试验,以证明所提供的设备在各方面均能完全符合买方的要求。
温度变送器应依据相应的工业标准、计量检定规程或其它的管理规范进行测试。
供货商应向买方提供每台温度变送器的出厂测试报告及质量检验报告,应是具有签署和日期的正式报告。
供方必须对所供设备进行100%的试验和检验,其内容至少应包括:
①静态测试
数量检查(包括附件);
外观检验(包括漆面质量、表面光洁度等检验);
尺寸检测;
标牌标识是否完整、清晰;
防爆等级或本质安全设备的认证证书;
紧固件等是否有松动现象;
连接件形式、尺寸是否符合标准;
是否遵从焊接规范和标准;
材质是否与供货商提供的证明相符(内部件,外壳、连接件等)。
② 动态测试
密封性;
基本误差;
回程误差;
静压影响
绝缘性能试验;
输出开路影响;
输出交流影响;
绝缘电阻测试;
电磁干扰试验;
带负载能力(20~30vdc)试验;
振动试验;
高、低温和湿度环境试验;
仪表测量准确度受环境温度变化及介质温度变化影响试验;
仪表功能测试;
其它内容测试。
③现场验收试验
仪表设备运抵安装现场后,由供方与买方共同开箱检查,发现问题,由供方负责解决(即使在供货商工厂已试验过且已通过出厂验收)。
在现场验收试验前两星期,供方应事先提出试验计划,并须征得业主的批准。现场试验合格后,由用户预验收。
④温度变送器检定
温度变送器在安装前应在国内,由授权的法定计量检定部门进行检定,检定不合格者由供方负全部责任。供货商应提供法定计量检定部门出具的检定证书。
4)备品、备件及工具
供货商应提出两年内运行所需的备品备件、易损件以及仪表、自控设备维护与调校的工具的建议,并提供单项报价清单,以帮助业主进行选购。
5)供货范围及界面
供货商应提供一体化温度变送器及配套安装附件。
6.11.3 压力表
1)设计与制造
供货商提供的压力表及其相关的附件应适合天然气流量的连续测量,适应被测天然气组分、流量、压力、温度的变化,满足现场安装、使用环境的需求。
应选用测量元件为弹簧管式的压力表。
压力表的准确度等级为1.0或1.6级,表盘刻度的单位应为mpa或kpa。
压力表的零部件装配应牢固、无松动现象;涂层应均匀光洁、无明显剥脱现象。
压力表应配有高强度、安全模式的玻璃,背部应有防止压力过大的安全膜片,以适应现场安装环境及运输条件。
压力表刻度盘应为机械指针式,宜选用不锈钢材质,刻度盘的底色应为白色,色标应符合测量介质为可燃性油品和气体的规定,刻度分度值应符合国家标准的要求。
压力表应有可直接读取的明显的指示盘,盘面直径为ø150mm。
压力表应能长期承受一个与zui大刻度值相等的压力,且应能短期承受一个超过zui大刻度值1.25倍的过压力。
压力表的过程连接部分应采用1/2npt(m)或m20×1.5。
压力表的测量元件和外壳均应选用不锈钢材质。
压力表和附件的材料选择应考虑在zui低环境温度条件下运行,还应考虑介质温度和介质组分的影响。
压力表处于爆炸危险场所区域内,其防护等级不应低于ip65。
封印:为保证测量准确性,提高测量数据的可信度,对于可能影响测量准确度的地方,必须提供可加封印的机构。
2)材料
供货商应对压力表工作在zui高设计压力条件下所采用的材料耐压等级是否能满足要求进行核算并提供充分的书面依据。如果不能满足,应提高压力表的耐压等级或采用适当的材料。
压力表与天然气接触的所有部件的材质应适用于天然气的材料制造,它们既不能影响天然气的性质,又不能受天然气的影响。
压力表内部的所有与天然气介质接触表面应用抗腐蚀材料制造,尤其选用能够抗硫化氢腐蚀的防腐材料。
压力表外部应选用适应环境条件的抗腐蚀涂层进行保护。
供货商应提供主要零部件材料化学成分、机械性能、无损检测报告。
3)检验和测试
(1)工厂验收试验
所有压力表在出厂前应根据有关规范进行工厂试验,以证明所提供的设备在各方面均能完全符合买方的要求。
压力表应依据相应的工业标准或其它的管理规范进行测试,所依据的检定规程、标准应征得买方的同意。
供货商应向买方提供每台压力表的出厂测试报告及质量检验报告,应是具有签署和日期的正式报告。
供方必须对所供压力表进行100%的试验和检验,其内容至少应包括:
①静态测试
数量检查(包括附件);
压力表涂层应均匀光洁、无明显剥脱现象;
压力表应装有安全孔,安全孔上须有防尘装置;
压力表按其所测介质不同,应有规定的色标;
压力表表盘玻璃应无色透明,不应有妨碍读数的缺陷和损伤;
分度盘应平整光洁,各标志应清晰可辨;
指针指示端应能覆盖zui短分度线长度的1/4~3/4;
指针指示端的宽度应不大于分度线的宽度;
测量上限值数字和分度值应符合规定;
尺寸检测;
标牌标识是否完整、清晰;
防爆等级或本质安全设备的认证证书;
压力表的零部件装配应牢固、无松动现象;
连接件形式、尺寸是否符合标准;
是否遵从焊接规范和标准;
材质是否与供货商提供的证明相符(内部件,外壳、连接件等)。
②动态测试
准确度;
零位;
示值误差;
回程误差;
重复性;
轻敲位移;
指针偏转平稳性;
仪表功能测试;
其它内容测试。
③现场验收试验
压力表运抵安装现场后,由供方与买方共同开箱检查,发现问题,由供方负责解决(即使在供货商工厂已试验过且已通过出厂验收)。
在现场验收试验前两星期,供方应事先提出试验计划,并须征得业主的批准。现场试验合格后,由用户预验收。
④压力表检定
压力表在安装前应在国内,由授权的法定计量检定部门进行检定,检定不合格者由供方负全部责任。供货商应提供法定计量检定部门出具的检定证书。
4)备品、备件及工具
供货商应提出两年内运行所需的备品备件、易损件以及仪表、自控设备维护与调校的工具的建议,并提供单项报价清单,以帮助业主进行选购。
5)供货范围及界面
供货商应提供压力表、垫片等。
6.11.4 双金属温度计
1)设计与制造
应选用径向型或万向型,表盘选用ø100mm的双金属温度计,其外壳应采用不锈钢材质。
双金属温度计的准确度等级不低于1.5级,仪表盘单位为摄氏度。
双金属温度计指示盘的玻璃应为高强度、安全模式玻璃,以适应现场安装环境及运输条件。
仪表的刻度盘应为机械指针式,应选用铜铝合金材质,底色为白色,上面标的数字和刻度为黑色(不易褪色),刻度分配应采用厂家提供的标准。
双金属温度计的传感器保护套管一般为φ10 mm的不锈钢套管,与外保护套管采用螺纹连接。双金属温度计传感器保护套管的长度应根据相应的数据表中提供的安装位置处的管径确定。
供货商应提供与双金属温度计配套的外保护套管(管嘴一体化),为了便于测量管道保温(保温层厚度约为50mm),其中管嘴外露长度斜装90mm、直装80mm。外保护套管可以直接焊接在管道上,其材质应与安装位置的管道材质一致。外保护套管的压力等级应为管道的设计压力。
通常,在天然气测量管线中,双金属温度计应垂直向上安装,当测量管路为dn80以下时,尽量采用45度、迎流安装方式。
双金属温度计的测量范围、安装地点、插入长度、仪表位号、数量等应参照相应的双金属温度计数据表。
2)材料
供货商应对双金属温度计工作在zui高设计压力条件下所采用的材料耐压等级是否能满足要求进行核算并提供充分的书面依据。如果不能满足,应提高双金属温度计的耐压等级或采用适当的材料。
双金属温度计与介质接触的所有部件的材质应适用于天然气的材料制造,它们既不能影响天然气的性质,又不能受天然气的影响。
双金属温度计内部的所有与天然气介质接触表面应用抗腐蚀材料制造,尤其选用能够抗硫化氢腐蚀的防腐材料。
双金属温度计外部应选用适应环境条件的抗腐蚀涂层进行保护。
供货商应提供主要零部件材料化学成分、机械性能、无损检测报告。
3)检验和测试
(1)工厂验收试验
所有仪表在出厂前应根据有关规范进行工厂试验,以证明所提供的设备在各方面均能完全符合买方的要求。
双金属温度计应依据相应的工业标准或其它的管理规范进行测试。
供货商应向买方提供每台仪表的出厂测试报告及质量检验报告,应是具有签署和日期的正式报告。
供方必须对所供设备进行100%的试验和检验,其内容至少应包括:
① 静态测试
数量检查(包括附件);
双金属温度计涂层应均匀光洁、无明显剥脱现象;
分度盘上应有如下标志:包括制造单位或商标、产品名称、计量单位和数字、计量器具制造许可证和编号、准确度等级、出厂编号。
分度盘应平整光洁,各标志应清晰可辨;
防爆等级或本质安全设备的认证证书;
双金属温度计的零部件装配应牢固、无松动现象;
双金属温度计表盘玻璃应无色透明,不应有妨碍读数的缺陷和损伤;
指针指示端应能覆盖zui短分度线长度的1/4~3/4;
指针指示端的宽度应不大于分度线的宽度;
测量上限值数字和分度值应符合规定。
连接件形式、尺寸是否符合标准;
是否遵从焊接规范和标准;
材质是否与供货商提供的证明相符(内部件,外壳、连接件等)。
②动态测试
零位;
示值误差;
回程误差;
重复性;
角度调整误差;
温度响应时间;
指针偏转平稳性;
静压测试(包括附带的外保护套管);
绝缘性能试验;
仪表功能测试;
其它内容测试。
③现场验收试验
仪表设备运抵安装现场后,由供方与买方共同开箱检查,发现问题,由供方负责解决(即使在供货商工厂已试验过且已通过出厂验收)。
在现场验收试验前两星期,供方应事先提出试验计划,并须征得业主的批准。现场试验合格后,由用户预验收。
④双金属温度计检定
双金属温度计在安装前应在国内,由授权的法定计量检定部门进行检定,检定不合格者由供方负全部责任。供货商应提供法定计量检定部门出具的检定证书。
4)供货范围及界面
供货商应提供双金属温度计及配套附件。
6.11.5 电动执行机构
1) 设计与制造
(1)总则
电动执行机构为多回转或部分回转(90°旋转)控制的驱动设备。本工程选用智能型电动执行机构。供货商应该对电动执行机构的正确运行和型号的正确选择负责。对于任一给定阀门的电动执行机构的行程/扭矩选型取决于:
——阀门尺寸
——阀门类型(等级系列)
——管线压力
——阀门两端zui大压差
——操作温度
——管线内流体类型
——环境温度
——阀杆尺寸等
——阀门的全行程圈数(对于多回转阀门)
——阀杆承受的zui大力矩
选型所需的扭矩应从阀门供货商获得。决定电动执行机构选型的其他因素有操作速度(阀门开关时间)等。阀门和联轴器应该能够承受电动执行机构产生的zui大扭矩。
电动执行机构的选型应能满足数据单中规定的zui恶劣操作条件下的阀门运行要求,并且电动执行机构的额定输出扭矩应具有不小于1.25倍阀门公称扭矩的安全系数。
电动执行机构操作速度必须按照数据单中指明的速度以及阀门的结构特性来选择。开关时间见数据单。
电动执行机构输出的zui大扭矩不应对阀门造成破坏,输出的zui小扭矩能保证阀门的正常开启。执行机构输出扭矩在现场可调。
电动执行机构应为非侵入式智能型,对执行机构进行任何外部调节、调试、故障诊断及设定值的修改均可通过外部操作进行,不需要拆开执行机构的密封端盖。
电动执行机构的阀位指示应为连续指示,递增量为1%。执行机构在外部电源断电时仍然可以就地显示阀位及相关报警,并可实时反映因就地手轮操作而使阀位发生的变化。
智能型电动执行机构具有每次通电后的自动巡检功能,以使设备正常工作。同时智能型执行机构具有数据及事件记录功能,所记录各种参数及事件均可安全下载。
电动执行机构应能通过lcd面板上显示与阀门、控制回路、执行机构本身的故障及报警。
供货商确保所提供的电动执行机构的正常使用寿命不低于30年。
电动执行机构的防爆/防护等级不低于ex d ii bt4/ip68。
阀门所配执行机构或控制系统的故障不应影响到阀门的其他部分,并且其维修和更换工作应能够在不影响阀门正常工作的情况下进行。
使用寿命开关全周期≥8000次。
(2)机械特性
执行机构应包括电机、齿轮减速器、联轴器、限位开关、扭矩限制开关、手轮、手轮自动断开装置、就地阀位显示以及安全平稳运行所需的其它部件。执行机构整体组装应该是密闭的,独立的且适合于户外操作。
齿轮如需润滑,则润滑系统在使用期内应免维护。
在操作过程中以及在开启点,所需手轮zui大操作力不应超过250n,以保证一个操作工无需加力工具可以操作。
在就地手动操作过程中,电机通过手动、电动切换装置的离合器断开。
顺时针操作手轮将关闭阀门。
涡轮蜗杆的机械啮合效率≥35%。
(3)电动特性
电机应是鼠笼式感应电机,现场供电条件:380vac、50hz。电力供应的电压波动为±10%,频率为±10%,且短期电压下降可达15%。
正常带动阀门时,在100%额定电压情况下电机任何部分的温升都不超过允许范围。
电机应该是整体封闭的,采用自然冷却。电机具有不低于“f”级的绝缘,能满足沿线站场所在位置的气候条件。
电动执行机构应为开关型。
电机应有过热保护装置。当阀门在局部卡死的情况下仍能开启阀门,电机的短时间堵转(失速)力矩应能达到额定力矩的2倍。
阀位信号输出应是无源触点(spdt),接点容量不应小于1a 24vdc。
电动执行机构应具有限位保护、过力矩保护、正反向联锁保护,电机过载、过热保护,防冷凝的加热保护和控制回路过载及短路保护,相位自动校正能力。
与外部连接的接线端子板应置于一个单独的密封的接线腔体内。使现场连接电缆时内部控制电路免于直接暴露于外部环境。端口应该有标号,接线也要清晰地标记。
接线箱应设有至少2个电缆连接的入口,未用的接线口要用金属丝堵封闭。电缆入口和连接件都应符合防爆要求。接管螺纹满足npt标准,其尺寸不应小于1 inch。
电动执行机构可对执行机构本身故障和外部控制回路故障进行检测和报警。
接线箱内外都应有接地端子。
执行器内应防止生成冷凝物。电气部分的外壳的防爆等级应不低于eexd iibt4,并具有授权实验室的认证。
执行器内应为一体化产品,电机启动器与所有电缆应在执行器内部。
执行机构突然掉电时,阀门的状态信号能够上传站控系统。
(4)控制系统
电动执行机构包括电机启动器、就地控制和远程控制, 远程控制可以实现远程开关操作和阀位显示。
电动执行机构应具有就地和远方开/关/停止的控制能力。
电动执行机构应有带锁的 就地/停止/远控 选择开关。选择开关在就地位时,执行机构由就地的开关(按钮)控制。选择开关在远控位时,执行机构由远程开关或控制系统控制。选择开关在停止位时,执行机构只能通过手轮操作。阀门所配的电动执行机构的就地开关操作为自保持型,远控开关操作可设置为非自保持型/自保持型。
电动执行机构内部控制器的精度应≤1%,在相同方向要使电动执行机构动作需要的zui大信号变化量为1%。电动执行机构和阀门配套后的整体精度应保证≤1.5%。
远方控制继电器和指示信号输出接点的电压等级为24vdc。输出接点应是无源接点。控制继电器由站控系统的控制输出控制。
执行机构应具备故障自诊断和报警功能。电动执行机构本身应有状态指示和开度指示,能向远方发送开/关/停状态指示的触点信号及故障报警等触点信号。lcd应能适应现场环境的温度要求,执行机构lcd就地指示在阀门任何安装位置均可正视操作者。
执行机构应包括足够的可组态的继电器用以实现以下远程显示:
——阀全开到位
——阀全关到位
——阀门正在开
——阀门正在关
——报警(综合报警)
——过扭矩报警
——就地和远控操作。
执行机构应具有输出扭矩在线实时显示功能。
启用esd命令时,应不受就地/远控开关的限制。
2)材料
执行机构的润滑油应能在现场条件下正常工作,报价书中应提供液压油的品牌及性质,便于用户日后采购。
主要承压零部件和标准件应提供材料化学成分和机械性能检测报告。
所选材料应能适应环境温度及操作条件。
不排除供货商使用性能优于上述条款中所规定的材料。
3)检验和测试
(1)总则
本检验和测试不能解除供货商对所提供设备的材质、工艺和性能所负的责任。以下的检验和测试由供货商自费进行。
如果需要,业主有权监视检验和测试的进行。
检验和测试的目的是检查执行机构、阀门和执行机构的组装的有效性和功能,它们都应该符合本技术规格书的要求。
为此,执行机构应与本工程中使用的阀门组装后进行检验和测试。执行机构输出扭矩应与阀门的扭矩相匹配。
(2)执行机构的测试
下面描述了电动执行机构检验和测试的程序,但不如此。供货商应根据实际工艺和控制要求主动检验和测试电动执行机构。扭矩保护系统:
当扭矩保护系统调试好后,执行机构应该在无载荷的情况下,逆时针和顺时针两个方向各运行几分钟, 然后再加载运行直至确认扭矩保护已起作用。
①功能测试
控制回路的正确运行:控制回路的各个元件正确运行的测试:限位开关、选择器、监控继电器,自动相位保护。
转速:在执行机构没有载荷的情况下,确认电机在1分钟的总转数与手轮的转数比率,从而验证阀门开关的速度。
zui小扭矩的设定:为执行机构提供额定的电压,把执行机构扭矩开关调到zui小值并与远控回路连接,逐渐增加荷载然后在正反两个方向测量扭矩。阀门需要的电流要记录在检测证书上, 以确认zui小扭矩的设定值。
zui大扭矩的设定:为执行机构提供额定电压,并且把执行机构与远控回路连接,逐渐增加载荷,然后在正反两个方向测量扭矩。从无载荷开始直到扭矩保护系统停止动作,载荷增加至少分5个阶段。将阀门所需要的电流记录在检测证书上,以确认zui大扭矩的设定值。
就地控制的校验:在有载荷的条件下,进行就地控制连接的测试(执行机构不能倒转);将执行机构设定在阀门zui大扭矩的70%和80%,测试开关两方向上执行机构的过扭矩自动停止功能;在执行机构无载荷和执行机构动作的状态下,进行就地控制的连接和断开的测试;在执行机构动作状态下,在开关两个方向连续两次连接就地控制,进行测试;在检测就地控制的连接与断开时,不应引起手轮的非正常动作。
②设定值的校准
各种限位开关应调到设定值的正确位置进行校准。
③外观检测
执行机构应该进行外观检测,以确保执行机构表面没有在制造和组装过程中因误操作所导致的划痕或损坏。
除此之外,还包括以下几项的检测:
——外观检测润滑油系统的严密性,以确保润滑油系统无内外泄漏。
——确保zui后要安装的连接系统已正确替换了用于检测的系统
——检查阀杆外盖或旋塞是否正确地安装好
——检查螺钉是否完全拧紧
——检查电缆密封套或插塞是否已经安装在电缆进口上
(3)执行机构和阀门组装后的整体测试
除了提前用特殊文件规定外,组装好的阀门和执行机构厂应在阀门生产车间进行检测,检测内容如下:
①在执行机构关闭阀门的状态下,阀门的严密性检测
② 无载荷和有载荷条件下的操作试验,包括扭矩和限位开关操作试验
③检查阀门在关闭状态下阀杆轴线是否垂直于管线的轴线。
(4)现场测试
① 现场测试是指阀门与执行机构在现场安装前进行的测试,其目的在于确保阀门与执行机构安装后在操作条件下能正常工作。
②供货商需派有经验的人员到现场协助阀门与阀门执行机构现场测试工作。
③ 在保修期内如果测试和运行过程中出现任何产品故障或缺陷,供货商都要免费进行维修或更换,直到满足功能要求为止。
④作为一项zui低要求,如果现场可以满足条件,则应在现场重复工厂实验以通过现场验收测试。供货商应在收到定单2周后向业主报批现场验收测试计划。
4)铭牌
(1) 制造商应提供铭牌以正确标识每个执行机构,并与供货文件相一致。铭牌上应至少给出下列信息:
——执行机构位置编号;
——执行机构型号
——供货商名
——电机的特性参数
——执行机构的特性参数
——电气执行标准/保护标准
——总传动比
——zui大额定输出扭矩
(2)铭牌应由不锈钢制成且成矩形。
(3) 铭牌尺寸可按照供货商标准确定,但铭牌上的文字应在安装后清晰可见。
(4)铭牌使用不锈钢自攻螺钉固定在执行机构上。
(5) 铭牌上的文字应在现场条件下长期保持清晰可读。
(6)铭牌上的文字为中文或英文,单位为si制。
5)供货范围及界面
供货商应提供电动执行机构及其他配套设备,与阀门配套的连接件,辅件和连接头。
6.11.6 气动执行机构
1)技术要求
(1)供货商应该对气动执行机构的正确运行和型号的正确选择负责。对于任一给定阀门的气动执行机构的冲程/扭矩选型取决于:
a) 阀门尺寸;
b) 阀门类型(等级系列);
c) 管线压力;
d) 阀门两端zui大压差;
e) 操作温度;
f) 管线内流体类型;
g) 环境温度;
h) 阀杆密封结构等;
i) 操作速度(阀门开关时间),控制方式等;
j) 气源压力。
阀杆行程和推力或所需要的扭矩应从阀门制造商获得。
(2) 气动执行机构应按照工艺专业阀门数据单中规定的zui恶劣操作条件(本工程的所处地区的zui高和zui低的环境温度,所处的地区环境,工艺zui高压力、zui低压力工况及流量,zui大压差等情况)下进行选择,并且要求有一定的安全余量。气动执行机构的扭矩或推力应具有1.5倍的安全系数,同时气动执行机构的zui大扭矩或推力应不大于阀门和联轴器能够承受的zui大扭矩或推力。执行机构整体组装应该是密封的,适合于户外操作。在所规定操作使用时,寿命不少于25年。
(3) 在全压差的条件下,口径为dn50及以下的阀门,其全行程关闭/打开时间宜在2秒以内;dn50~dn500的阀门,其全行程关闭/打开时间应根据工艺过程以及安全生产要求提出,全行程关闭/打开时间宜在25秒以内,这一时间值应在所给定范围内能进行调整。供货商应根据本工程工艺要求提出合理的关闭/打开时间。
(4)若气动执行机构要求故障时阀门处于安全位置,执行机构可以采用单气缸弹簧复位式,也可为双气缸带事故储气罐式,通常口径为dn250及以下的阀门选用单气缸弹簧复位式执行机构,口径为dn250以上的阀门选用双气缸带事故储气罐式执行机构。采用事故储气罐时,储罐应带有单向阀,其储罐的容积应满足阀门从全开到全关和从全关到全开动作各1次,即满足1次全行程的的储气容量。
(5)气缸为低压型,其压力≤1.0mpa。气动执行机构可使用管道中的天然气作为动力气源,也可根据情况采用仪表风作为动力气源。管道中天然气压力范围为1.6~10mpa,仪表风压力范围为0.4~0.8mpa。当采用管道天然气作为动力源时,配套提供相应的过滤组件、减压系统、压力表等。配套的动力气源调压器应能适应管输压力的变化,并应配套过滤性能好,便于更换和维修的过滤组件以及防止气体节流后造成冰堵的设备。同时调压系统应设置相应的安全泄放阀和安全截断阀等可靠的气源压力安全装置,以防止动力气源调压器出现故障时,高压管道气进入到气动执行机构低压系统,发生安全事故。
(6) 用于紧急关断和紧急放空气动执行构的电磁阀只能人工现场手动复位,不允许自动打开。
(7)当采用管道天然气作为动力源时,供货商应配套提供安装于动力气取气管道上的截断球阀。截断球阀带操作手柄,尺寸为dn15,压力等级应为pn16mpa。在正常工作状态下,执行机构(包括气动管路、附件等)应无泄漏。动力气取压采用螺纹管嘴、焊接法兰连接件或者焊接法兰阀,根据工程需要确定是否由供货商一并提供。
(8) 执行机构应配带电磁阀、阀位开关、气动三联件等。电磁阀采用长期带电型低功耗防爆型(材质316sst),功耗不大于4w,电磁阀供电电源为24vdc。紧急关断和紧急放空气动执行构的电磁阀按励磁设计(正常时电磁阀带电,执行机构不动作)。其提供的阀位信号为无源接点信号,接点容量:24v.dc 2a。
气动执行机构的限位开关提供独立的隔爆型接线盒,防爆标志的zui低要求为iec exdⅱbt4,与用户连接的电气接口为3/4〞npt(f),阀位开关与接线盒的电缆连接由供货商配套完成,并保证达到防爆要求。电磁阀电气接口为1/2〞npt(f)。
电磁阀和阀位开关防爆型式应采用“隔爆”型或“本安”型,防爆标志的zui低要求为iec exdⅱbt4或exiaⅱbt4。若采用本安型设备时,供货商应提供配套的隔离式安全栅。
(9)气动执行机构的防爆接线箱应设置可靠的接地连接端子。
(10)气动执行机构为露天使用安装,防护等级为ip65。如果采用管道天然气作动力,所有气动组件可集成在带有防护的箱内,防护箱内应设置防冻凝电加热器。
(11) 总成后的阀门执行机构信号指示应包括:
①远传信号:
a)阀门开、关控制信号;
b)阀门开到位、关到位状态返回信号。
②就地指示:
a)阀门开关的就地阀位指示。
(12)气动执行机构应在便于操作的位置带有就地开、关阀门的手轮、拉杆或按钮,并应提供可靠的锁定装置,手轮宜侧装。手操机构的力不大于250n。
(13)当采用天然气气源,气缸排气孔处带护网和具有适当长度且朝向上的排气导向管,护网和和导向管的材质为不锈钢。所有放空口或呼吸通气口应朝下,并应加网罩,防止外界异物及水进入。
(14) 执行机构应具备上下限位调节设定功能,目的是补偿阀门和执行机构的制造公差,和长时间使用阀门特性的改变。
(15) 执行机构的定位精度应高于2%,重复精度和迟缓率不大于全行程的1%,死区应是可以调整。
(16)执行机构涂底漆前应表面处理洁净,去油污,干燥后涂底漆一道,需涂三层抗腐蚀面漆。
(17 )气动执行机构的安装地点、数量等应参照相应的工艺专业数据表。
(18 )气动执行机构有安全完整性等级要求时,其安全完整性等级应不低于sil2。
2)材料要求
(1) 供货商应保证所提供的气动执行机构所配套的承压部件、组件、容器、气缸等在材料的使用方面无任何设计问题,能够满足实际操作和使用过程中的要求,如气质、压力、温度、粘度、组份等的要求。应保证所有零部件的材质必须符合环境条件如湿度、温度以及防爆的要求。应按astm相关标准选材,并按astmⅲ标准锅炉和压力容器的要求进行制作和鉴定。
(2 ) 当提供与管道焊接的螺纹管嘴、焊接法兰连接件或者焊接法兰阀时,其螺纹管嘴、焊接法兰连接件或者焊接法兰阀与管道具有良好可焊性。
(3 ) 管道取压阀和取压配管的材质应为316sst。
(4) 电磁阀材质应为316sst。
3)检验和测试
(1)气动执行机构在出厂前应根据有关规范进行工厂试验及与阀门组装后的整体性能测试,以证明所提供的单项设备及整套装置在各方面均能完全符合业主的要求。
(2)气动执行机构应依据相应的工业标准或其它的管理规范进行出厂测试。
(3)供货商应向业主提供每台气动执行机构的出厂测试报告及质量检验报告,应是具有签署和日期的正式报告。
(4)供货商必须对所供设备进行100%的试验和检验并提供相应报告,其内容至少应包括:
①检验
a) 数量检查(包括附件);
b) 外观检验(包括漆面质量、表面光洁度等检验);
c) 尺寸检测;
d) 标牌标识是否完整、清晰;
e) 防爆标志或本质安全设备的认证证书;
f) 储气罐特种设备证书;
g) 紧固件、连接管路等是否有松动现象;
h) 电源及接线是否满足要求;
i) 连接件形式、尺寸是否符合标准;
j) 是否遵从焊接规范和标准;
k) 材质是否与供货商提供的证明相符(内部件,外壳等)。
② 测试
a) 电气和机械功能测试;
b) 气动回路密封测试;
c) 开、关运行时间控制检测;
d) 限位装置操作的检测;
e) 执行机构行程或扭矩的检测;
f) 其他相关标准与规范规定的测试要求。
③整体测试
执行机构单独测试完成以后,还应与阀门组装后进行整体测试。整体测试内容包括如下:
a) zui小动力气源压力下zui大载荷(dpzui大)开阀性能与时间的测试;
b) zui小动力气源压力下无载荷(dp=0)阀门开关性能与阀门开关时间的测试;
c) zui大动力气源压力下zui大载荷(dpzui大)开阀性能与时间的测试;
d) zui大动力气源压力下无载荷(dp=0)阀门开关性能与阀门开关时间的测试;
e) 机械限位装置操作的检测和电子限位信号反馈的检测;
f) 每次操作的气体耗量;
g) 其它内容测试。
(5)设备运抵安装现场后,由供货商与业主共同开箱检查,发现问题,由供货商负责解决(即使在供货商工厂已试验过且已通过出厂验收)。
(6)在现场验收试验前两星期,供货商应事先提出试验计划,并须征得业主的批准。现场试验合格后,由用户预验收。
(7)在设备安装和投运期间,供货商应派遣有经验的工程师到现场指导,协助并监督气动执行机构及其附件的安装并保证其投入正常运行。
4)铭牌/标志
气动执行机构上必须提供*性防腐蚀的不锈钢标牌,该标牌的固定方式不应采用粘贴的方式。根据产品类型,上根据气动执行机构具体类型,应包括以下相关方面的内容:
(a) 仪表位号(由买方提供);
(b) 用户名称及工程名称;
(c) 规格型号;
(d) 产品系列号;
(e) 供货商/制造商名称及其商标;
(f) 压力等级(如需要);
(g) 主要材质(如需要);
(h) 介质流向(如需要);
(i) 防爆标志(区域分类)(如需要);
(j) 防护等级标志(ip代码)(如需要)。
5)供货范围及界面
(1)根据工艺操作的要求,所提供的气动执行机构是一种低故障概率设备(pfd——probability of failure on demand),通常应包括气动驱动装置、电磁阀、限位开关、回讯器、气动三联件(气源减压/稳压阀、过滤器、油雾器)等,气动驱动装置应为气缸式结构。
(2)采用管道天然气作为动力气源的执行机构还应配套提供气源处理系统、气源气取压的截断球阀(二次阀)、每台阀门3米取压管线以及相关连接附件等。
(3)气动执行机构供货商应根据本技术规格书和相应的数据单要求提供气动执行机构和气动执行机构选型计算书,同时结合的工艺阀门的技术规格书及数据单,一并作为供货商投标的依据。气动执行机构由阀门供货商负责总装,调试验收合格后成套向业主供货。
6.11.7 控制阀
1)设计与制造
(1)一般要求
控制阀的选型和尺寸应根据操作和设计的参数计算,设计参数指:压力、温度、允许压降、流量、流体的成份、允许的渗漏量要求和zui大噪音等级等。所有的计算应符合isa标准。
控制阀的尺寸应允许在zui大的流量条件下,阀的开度85%,zui小的流量条件下,阀的开度不低于5%。出站压力控制阀门在zui大流量的工况下阀门全开时压降必须在0.015mpa以下。供货商应向业主和设计方提交所有的计算书。
所有阀体上应清楚地标出流体的流动方向。通过附在阀杆或阀轴上指针的移动显示阀的开启度。
控制阀的性能参数见控制阀数据表。
①泄漏
阀的泄漏等级应执行ansi/fci-70-2的标准。阀座的泄漏应能够达到或超过ansi/fci-70-2标准中第ⅳ级。
压差≥3mpa的工况,为防止间隙流对阀门内件的破坏,泄漏等级必须为v级。
zui大的关断压差应在控制阀选型中进行计算和说明。zui大关断压差应该在控制阀选型参数数据表中说明。对于执行机构的选型,应提供执行机构的负荷计算。计算书中要求说明执行机构zui小的负荷参数,在zui大关断压差下阀门所需的推力以及执行机构所能提供的推力,以满足控制阀zui大压差工况下的关断要求。
②控制阀计算
应根据输送介质的设计参数(温度、压力、阀两端差压、流量、流速、粘度、密度、允许的渗漏量、zui大噪音等),计算并选择适当的控制阀。
控制阀的尺寸应按照在zui小差压zui大流量条件下,阀的开度在5%~85%之间进行计算。所有的计算应符合isa s75.01标准。供货商应在技术建议书中指出与isa公式不同之处及其原因,并说明优点。
控制阀内件需有足够的阻力通道或减压级,对于油品介质,保证在zui恶劣的工况下阀门出口介质流速必须≤6.0 m/s 。
在zui恶劣的工况下,距离阀门1m处的噪音必须小于85db。对于油品介质,噪音计算应符合isa sp75.17标准。
对于阻塞流工况,应提供气蚀、流速以及噪音计算书。
流量计算必须以zui大流量的110%为基础。
供货商应提供所有操作条件的计算书,计算基础数据和结果应以书面方式说明。
供货商应负责对控制阀和执行机构的选型和计算,使阀门满足zui低精度要求。
在工艺系统中,每个控制阀门的调节范围应满足所有定义的流量条件。定义的zui小流量条件也应为可控制的。
(2)阀的类型
供货商应依据实际操作条件,提供适合本工程工况条件的适当类型的阀门。
供货商所提供的控制阀必须满足气蚀指数大于系统气蚀指数,并提供阀门的气蚀指数值参数。
①球阀
球阀具有近似全通径的阀内球体沿着阀杆能90°转动,改变阀内流通面积,达到控制流体的目的。球阀的主要部件包括:阀体、阀内件、密封环、阀杆等。
球阀可以考虑为在节流或者关断条件下使用,需使用式球体或者近似式球体的球阀,使用双密封环结构的球阀,满足双向密封的要求。不能采用部分球体式的球阀。
出站压力控制、中低压差(≤3.0mpa、压差比(△p/p1)≤0.6)工况下应选用调节球阀。
对于差压≥3.0mpa、压差比(△p/p1)≥0.6的工况下的控制阀宜选用多级减压阀芯的控制阀。
②轴流控制阀
轴流控制阀是指在阀内部和阀体外部所形成直线形对称无限制的路径。轴流式控制阀的主要部件包括:阀体,阀内件,活塞杆,阀杆和卧式笼套等。卧式笼套包括普通笼套和多级笼套,活塞沿着阀体的中心线移动,活塞由一对滑动的齿竿90°传动。阀门为一体型设计。
多级笼套是由多层同心笼套组合而成。每层笼套布有钻孔;介质通过各层笼套的钻孔时,因节流而减压;通过钻孔后介质因流通空间膨胀而减速。介质通过多级笼套,达到分级减压和控制流速的效果。
多级降压工况,轴流控制阀应审慎使用, 使用时应经业主批准。
③直通式控制阀
直通控制阀是指阀芯动作和管道流向成直角的阀门形式。直通控制阀的主要部件包括:阀体、阀盖、阀芯、阀杆和阀笼等。阀体为一体型设计,直通控制阀为顶装式控制阀。
直通控制阀根据流量特性和应用工况,可以有多种内件组合,例如线形阀笼、等百特性阀笼、多级减压阀笼、迷宫式阀笼、串连式多段逐级减压阀芯等等。
单级阀笼有钻孔或窗口,阀芯在阀笼中上下移动,通过控制阀笼的环绕流通面积,达到控制介质的目的。
多级减压笼套是由多层同心笼套组合而成。每层笼套有钻孔;介质通过各层笼套的钻孔时,因节流而减压;通过钻孔后介质因流通空间膨胀而减速。介质通过多级笼套,其流速得到减慢和控制,从而达到分级减压的目的。
迷宫式笼套则通过强制流体流过弯曲的路径,控制介质进入阀内件的流速。经过这些转角,流体在阀内件出口速度受到限制、降低压力。迷宫笼套式控制阀它由阀杆、阀芯、阀盖、法兰盖、盘叠和阀内件等组成。
出站压力控制和中低压差(≤3.0mpa)工况,宜选用单级阀笼。在大压差(≥3.0mpa)工况,为避免堵塞,应使用免堵型结构阀笼,宜选用迷宫式阀笼或多级减压阀笼的直通式控制阀。
④其它
其它类型的控制阀需经业主批准方可采用。在特大压差(≥5.0mpa)、高流速、高冲击和大落差的工况下,推荐使用串连式多段逐级减压阀芯。
(3)阀门的技术要求
①阀体
a)可选择尺寸
控制阀计算口径可选如下尺寸
1/2,1,11/2,2,3,4,6,8,10,12英寸或更高。
不可使用不符合标准尺寸的阀。
在通常情况下,控制阀的正常尺寸不超过管道的尺寸。
b)连接
法兰连接:
通常所有的控制阀应为法兰连接,除非技术规格书要求更高的等级或不同类型的连接方法。法兰应遵从标准 ansi b 16.5 ,一般情况法兰密封面型式采用平面(ff、pi≤300lb)为zui低的标准,根据介质压力等级,法兰密封面型式可以采用凸面(rf、300≤ pi≤900)或密封环连接面(rtj、pi≥900)等型式。法兰密封面型式由业主或设计批准后确定。
除非特殊注明,带有法兰的控制阀,供货商应提供配对的法兰、密封垫圈、紧固件并分项报价。其中密封垫圈必须为两副,用于打压试验后更换。
焊接连接:
控制阀采用焊接连接时,焊接阀门端部应按asme b16.25加工,端部壁厚应符合数据表的要求。
②阀内件
a)流量特性
在正常操作条件下,若控制阀上的压降≥控制阀全关状态下压降的60%,(如分输进罐调压阀)控制阀的流量特性必须使用线性特性。
所有其他的情况下(如出站压力控制),控制阀的流量特性应使用等百分比或修正等百分比特性。
控制阀的流量特性在数据表中有明确规定。
其它被证明是有效的特殊的流量特性。需经业主同意后方可采用。
b)流体方向
液体应用下的流体方向应为流动到关。
c)阀内件设计
阀内件应为快速更换型,易于维修。不应有焊接方式固定在阀体或阀盖上的内部元件。为了减少振动,阀内件所产生的压降应与阀芯的压降相同,卖方所选择的控制阀的阀内件应满足本技术规格书的要求。
阀内件设计应优先选择免堵型结构。可以允许9mm以内的颗粒顺利通过流道,属于免堵型结构;可以允许6mm以内的颗粒顺利通过流道,属于抗堵型结构;可以允许3mm以内的颗粒顺利通过流道,属于易堵型结构。
由于原油和成品油含有颗粒,容易造成阀门堵塞。因此,考虑维护方便,抗堵型和易堵型结构的控制阀阀芯结构形式优先选用顶部卡入式安装结构,轴向安装设计应审慎使用,使用时应经业主批准。
供货商应提供zui近五年的控制阀阀内件设计经验。
③阀盖
一个标准的阀盖应满足-29°c 到 232°c的温度范围。在低于-29°c的环境下,阀体应采用适当的低温阀体材料;在低于-29°c的环境温度和介质温度高于232°c时,阀门结构上应考虑使用延长颈的阀盖等措施,供货商对所采用的材料(包括密封材料)应加以说明,确保阀体满足环境、介质温度要求。
业主应对推荐的方案进行评估和研究。
4振动
合适的控制阀的选择应能保证能量散失的要求,此能量散失不包括管道系统的zui大振动和阀内件材料的磨损。卖方在选择控制阀阀内件时,应考虑振动和阀内件磨损所引起的控制阀的zui大磨损。
⑤气蚀和闪蒸
根据标准isa s75.01《控制阀口径计算公式》,供货商计算时应输入介质的气化蒸汽压,以预测介质在阀门内可能产生气蚀、阻塞流和闪蒸条件的严重性,并根据气蚀的严重程度选择适合工况的阀芯以消除气蚀。
消除气蚀的阀芯具有以下特点:
· 多级减压;
· 流道逐级扩大;
· 流体进入阀芯时转换成多条细流,以消弱其能量;
· 流体经过多级转向和弯曲的路径降低流速;
对于气蚀,应提供足够的压降级数,保证流体在通过阀门的过程中压力始终保持大于饱和蒸汽压。供货商应建议压降的级数,能够避免气蚀现象的发生。
对于闪蒸,阀芯、阀座等应做硬质合金堆焊处理,阀杆应采用高硬度的材质,以提高抵抗闪蒸冲刷侵蚀破坏的能力。
(4)执行机构
供货商应根据阀门计算的zui大关断压差下阀门所需的推力以及相应型号的执行机构所能提供的推力,配置执行机构。
zui终所选执行机构的大小应使用供货商提供的公式进行验证。
执行机构应接收4-20ma dc 的模拟控制信号,输出4 -20ma dc的阀门开度信号,输出spdt的故障信号,触点容量:24vdc 3a。
执行机构内部之间的配管、管件和阀门的材料应采用aisi316不锈钢。尺寸应为ansi b 1.20.1 1/4″npt或1/2″npt。所有连接处不得有泄漏。
执行机构的接线端子板应密封在单独的防爆盒(箱)内,端子应有标号,以便于接线,同时应有接地端子或接地螺栓。电源电缆的电气接口应与控制电缆的电气接口分开,没有使用的接口应用金属接头密封。接线盒应做为执行机构的一部分。电气接口应为ansi b1.20.1 至少具有 11/4″npt螺纹接口 1 个和3/4″npt螺纹接口 3个。
由阀门供货商负责执行机构和控制阀的成套。
①气动执行机构
控制阀的执行机构为气动执行机构
气动执行机构应采用隔膜或活塞作为执行元件。带有气动薄膜或活塞类型的控制阀通常操作在20-600kpa量程范围内工作。
气动薄膜执行机构应足够大,以便能够承受阀座上的不平衡力,在冲击的情况下稳定操作或给阀门提供所需的切断力。
活塞式执行机构应采用平衡位置的整体安装方式。供货商应提供气动执行机构所需的所有设备,包括失效安全所需的保护设备,如:气体储罐、换向阀等。
用户为气动执行机构控制阀提供0.5mpa的气源。投标商应提出对气源的技术参数要求。
执行机构的选择zui终应由供货商或承包商按照标准公式进行核准。
顶部安装的执行机构应由耦合器、手轮、机械阀位置指示器、限位开关、阀门定位器以及执行机构正确操作所需的设备构成。
阀门定位器可接收4 -20ma dc (二线制)的模拟控制信号,其精度要优于满量程的±0.075%,信号分辨率应大于0.025%,并能接收基于hart通信协议的数字信号、具备在线故障自诊断功能,并配有过滤减压阀。可用手持编程操作器对其进行零点及量程的调整。供电电源应为24vdc。
阀门开度转换器应输出4 -20ma dc(二线制)的模拟信号,其精度要优于满量程的±0.5%。
故障输出信号(spdt),触点容量:24vdc 3a。
在执行机构上便于人工操作的位置应配有手轮装置,在无气源的情况下手轮可开启和关闭控制阀。并应保证zui大差压时仍易于进行手轮操作。手轮的旋转应是顺时针关闭。在操作过程中以及在开启点,所需手轮zui大操作力不应超过250n,以保证一个操作工无需加力工具可以操作。
气源的入口处应安装精度为:0.5级、φ60mm、量程0~1.0mpa压力仪表。
②电液执行机构
电液执行机构应包括集成型电液动力装置、蓄能设备、联轴器、手动操作装置、电磁阀、按钮、接线盒、电控箱以及其它设备。
电液执行机构应结构紧凑、模块化设计,自带封闭油源,无需外接油源和管路。控制器和执行机构应为一体结构。
电液执行机构的工作原理:由一个以微处理器为核心的控制器控制,以泵驱动液压油从双作用油缸的一端到另外一端的工作方式,一旦到达了正确的位置,驱动泵的电机停止且不需要动力来维持。以避免马达长期运行影响寿命,并要求采用步进或伺服电机。
电液执行机构应保证控制阀的全行程时间10~30s可调,并可根据设计出厂设定。在电液执行机构故障时,输出故障信号,信号为触点信号(spdt),
电液执行机构的zui大推力不应低于zui大关断压差下阀门所需的推力的1.25~1.5倍,同时,zui大推力不能高于阀门机械结构允许的承受力,应具有可靠的推力过载保护功能;zui终所选执行机构应使用供货商提供的公式进行验证。
执行机构应适合所处位置环境温度的要求。在不能满足该要求的部位,应采用相应措施(如:电加热器),保证相适应的温度。
执行机构应可以接受以下阀门的控制信号:阀门调节信号,esd信号。其中阀门调节信号为4~20ma,esd信号为继电器输出的有源(24vdc)触点信号。
输出4~20ma dc的阀门开度信号,该位置变送器应为有源型,工作电压24vdc,输出信号的精度应达到0.1%以上。
执行机构的定位精度应高于0.2%,重复性高于0.15%,死区应可调。
用户为电液执行机构的动力提供以下电源: 380vac,三相,220vac,单相。电源的电压处于额定电压的±10%范围内,工作频率处于额定的±2hz范围内,电液执行机构应能正常工作,不应因为电源的波动影响执行机构的正常工作。执行机构供货商在报价文件中应列出执行机构使用的电源及功率消耗。
在执行机构便于人工操作的位置上,应配有手轮装置,并应保证zui大差压时仍易于进行手轮操作。手轮的旋转应是顺时针关闭。在操作过程中以及在开启点,所需手轮zui大操作力不应超过250n,以保证一个操作工无需加力工具可以进行操作。
执行机构具有就地手动、就地自动和远程控制选择开关。就地手动位时,由执行机构手轮操作;就地自动位时,由就地按钮操作;远程控制位时,由远方控制按钮或站控制系统程序自动控制操作。就地自动控制或远方控制时,手轮应能自动脱离操作位置,不应随执行机构的动作而动作。
在就地/远方操作切换时,就地/远方操作的切换状态信号输出到站控制系统,状态信号为触点信号(spdt)。
执行机构的现场电控箱内应有开、关和停按钮,执行机构可以停在阀门全行程的任何位置。
电液执行机构应有蓄能设备,当执行机构动力电源中断时,保证阀门能运行到的开关位置或维持原位。
执行机构本身应有机械式位置指示器,指示器的zui小刻度为1mm。
执行机构上应设全开和全关状态的限位开关,状态信号为触点信号(spdt)。
执行机构状态接点容量:24vdc 3a。
执行机构在安装前应保证有足够阀门正常工作的液压油。液压油应能在现场条件下正常工作,报价书中应提供液压油的品牌及性质,便于用户日后采购。
电液执行机构应加装液压油罐油位传感器,用于故障锁定和报警。
处于动态调节过程中的执行机构,噪音在1米内应小于85db。
电液联动执行机构的配管、管件和阀门应采用aisi ss316不锈钢。
电液联动执行机构内部材料应采用为aisi ss316不锈钢。
维护间隔:250000个全行程。
设计寿命:216000小时/1000000个全行程。
控制精度:优于0.15%。
半年运行稳定性:优于2%。
重复性:优于0.1%。
响应时间:小于0.2s。
频响:大于3hz。
执行机构的接线端子板应密封在单独的防爆盒(箱)内,端子应有标号,以便于接线,同时应有接地端子或接地螺栓。电源电缆的电气接口应与控制电缆的电气接口分开,没有使用的接口应用金属接头密封。
电连接应在接线盒的适当位置,接线盒可做为执行机构的一部分。提供给用户的接线孔应有:2×1/2” npt(f)和2×1-1/2” npt(f)。
执行机构的所有电气部分都应能满足现场防爆等级和防护等级的要求,防爆等级应不低于exdⅱbt4,防护等级应不低于ip65。
③电动执行机构
执行机构应选用调节型的电动执行机构。执行机构应与所选用的控制阀类型、尺寸等相配套,根据控制阀的类型,执行机构可以是直行程也可以是角行程。
执行机构应按照阀门在zui恶劣的操作条件下工作进行选择。执行机构整体组装应该是密封的,适合于户外操作。
执行机构的输出力矩、行程、响应速度等技术指标应与控制阀所需的力矩、行程、响应速度等技术指标相匹配。电动执行机构输出力矩应能保证可靠地驱动实际工作条件下的阀门,特别是保证在zui大设计压差下启闭阀门而不需任何辅助设施。电动执行机构的输出力矩由阀门生产厂家根据阀门和阀杆尺寸、类型、管道的压力、温度、zui大差压(见数据单)以及流体类型选取确定,并应留有1.25倍的安全系数。
执行机构的动力电源应优先选用220vac,50hz或三相四线制380vac,50hz交流电源,其内部电气元件及组件的耐压等级不低于450vac。
执行机构内部控制电路电源为单相直流24v,该电源可由电动执行机构本身提供。
执行机构接收来自控制系统的4~20madc的模拟控制信号,并能输出4~20madc的阀门开度反馈信号。
电动执行机构内部控制器的精度应≤±1%,在相同方向要使电动执行机构动作需要的zui大信号变化量为±1.0%。
电动执行机构本身应有状态指示和开度指示。执行机构应带有限位开关,当阀位处于全开或全关位置时,限位开关应能输出spdt类型的无源接点信号。
执行机构的电机应能够在线直接操作,其绝缘等级不应低于f级。
执行机构的电机应能承受zui不利条件下产生的机械和热应力,并能保持连续调节,而且执行机构zui少应满足每小时启动1200次。
执行机构电机的任何部分都不能超过其允许的温度,在定子或线圈上应安装有温度开关,当电机内的温度超过允许值时,应能自动断开绕组电源,以防止电机过热或烧毁,同时发出故障报警信号。
执行机构的电机应具有过载保护功能,当阀门卡死或过负荷等造成电机电流过大时,过载保护单元应切断电机电源,以保护电机不受损害。
电动执行机构应具有限位保护、过力矩保护、正反向联锁保护,电机过载、过热、断相、错相保护,防冷凝的加热保护和控制回路过载与短路保护。同时应能检测断相并具有相位自动校正能力。当电动执行机构出现任何故障时,应能输出spdt类型的故障报警触点信号。
执行机构的所有电气部分都应能满足现场防爆、防护等级的要求,防爆等级应不低于exdⅱbt4,防护等级应不低于ip65。
执行机构的接线端子板应密封在单独的防爆盒(箱)内,端子应有标号,以便于接线,同时应有接地端子或接地螺栓。电源电缆的电气接口应与控制电缆的电气接口分开,没有使用的接口应用金属接头密封。
在执行机构上便于人工操作的位置应配有手轮装置,并应保证zui大差压时仍易于进行手轮操作。手轮的旋转应是顺时针关闭。在操作过程中以及在开启点,所需手轮zui大操作力不应超过250n,以保证一个操作工无需加力工具可以操作。
电动执行机构具有就地手动、就地自动和远程控制选择开关。就地手动位时,由执行器手轮操作;就地自动位时,由就地按钮操作;远程控制位时,由远方控制按钮或站控制系统程序自动控制操作。就地自动控制或远方控制时,手轮应能自动脱离操作位置,不应随电机的转动而动作。
执行机构的齿轮应采用润滑油或润滑脂,供货商应提供采用的润滑油(脂)的牌号和主要指标。对应用于环境温度较低的站场,应考虑加热器,但增加加热器后不能降低执行机构的防爆等级。
(4)附件
①附件要求
根据控制要求,控制阀可能需要一个或更多的以下附件以达到控制阀正常的功能:
· 手轮;
· 电磁阀;
· zui小停止装置;
· 限位开关;
· 密封设备;
需要附件的地方应由工厂安装并接线,并配不锈钢套管、部件。
②手轮
优先选择侧面安装连续可脱离型手轮。
组成紧急切断系统的控制阀不配有手轮。
③电磁阀
选择两位三通直动式电磁阀。
④机械限位
当工艺设计要求时,提供防止阀门完全关闭或完全打开的机械限位机构。
机械限位机构作为机械设备安装在执行机构上,但不能构成手轮机械的组成部分。
⑤限位开关
限位开关是在完全打开或关闭位置上阀位指示的一种。
开关为单刀双掷型,以显示开/关的位置,其信号应连接到阀上的接线盒内。
2)铭牌
根据合同文本,每个设备提供不锈钢铭牌。标牌应为矩型,尺寸符合厂家标准。使用不锈钢螺钉固定标牌,不可使用粘贴的方法。
至少标明如下信息:
a) 阀的位号;
b) 执行机构的系列号;
c) 阀的系列号;
d) 执行机构的技术数据;
e) 操作压力;
f) 故障时操作模式;
g) 厂家名称及商标;
h) 阀体和阀芯尺寸、材料及阀芯的类型;
i) 阀体和法兰等级;
j) 流体方向;
k) 阀流量参数;
l) 电操作机构和保护;
m) 扭距开关设定;
n) 调节比;
o) zui大额定输出扭距。
3)材料
(1)阀体材料
阀体、阀盖、法兰内流件的材料,应根据设计条件和制造要求选用,并应符合astm a105、astm a182、astm a216、astm a352、astm a217和astm a351的规定。各种材料的压力-温度等级按asme b16.34的规定。
每种代用材料必须经买方同意。代用材料必须等同或更优于规定的材料,其性能均要满足原规定材料的要求,且应在产品规格书中注明代用材料的物理、化学、机械性能,热处理、晶粒度、制造方法、冶炼方法等内容。
严禁使用铸铁阀体。
需要焊接的碳钢阀门的zui大含碳量为0.25%,且需与技术规格书中给出的工艺母管材质相同 。
dn<100的合金钢阀与不锈钢阀的支架宜与阀盖材质一致,dn≥100的合金钢阀与不锈钢阀的支架材质可为wcb。
阀体和阀盖的材料,如:螺栓、螺帽等应符合相关的技术要求。
对于强腐蚀性的介质,应考虑控制阀体的内部增加防腐内衬。
对于有冲刷侵蚀,阀体内小流量影响区域必须用硬质合金焊接覆盖。以下工况应采取硬质处理:
a) 压力降大于3.0mpa的所有类型的流体;
b) 流体含有腐蚀性的颗粒。
一个标准的阀体应满足-29°c 到 232°c的温度范围。在低于-29°c的环境下,阀体应采用适当的低温阀体材料;在低于-29°c的环境温度和介质温度高于232°c时,阀门结构上应考虑使用延长颈的阀盖等措施,供货商对所采用的材料(包括密封材料)应加以说明,确保阀体满足环境、介质温度要求。
业主应对推荐的方案进行评估和研究。
(2)阀内件材料
阀内件的材料,应根据设计条件和制造要求选用,并应符合astm a105、astm a182、astm a216、astm a217和astm a351的规定。各种材料的压力-温度等级按asme b16.34的规定。
接触介质的阀内件,严禁使用铜或铜合金,包括黄铜和青铜.
密封面为堆焊的阀芯,阀座环,其材料的耐蚀性应至少等于壳体材料。
除特殊要求外,锻件可代替铸件。但锻件作为受压元件时,未经买方允许严禁使用铸件代替。
阀芯与阀座、阀杆与其配合零件之间应保持硬度差zui小值为hb50,当两个表面均为硬质合金硬化表面时,则不要求该硬度差。
除非流体和条件要求更合适的材质,阀芯、阀座密封环和阀杆应为aisi 316不锈钢,或等同以上的材料。
以下工况,阀芯和阀座应进行表面堆焊硬质处理:
气蚀和闪蒸工况
腐蚀性的流体。
软阀座不推荐使用。特殊情况下选择带有软阀座的单级笼套阀芯或球阀应说明其严密性。
当出现闪蒸工况时,阀芯、阀座等应做硬质合金堆焊处理,阀杆应采用高硬度的材质,以提高抵抗闪蒸冲刷侵蚀破坏的能力。
4)检验和测试
控制阀和执行机构以及阀的配件在控制阀的工厂组装、安装和试验,期间经以下人员检验:
业主或业主的代表。
根据现行的规范和标准进行试验。业主代表应能够监视所有的试验过程。
试验之前一个月供货商通知业主,以便为监督试验达成一致意见。供货商应首先应完成内部试验,并将记录在测试前两个星期提交业主。
对于控制阀需要提供以下文件:
a) 化学分析:
控制阀使用的材料应有化学分析试验证书,证书应符合din50049 3.1.b 的要求。
b) 机械特性:
承包商有责任提供符合din50049 3.1.c的试验证书。
(1)工厂验收试验
控制阀和执行机构以及阀的配件在出厂前应根据有关规范进行工厂试验,以证明所提供的设备在各方面均能完全符合买方的要求。
除特殊说明外,所有控制阀均应由制造商按api598或asme b16.34进行检验。
所有的控制阀均应按api598或asme b16.34的要求进行壳体试验和密封试验。
所有的控制阀均应按api598或ansi/fci70-2的要求进行泄漏试验。
制造商应在阀门组装好后进行试压,所有的零件和附件均属承压范围。试压时,手动或齿轮驱动的阀门,其闭合扭矩应由手动获得。奥氏体钢阀门的水压试验用水的氯离子含量应小于25ppm。
水压试验后,阀门应完全排净,并用干燥空气或氮气进行干燥。
供货商应向买方提供每台控制阀的出厂测试报告及质量检验报告,该报告应是具有签署和日期的正式报告。
供方必须对所供设备进行100%的试验和检验,其内容至少应包括:
①静态测试
数量检查(包括附件);
外观检验(包括漆面质量、表面光洁度等检验);
尺寸检测;
标牌标识是否完整、清晰;
防爆等级的认证证书;
紧固件等是否有松动现象;
连接件形式、尺寸是否符合标准及数据表的要求;
是否遵从焊接规范和标准;
材质是否与供货商提供的证明相符(内部件,外壳、连接件等)。
②动态测试
控制精度;
全行程时间;
复现性;
绝缘性能试验;
阀座泄漏测试;
压力测试(包括配套电液/气液执行机构);
气动/电动/液动功能测试;
阀门吊装;
其它内容测试
(2)现场验收试验
控制阀运抵安装现场后,由供方与买方共同开箱检查,发现问题,由供方负责解决(即使在供货商工厂已试验过且已通过出厂验收)。
在现场验收试验前两星期,供方应事先提出试验计划,并须征得业主的批准。现场试验合格后,由用户预验收。
(3)试运行/运行试验
作为zui低要求,如果现场允许,与工厂测试同样的测试应在现场重复,来完成现场验收试验和试运行/运行,接受定单一个月后,供货商应建议现场验收试验程序,并提交业主批准。供货商负责现场技术服务。
5)供货范围及界面
供货商提供的控制阀应包括:控制阀本体、配套的执行机构、配套的过程连接法兰和相关附件。
6.11.8 限流孔板
1)设计与制造
(1)限流孔板的压力等级在环境温度及操作条件下应大于等于安装管道的设计压力。
(2)供货商应根据《限流孔板数据表》所提供的参数数据,经计算后选择合适的孔板。若有必要,可以采用多级孔板进行限流。为了便于现场安装,供货商所提供的限流孔板(包括多级限流孔板)应该在工厂集成为一体,两端以法兰方式与管道连接,并配套提供接管法兰、紧固件。
(3)限流孔板材质的选择应不低于aisi 316 ss (astm a 167-54),限流孔板的厚度应能承受现场高差压的冲击。
(4)限流孔板在工作时,距离1m处zui大噪音不应大于85db。
(5)限流孔板在工作时不能引起管道的振动。
(6)限流孔板处不得有油品泄漏。
(7)限流孔板及附件应能保证:在管线运行后其寿命应不低于25年。
(8)供货商应根据《限流孔板数据表》所提供的参数数据,对所提供的限流孔板进行计算,关提供计算书。
2)材料
(1)供货商应对限流孔板工作在zui高设计压力条件下所采用的材料耐压等级是否能满足要求进行核算,并提供充分的书面依据。如果不能满足,应提高对限流孔板的耐压等级或采用适当的材料。
(2) 限流孔板内部的所有与油品接触表面应用抗腐蚀材料制造。
(3 )限流孔板外部应选用适应环境条件的抗腐蚀涂层进行保护。
(4 )供货商应提供主要零部件材料化学成分、机械性能、无损检测报告。3)检验和测试
(1)工厂验收试验
限流孔板及辅助设备在出厂前应根据有关规范进行工厂试验,以证明所提供的设备在各方面均能完全符合买方的要求。必要时,买方及其代表有权利到卖方工厂进行监督试验及验收,供方应提前两星期以书面方式通知买方及其代表。
限流孔板应依据相应的工业标准或其它的管理规范进行出厂测试。
供货商应向买方提供每套限流孔板的出厂测试报告及质量检验报告,应是具有签署和日期的正式报告。
供方必须对所供设备进行100%的试验和检验,其内容至少应包括:
压力测试;
数量检查(包括附件);
外观检验(包括防腐质量、表面光洁度等检验);
尺寸检测;
标牌标识是否完整、清晰;
连接件形式、尺寸是否符合标准;
是否遵从焊接规范和标准;
材质是否与供货商提供的证明相符(内部件,外壳等)。
其它内容测试。
(2)现场验收试验
限流孔板运抵安装现场后,由供方与买方共同开箱检查,发现问题,由供方负责解决(即使在供货商工厂已试验过且已通过出厂验收)。
在现场验收试验前两星期,供方应事先提出试验计划,并须征得业主的批准。现场试验合格后,由用户预验收。
在设备安装和投运期间,供方应派遣有经验的工程师到现场指导,协助并监督设备的安装并保证其投入正常运行。
4)供货范围及界面
供货商应提供限流孔板及配套附件。
6.11.9 plc控制系统
1) 总则
严格遵守国家的法律法规,执行国家及行业版本或上先进的、版本的标准、规范。
plc控制系统将自动、连续的监视和控制储气库的运行,保证人身、站场、设备安全。
采用的设备、控制系统及材料应是技术先进、性能价格比高,能满足所处环境和工艺条件、在工业应用中被证明是成熟的产品。
2)系统总体要求
(1) 系统硬件及软件配置必须为近来发展和改进的新技术、新设备和新系统,并经过现场验证具有先进性及可靠性。为方便系统的扩展,系统的硬件应为模块化的结构。i/o模块具有抗机械冲击和抗电磁干扰能力,同时还具有电气隔离功能,i/o模块允许带电插拔,方便地进行在线更换。触摸屏不小于8"lcd,分辨率不低于800*480,24bit。系统能以通讯方式调取其余主要厂家plc数据,系统应具有支持主要厂家的接口。
(2)系统启动时间即从发出指令到屏幕上显示有关图形或数据的时间,应符合上述要求:
冷启动或掉电后重新启动:<300s
热启动或复位后启动:<250s
(3)系统性能指标:
系统数据更新≤1s
显示时间精度:±1s
图形画面调用≤2s
动态数据组≤2s
控制触发≤1s
窗口显示≤1s
目标菜单调用≤1s
报警一览表更新≤1s
报警确认≤1s
(4)系统的自诊断率不低于90%,自诊断应覆盖每一个通道。
(5)当所有备用i/o卡件均接入系统后,系统的软件容量和通讯负荷率不应该超过50%;当所有备用点数均接入系统后,电源负荷及cpu负荷均不应超过60%。
(6)系统应具有设备管理功能,能够通过hart协议(ai和ao通道)与现场设备进行通讯,在线对设备进行诊断,并远程修改仪表参数,设备管理应实现通道级(即每个通道均能实现,无须重复设置)。
(7)过程i/o接口类型(i/o分布详见附表一)
①模拟输入: 4~20ma(供电和不供电2种)
支持hart协议
转换精度:zui少为12bit
②模拟输出: 4~20ma;
支持hart协议
转换精度:zui少为12bit,能够驱动至少650欧姆的负载;
③离散输入为24vdc或无源接点, 当离散输入信号为无源接点时,回路电源应由系统提供。离散输出为24vdc/1.;
④带线性化的pt100输入;
(8)i/o模块具有隔离功能,主要指输入、输出间、通道间、电源间的相互隔离。隔离电压:模块到地 1500vac 60s,300vac连续。 输入到机壳 500vac 60s,输入间250vac;
(9)模拟量模块连接的pid回路数不得大于8个。
(10)plc系统ai、ao模块不超过8通道,di、do模块不超过32通道。
(11) i/o模块支持热插拔。
(12)控制器
①控制器cpu应为32bit,其处理能力相当于in 586处理器,cpu负荷不超过60%,控制器内存在现有点正常运行时利用率不超过50%且zui少不低于8mb。当电源掉电恢复后,控制器应不需人工干预而自动重新启动。控制器应采用热备冗余配置,热备冗余控制器能够自动切换,且带有通讯接口,网络接口。热备冗余控制器切换的切换时间应不大于100ms。
②控制器应具有电气和机械隔离,每个控制器均有过电流和过电压保护;
③在失电情况下维持其内存、实时日历、时钟至少一年,电池后备的ram或eprom应能保持其存储的应用程度至少一年;
④更换的控制器应能自动拷贝应用/组态程序而不需要人工下装。
(13)自诊断
系统具有可靠的完善的自诊断功能,诊断可达通道级。且可以诊断输入/输出回路为开路或短路。
(14)供电
除非特别说明,所有现场仪表均由控制系统供电。
系统电源和现场仪表的供电电源应独立设置。系统供电为1:1冗余设置,供电的单个电源可负担整个系统的用电负荷,正常情况下,冗余电源分担整个系统的用电负荷。
系统电源应有超温保护和故障显示功能。
电源应能在线更换,更换电源不能干扰系统运行。
(15)系统安全性
服务器(如需设置)和操作站均设置人员操作权限,对不同级别的操作员、维护人员和系统工程师规定不同的操作权限。
操作站要求采用键锁或软件方式规定其管辖范围。并能进行切换;即当某一操作站发生故障后,另1操作站能进行简单操作后对全区域进行操作。
(16)系统必须提供故障显示及在线诊断功能。
(.17)lisence
投标商应明确各种类型点所用lisence的计算方法,并明确本工程所配置的点数,并保证lisence点数比要求点数有50%的富裕量。
(18)系统的实时性
对于控制回路,控制周期一般按1秒钟考虑。 计算容量与速度时按如下要求进行:
控制周期:0.5s、1s、 2s占有比例:10%、 50%、 40%
开关量控制周期一般按1s,0.5s考虑10%。
数据采集速率一般应有几个速率选择,可按0.5s占20%,1s 占20%,3s占60%计算容量。
(19)系统扩展性
系统在配置时,应留有一定的扩展能力。i/o卡留有20%富余通道。当系统i/o点增加20%时,机柜、电源、软件、通迅负荷和其它各种负荷应能满足这些扩展量。
机柜应留有i/o卡件数量15%的扩展空间,如果卡件需机架安装,则安装机架应一次性提供。
系统应有较好的开放性。操作站操作系统为windows xp/2000/2003 网络协议为tcp/ip。
i/o模块支持热插拔。
3) 控制和数据采集功能
(1 )常规控制功能
控制功能的实现是按照要求把所需的控制功能模块组合在一起,实现常规控制功能的功能模块至少包括下列各类:
pid;
pid带串级、pid带偏差、pid带死区、高低选、三选一、比率控制、斜坡控制;
pid控制必须具有参数自整定功能,手<->自动切换必须做到双向无扰动。
开方运算、加/减运算、乘/除运算;
超前/滞后、延时、阻尼;
高、低、高高、低低、偏差和变化率超值报警;
数字滤波、开/关控制;
手操输出;
前馈、变量增益控制;
(2 )间断控制
用标准功能块或简单的系统控制语言实现顺序控制和逻辑控制。并有计时、计数等模块供组态时选择。
(3 )数据采集功能
控制系统应内置有标准的aga3、aga7、aga8、aga10算法或计算标准,能够方便地进行z值计算。
控制系统应内置有标准的rs485 modbus rtu的通讯接口,能够方便地与现场plc、智能仪表通讯,且每个通信口支持通过软件的设置可以依据第三方设备的要求而任意设置为rs485/rs422/rs232的物理接口。
串行通讯模块必须是和dcs的其他io模块一样,直接安装在dcs系统的io支架上,并通过io bus与控制器直接通讯。不允许采用串口服务器。
(4) 显示功能
画面种类至少包括以下几类:
菜单画面
总貌画面
单点显示画面
报警总貌画面
分区报警总貌画面
趋势组画面
单点趋势组画面
用户流程画面
画面的进入方式可从主菜单开始逐级进入,也可用编号直接调出。另外,一些重要的画面也可以从键盘的予置功能键上直接调出,这些键盘功能由组态时予置。某些画面还可以根据报警等逻辑关系自行调出。系统应保留一定的临时操作组,便于随时加入一些过程点。
(5 )工程技术人员画面
工程技术人员能在该画面上方便地进行系统的生成、用户流程图及各类图形的生成,以及用通用语言或语言生成各类记录、报表。画面至少有:
系统组态画面
用户图形生成画面
语言编程画面
联机记录和报表生成画面
(6 )维护人员画面
维护人员能在该画面上方便地进行整个系统的维修, 在这些画面上能方便地观察到系统发生故障的位置,指导维修人员对全系统进行维护。画面应包括:
系统诊断画面
系统维护画面
系统资源使用情况画面
设备状态画面
(7 )报警功能有:
值及偏差报警
设定点超限报警
开/停报警
输出越限报警
变化率超限报警
系统诊断报警
报警值由操作人员设定或由工程技术人员在组态时设定,并在组态时报警发生后过程变量的颜色,在没被确认前,报警的过程变量以闪动的方式显示,同时可以设定报警的优先级并选择不同的声音级别来区分报警点的重要性。当同时发生多个报警时,首先报优先级高的报警,这可在组态时确定。对系统中所有的报警均进行存贮,保留时间可任意设定。
(8 )打印/记录功能
报表打印、历史趋势打印和流程图打印功能利用配套的打印机完成,供货商应负责打印数据的链接,且报表和历史数据能够进行存储,便于日后查询。
(9 )软件支持能力
必须提供成熟的、丰富的及稳定的软件,以使系统的各种功能得以实现。应详细列出随机所带的软件的目录清单,并对软件的环境和版本加以说明。
当系统软件有修改或升级应及时通知用户,并在保证期后一年内无偿提供给用户。
4) 总线系统
如果采用总线结构,plc系统的配置需满足以下要求:
(1 )总线网段的配电系统
所有总线网段的总线配电器(电源调节器)模块应冗余配置。每台总线配电器模块的通道数不得大于plc系统总线通讯卡件的通道数。总线配电器的网段输出电压不应低于28vdc;总线配电器的网段输出电流不应小于400ma。总线配电器的输出应与系统接地隔离。总线配电器应设有输出短路保护。
总线配电器供电的稳压电源应冗余配置。稳压电源的输出电压为20-35vdc。
总线配电系统应配备配电的自诊断功能,对稳压电源的供电、总线配电器模块的正常工作、总线主干线的过载和短路故障进行诊断和报警。
总线配电系统应支持plc 的冗余总线通讯卡,并可组态成该冗余通讯卡的两路独立接线或合成后的单路接线。
(2) 总线终端器
每个总线网段的两端应各配备一只总线终端器。总线终端器可集成在总线配电系统和现场总线隔离栅中。
(3) 总线网段的拓扑结构和接线箱
总线网段可采用单接线箱结构,或多接线盒结构,每个网段的接线盒数量不得超过4 个。不得采用t 型头连接型式。带机壳的现场总线隔离栅可作为总线接线箱。
所有总线现场仪表的分支导线均应挂接在总线接线箱内的独立端子上。每个分支只挂接一台现场仪表。总线网段的各分支应具有独立的短路保护功能。短路保护电流不应大于50ma。
接线箱安装位置的设计以分支电缆越短越好为原则,每个网断连接的总线设备不应超过10个,其中至少含有增加2台总线设备的余量;每个网段的调节阀不应超过3个,标准控制回路的变送器和调节阀应在同一网段上。一个网段上的分支电缆长度不得大于120米,主干线和所有分支电缆长度之和不得大于1900 米。
(4) 总线电缆
总线主干线电缆应采用现场总线a 型电缆,或其他电气参数指标不低于现场总线a型电缆同等要求的截面大于awg18 的屏蔽双绞线电缆。分支电缆应采用满足fisco要求的现场总线a 型电缆,总线电缆的颜色优选橙色,总线电缆由供货商提供。
5)plc系统机柜
控制器应安装在钢质的机柜内。i/o机架与处理机机架安装在同一面机柜内。需要时,应设与现场仪表、设备连接的接线端子柜。
每面盘/柜的高度不宜超过2m,宽度不宜超过1m。
选用钢质双门或单门标准尺寸柜,门可以180度打开,应为前或前、后开门,门上带安全锁。电缆/电线由机柜底部进出,盘/柜内配线应通过汇线槽。机柜的喷漆应光洁、美观、耐用。机柜应配备散热通风、照明等设施,进风口应设便于拆卸、更换的过滤网。风扇的噪音不应大于40dba。
在机柜设计时,应充分考虑机柜内部和外部电线/电缆的布线空间。每面机柜内安装的i/o机架(槽12~16槽)不应超过2个,plc选用的机架宽度应能安装在不超过1米宽的机柜中,以避免占用过多的空间。柜内安装空间按30%的余量设计。
柜内机架与端子排的布置应考虑留有扩展余地且方便维护、检修,柜内布线通过走线槽,柜下端安装接地母线。
通常,机柜颜色应采用浅灰色(light grey),色标为ral 7035。机柜底座颜色应采用黑色。
6) 布线
柜内布线应采用铜芯电线或电缆。它们的绝缘耐压等级应为额定电压的2倍且不小于500v。信号电缆的线芯截面积不应小于0.75mm2,电源电缆的线芯截面积不应小于2.5mm2,传输模拟信号、脉冲信号、通信信号的电缆/电线应采用双绞屏蔽型。信号线与电源线不应采用同1根电缆。应以颜色区分电缆/电线的用途。线缆的直观部位应打标记符号以便于查找。
应采用笼式弹簧夹持型接线端子连接电缆/电线。接线端子抗拉力值应优于iec60999的要求。
接线端子之间的连接应采用短路片。
与外部的电缆/电线的电气连接应采用接线端子排。接线端子应留有20%以上的余量。接线端子的绝缘耐压等级不应小于500v。
防雷/电涌保护器不应作为与外部的电缆/电线连接的接线端子使用。
7) 防电涌设备
plc控制系统均应在有可能将由于雷击(直击雷、感应雷等)产生的高压导入计算机系统的接口位置设置完善的防雷击和电涌保护措施。至少应对以下的内容进行防雷击和电涌保护:
与通信系统的连接处;
供电系统的连接处;
与第三方的通信接口;
模拟量及开关式仪表的输入/输出接口;
防雷击和电涌的设备应采用可靠性高,并经实践证明过的产品。
电源电涌保护器基本要求如下:
内置过流、过热熔断保护;
劣化时有热脱扣保护装置;
符合ul 1449安全认证,或具有由国家授权的防雷产品测试中心或检验机构出具的检测报告的合格证书。
在一个建筑物内的同一个雷电防护区时,当ups电源(220vac)为过程控制系统提供220vac电源时,过程控制系统电源电涌保护器参数要求如下:
标称放电电流in≥3ka;
电压保护水平up≤1.25kv/1.5kv(线-线/线-地)(测试波形:in,8/20µs)。
在一个建筑物内的同一个雷电防护区时,当ups电源(220vac)输出至直流稳压电源(24vdc),并通过直流稳压电源为过程控制系统供电时,过程控制系统电源电涌保护器参数要求如下:
标称放电电流in≥1ka;
电压保护水平up≤200v/650v(线-线/线-地)(测试波形:in,8/20µs)。
当ups电源(220vac)经过露天进入室内为过程控制系统提供220vac电源时,或对露天安装的现场自控设备(如雷达液位计、分析仪器、泵控制机组或压缩机控制机组等)单独提供220vac电源时,应采用内部能量协调良好的电涌保护器,其参数要求如下:
冲击电流iimp≥15ka;
标称放电电流in≥20ka;
电压保护水平up≤1.5kv(线-线/线-地)(测试波形:iimp,10/350µs)。
对露天安装的现场自控设备(如雷达液位计、分析仪器、泵控制机组或压缩机控制机组等)单独提供24vdc电源时,电涌保护器参数要求如下:
标称放电电流in≥1ka;
电压保护水平up≤200v/650v(线-线/线-地)(测试波形:in,8/20µs)。
用于过程控制单元的信号电涌保护器可带电热插拔。其性能参数应符合8-2的要求。
信号电涌保护器性能参数要求如下表。
12v 脉冲 rs485信号 24v模拟信号
(ai/ao) 24v数字信号
(di/do) 热电阻和热电偶信号
标称放电电流(in)(8/20µs) ≥10ka
电压保护水平(up)
测试波形:6kv 1.2/50µs,3ka,8/20µs;或in 8/20µs ≤60v(线-线/线-地) ≤60v(线-线/线-地) ≤110v/600v(线-线/线-地) ≤110v/600v(线-线/线-地) ≤110v/600v(线-线/线-地)
负载电流能力 高于回路工作电流 高于回路工作电流
对于过程控制系统中的数字量输出为继电器输出的情况时,因电流较大,故电涌保护器的负载电流能力应高于回路工作电流。
爆炸危险区现场仪表的信号电涌保护器应符合爆炸危险区划分,其参数要求如下:
标称放电电流in≥10ka;
电压保护水平up≤85/650v(线-线/线-地)(测试波形:in,8/20µs)。
8) 电源
供货商为plc控制系统提供并联热备冗余配置的交流/直流电源。cpu及i/o模件使用独立的供电回路。系统的外部22vac电源由用户ups提供。
电源相对于输入和输出回路是悬空的。硬件如果有接地现象,系统将自动发出报警信号。报警信号归入到机柜的常规报警信号中。
在不影响系统运行操作的情况下能方便地将故障电源隔离、拆除和更换。
9) 接地
系统柜内应设置仪表工作接地、防雷接地和保护接地,每种接地应单独设置接地汇流铜板,汇流铜板宜采用25mm x 6mm的铜条制作。仪表信号的电涌保护器的接地线应接到工作接地汇流板,其余电涌保护器的接地线应接到防雷接地汇流板。
包括机柜在内的所有金属设备均连接到电气保护接地上,每台机柜都提供一个m10螺钉用于连接电气保护接地。
机柜内部之间相互连接的电缆屏蔽层在供货商提供的仪表接地汇流排上统一接地。
供货商须对每台机柜提供一个接地泄漏检测信号,或提出接地要求。在机柜的常规报警信号中能显示相应的报警。
供货商须明确提出所供设备的接地需求。
10)软件组态
供应商需提供该公司开发的正版软件,软件组态及系统生成由供应商完成,设计单位给予必要的协助。供货商完成工程数据库生成、流程画面制作、实时趋势制作、历史趋势制作(时间长度应可选)、生产报表生成(报表式样由业主提供)、泵状态(泵运行时间及换泵时运行时间的清零),维护手册(中文)、操作手册(中文)编制等,直至调试投产。
11 ) 检验和测试
在合同执行期间,系统的试验、检查、调试和验收主要分为两部分,
工厂试验、检查、调试和验收;
现场试验、检查、调试和验收。
每一步完成之后,均应由供需双方授权的人员签字后方可生效。
供货商在投标文件中应提供上述工作的详细内容、参照标准及执行计划。
(1)工厂试验(fat)
fat的目的是检查整个系统是否达到合同的要求,对系统的功能、性能进行全面的试验、测试和系统联调(系统内部和外部的通信也应包括在内),使整个系统尽可能的完善,减少现场出现问题的机率和修改工作量,为现场调试打下坚实的基础。fat应在供货商的系统集成地进行。fat所需的场地、工具、费用由供货商负责。系统联调应模拟现场实际的通信系统设置。供货商应提出fat的详细计划和工作内容,经业主批准后实施。
所有试验和测试项均应有书面报告,并经双方现场负责人签署视为有效。fat完成后,供货商应提供详细的fat报告,报告经双方签署后,系统才能出厂和装箱发货。
(2)工厂试验(sat)
系统安装完毕投入运行前须进行sat。sat涉及系统所有的组成部分(包括主备通信线路),即使是在fat中已经进行过的测试及试验项。
sat的目的是确保在运输、安装过程中系统未被损坏,所有的接线准确无误,系统功能和性能达到预期的要求,相关设备和仪表运行是否正常、安全保护是否有效等等,保证投产成功。测试包括但并不局限于下列各项内容:
100%功能测试;
100%性能测试;
所有数据类型的i/o点的回路100%检查和功能测试;
单台设备100%监控调试;
各种监控程序与相关设备100%的联调;
与调度控制中心、备用调控中心、所有远方站之间的功能、性能联调。
所有试验和测试项均应有书面报告,并经双方现场负责人签署视为有效。zui终形成sat报告报业主批准。
供货商应提出sat的详细计划和工作内容,经业主批准后实施。
12)供货范围及界面
供货商的工作范围包括:与本项目plc控制系统有关的全部硬件和软件、系统设计、培训、系统集成及制造、编程组态、fat、装箱发运、现场安装及通电试验、现场调试、sat、投产、项目管理、亚博竞彩网站的售后服务等。在本技术规格书中未提及但完成本项目所需的内容和工作也在供货商供货范围之内。
plc控制系统供货商应完成与其余控制系统的数据通信,并负责提供接口文件以及相关通信、系统文件。
供货商的工作范围应包括以下内容,但不局限于此:
根据本技术规格书及其它的相关文件进行plc控制系统系统设计,并提供详细的plc控制系统设计文件(设计文件需经业主和设计批准后方可实施)。
系统集成;
为业主和设计提供软件、硬件培训;
现场操作员培训;
所有应用软件编程组态及调试;为了能够使业主和设计的有关技术人员全面地、深入地掌握该软件,在实际的运行中能够根据需要进一步地开发它,应用软件的编制和组态采用由供货商、业主、设计三方合作的方式来完成。应用软件的编制工作在供货商的工厂完成。供货商应对应用软件的结果负责。
人—机界面(hmi——human/machine interface)的动态画面设计及制作;
与第三方软件或智能设备之间的衔接和测试;
工厂验收试验(fat——factory acceptance test);
装箱发运;
现场安装和通电试验;
现场监督指导与scada系统相关联仪表、设备的接线,配合与调控中心的数据通信;
现场调试;
预投产;
现场验收试验(sat——site acceptance test);
投产;
72小时的运行监护;
提供竣工资料;
提供备品备件;
亚博竞彩网站的售后服务;
项目管理。
系统供货商在系统设计时,应充分考虑到今后的扩展问题。
6.12 电气
6.12.1 防爆
1)橇内所有电气设备的选型均应满足爆炸性气体环境危险区域2区的设备选型要求。
2)橇内所有电气装置的电气设计均应符合gb50058的相关要求。
6.12.2 防雷、防静电接地
1)撬装设备的防雷措施应符合gb50057中第二类防雷建筑物的防雷措施的相关要求。所有非焊接连接和不符合gb50058的相关要求的螺纹旋合连接的金属管道及管件、螺栓孔数小于等于5的法兰等应在连接处采用铜质导体跨接。
2)橇内的所有装置及设备的金属外壳应可靠接地连接,并汇接于一处。应在所有橇外角的底部预留可方便连接至柜外接地体的接地连接装置。橇接地连接应不少于2个点。橇内防静电接地应符合sh 3097。
6.12.3 接线箱要求
调压计量橇仪表检测装置等所有电气部分的控制电缆、 电源电缆, 都应通过防爆接线箱引入或引出,防爆接线箱应安装在合适的位置,以便于现场接线。信号与电源接线箱应分别设置,接线箱内部的接线端子应留有 15%的余量。接线端子应具有防雷、防浪涌保护功能。
接线箱应由供货商负责提供, 并负责从橇装的每个电气设备到接线箱的接线, 连接电缆和接线方式应符合有关的防爆标准的规定。
6.13 仪表及电气配管、配线
1)电缆及绝缘导线应采用铜芯阻燃电缆,信号电缆的线芯截面积不应小于 1.5 mm2 ,电源电缆的线芯截面积不应小于2.5mm2。
2)所有电缆、导线均应穿镀锌焊接钢管保护敷设。电源电缆与信号电缆不应共用一根电缆保护管。电缆保护管与仪表、设备等的连接处应采用防爆挠性连接管,并设电缆夹紧装置以防电缆脱落或扭转。电缆保护管与接线箱连接,应设隔离密封接头。电缆保护管上应设排除冷凝水的密封接头。
6.8.3 线路严禁有中间接头。
6.14 橇体
1)橇体外形设计应在满足安全使用、运行可靠、便于维修的前提下,体积适宜、外表美观。
2)设备和管路间距应便于检修维护,主管路轴线距离以不小于1000mm为宜,工艺管路直管段长度应满足设备运行要求,设备外表面净距离不应小于 500mm。
3)成橇尺寸应满足汽车装运条件要求, 因尺寸过大而无法整体运输时, 应分块成橇运输,其整体组装由施工单位现场完成,由供货商或分包商派人指导安装。
4)橇体工艺管道与橇外工艺管道(包括放散和排污管道)的连接形式为法兰连接。
5)需现场完成组装的分体橇块,各橇块之间连接形式为法兰连接。
6)法兰为突面带颈对焊法兰,法兰、紧固件、密封件应符合 hg20615~20635 标准;
7)法兰、螺栓等连接件应进行热浸镀锌处理,镀锌层重量检验任何一个试样不得小于500g/m2 ,其质量应符合gb/t 13912 标准要求。
8)橇体工艺、电气接口方位根据实际情况由设计方确定,应满足安装方便的需要。
9)距橇体 1m 处噪音值不应超过 85dba。
10)橇体应固定于稳定的支座上,支座材料采用型钢,型钢应满足强度和刚度要求,且厚度不应小于5mm。
7 检验和测试
7.1 工厂验收试验
分输站撬装设备在出厂前应根据有关规范进行工厂试验,以证明所提供的单项设备及整套橇在各方面均能完全符合买方的要求。必要时买方及其代表有权利到卖方工厂进行监督试验及验收,供方应提前两星期以书面方式通知买方及其代表。
设备、管道组装焊接按照规范要求进行无损检测和强度试验,组装完成后对设备整体进行气密性试验、操作试验。出厂测试报告及质量检验报告应是具有签署和日期的正式报告。
供方必须对所供设备进行100%的试验和检验,其内容至少应包括:
7.1.1 静态测试
—数量检查(包括附件) ;
—外观检验(包括漆面质量、表面光洁度等检验) ;
—尺寸检测(包括整体尺寸) ;
—标牌标识是否完整、清晰;
—防爆等级或本质安全设备的认证证书;
—紧固件、连接管路等是否有松动现象;
—电源及接线是否满足要求;
—连接件形式、尺寸是否符合标准;
—是否遵从焊接规范和标准;
—材质是否与供货商提供的证明相符(内部件,外壳、连接件等) 。
7.1.2 动态测试
—阀门准确度测试;
—所有电气设备的绝缘性能试验;
—压力测试(单台设备) ;
—气密性试验(单台设备及整套橇) ;
—阀座泄漏试验;
—其它内容测试。
7.2 现场验收试验
设备运抵安装现场后,由供方与买方共同开箱检查,发现问题,由供方负责解决(即使在供货商工厂已试验过且已通过出厂验收)。
在现场验收试验前两星期,供方应事先提出试验计划,并须征得业主的批准。现场试验合格后,由用户预验收。
在设备安装和投运期间, 供方应派遣有经验的工程师到现场指导, 协助并监督仪表设备的安装并保证其投入正常运行。
8 备品、备件及工具
供货商在投标文件中应列出保障所供设备正常运行两年所需的详细的备品备件建议清单,并提供能够保证备品备件供应的时间、供应方法和渠道。推荐的备品备件及价格在投标文件中按可选项列出。
9 铭牌/标志
设备单体均要求按照规格书相应章节配置单独铭牌进行标志,管道上应做介质流向标志。
站场撬装设备组装完成后, 应按规定设置铭牌, 铭牌内容形式应符合相关标准的规定,至少包括以下内容:
1)介质进出橇体接管公称通径;
2)介质进出橇体压力范围;
3)介质进出橇体标准流量;
4)制造厂名或商标;
5)产品型号等。
10 涂层、包装和运输
1)涂层、包装和运输应符合 jb/ t 4711 的规定;
2)橇体及所有设备、管道的非不锈钢表面(除特别规定外)都应在检测后进行除锈、
防腐处理。供应方应提供表面处理方法、涂层名称、漆膜厚度和防腐寿命等;
3)橇体表面经除锈 sa2.5 级、除污后涂防锈漆两道和环氧树脂涂层两道;
4)防腐涂层外表面还应进行涂色,涂色要求应符合 sy/t 0043 规定;
5)所有涂层均应光滑,无流痕、划痕、漏涂、剥落、气泡等现象;
6)所有孔、洞应遮盖好,以防在运输或储存期间有外物侵入;
7)包装材料应坚固,并采用防潮、防震措施,以保证运输途中不会损坏设备。包装箱内应有装箱单,分别列出名称、规格、数量等,包装箱外应有明显标注货物的名称、数量、重量及运输要求等;
8)供货商提供的橇装设备宜在工厂组装后整体包装运输,如装运困难,也可分成若干个分橇块运至现场后进行安装, 但所有分橇块应在工厂内进行预拼装,以确保在现场能够顺利拼装。
11 验收
11.1 工厂验收
业主将在供货商发货前按照本技术规格书和数据单进行工厂验收。
11.2 到货验收
1)业主将在货物到达工地后进行现场验收测试,其测试程序将在开始前通告供货商。
2)现场验收的测试项目将由业主在技术规范书中任意选择,其测试结果由业主和供货商双方签字认可。
3)在上述测试中,若发生任一项指标不符合技术规范书要求,供货商应在一周内更换其不合格产品。如果指标不合格系由供货商原因造成,则所有费用由供货商负担。
11.3 中间验收
1)业主将产品安装完毕后在每一中继段上进行初步验收测试,其验收测试程序将在开始前通告供货商。
2)测试结果由业主和供货商双方签字认可。
3)在上述测试中,若发生任一项指标不符合技术规范书要求,供货商应在两周内更换其不合格产品。如果指标不合格系由供货商原因造成,则所有费用由供货商负担。
11.4 zui终验收
业主将在产品安装调测完毕后进行zui终验收测试, 其验收测试程序将在开始前通告供货商。
测试结果由业主和供货商双方签字认可。
在上述测试中, 若发生任一项指标不符合技术规范书要求, 供货商应在两周内更换其不合格产品。如果指标不合格系由供货商原因造成,则所有费用由供货商负担。
12 技术文件提交要求
12.1 投标期间提交文件
供货商所提供的文件至少应包括:
?详细的系统技术方案和说明;
?详细的系统配置框图、及仪表设备的接线图;
?带有设备的外观尺寸和质量的装配图;
?设备选型的计算书;
?所有电气设备的电源要求;
?浪涌保护设置;
?接地系统要求;
?操作手册;
?用户指南;
?系统中采用的各种设备和材料详细的产品说明书;
?系统可靠性和可用性分析;
?连接现场撬装到控制室控制盘的连接电缆的清单和性能;
?对招标技术文件的逐条应答;
?详细的工作内容及执行计划;
?所需的资质证书;
?第三方产品的授权书及质量、售后保证书;
?质量保证手册;
?亚博竞彩网站的售后服务保证书;
?zui近几年内与本项目类似的工作业绩;
?详细的设备材料清单
?备品配件清单(按可选项列出);
?提供技术文件清单;
?负责和参加项目的主要人员名单、资质证书、业绩;
?分包方及其参与项目的人员的详细情况介绍、名单、资质证书、业绩等;
?采用的标准和规范清单;
?培训计划及课程安排;
?工厂验收和现场验收的内容及执行计划;
?现场调试方案及执行计划;
?投产方案及执行计划;
?存在的问题和建议;
?详细的分项报价和总价;
?本文件中提及的其它要求。
12.2 zui终提交文件
供货商应提供6套完整的工程技术文件和2套刻录在光盘中的全套工程技术文件。工程技术文件采用中文。
图纸应使用autocad 常用版本软件绘制,若使用了特殊的字型及线形,应随图纸一并提供。文档采用microsoft office 常用版本软件(如word、excel、access等)编制。
在系统设计期间,供货商除向业主和设计方提交自用气调压计量系统的有关技术文件以外,还应提供涉及系统相关部分的技术资料和参数,如对通信的要求、供电要求、接地要求、计量安装尺寸、系统重量等(不限于此)。
供货商zui终提供的文件zui少应包括:
?文件目录/索引;
?系统设计文件;
?所有仪表设备的操作使用说明书;
?竣工文件;
?双方的会议和来往文件;
?所有校验、测试、验收报告;
?所有的软件。
提交文件的详细种类、内容、数量、时间等,应在合同签订前确认。
由供货商负责其供货范围内所有设备和材料的安装,系统内各种设备之间的布线及连接,系统与第三方系统或设备通信接口的连接。
系统配电和接地的连接,均由供货商负责。
13 技术服务
13.1
1)供货商提供的产品到达现场后,必须派出专业人员到施工现场培训专业接续人员正确安装产品。
2)供应商(制造商)在中华人民共和国境内常设服务机构,应昼夜24小时提供足够的备品、备件和技术服务。
3)当产品出现故障或不能满足业主要求时,供应商应按业主要求排除故障,直到业主满意为止。
4)当业主需要供货商提供服务时,供货商应在4小时内做出答复,(如必要)需在12小时内派服务工程师到现场,其它站在48小时内派服务工程师到现场。确需国外派员时不超过20天。
5)在质保期内,供应商负责对业主提出的质量疑异做出书面明确答复。确属质量问题时,供应商应及时采取保护措施且负责免费更换,并相应延长其质保期。
13.2 培训
供货商应根据项目的具体情况编写技术和管理培训计划和培训教材,为业主、设计、现场操作人员提供培训。
培训的目的是使参加培训的人员掌握分输站撬装设备的系统配置以及对一些常规故障的维护和维修;使参加培训的人员在掌握所使用的系统的情况下搞好安装、调试、投运、运行管理和维护维修等项工作。
技术培训的课程应采用专门的培训教材和培训手册,教材所用的文字应采用汉语。供货商应在投标书中提交一份切实可行的包括培训时间与培训费用的培训计划建议书。供货商应提供教室、培训教师、培训教材和培训用设备。
14 亚博竞彩网站的售后服务
撬装设备在现场验收后,供货商应zui少提供12个月的质量保证期,在质量保证期内,对于非买方责任引起的质量问题或系统故障,供方应免费为买方更换设备、恢复系统正常运行。超过保证期后发生的质量问题,也应给予及时维修或供应配件。
供货商在投标文件中应提供一份亚博竞彩网站的售后服务保证书,并应在投标文件中提出对系统的硬件、软件进行长期(5~10年)、有偿、定期及不定期的维护、维修、的可行方案。在该方案中zui少应列出服务项目、服务商名称、对服务请求的响应、价格等内容。
供货商提供的撬装设备的所有软件、硬件和其它辅助设备,在中国境内应有强大的亚博竞彩网站的售后服务能力,并提供保证函件,以方便业主对亚博竞彩网站的售后服务的需求。
15 项目实施
从合同生效之日起,即进入项目实施阶段。合同生效后15天内合同双方在预定的地点召开项目开工会,会期预计5~8天。会议所需的费用由供货商负责。在开工会上双方将讨论项目实施的所有细节问题及详细的进度计划并以会议纪要的形式发布作为今后工作的大纲。
在项目实施期间,合同双方应定期召开例会,协调和协商有关事宜,特别是项目实施的初期。
在项目实施期间,由双方被授权人员签署的会议纪要和文件与合同具有同等效力。
在项目实施期间,供货商应保证项目管理的有效性和充足的人力资源,确保本项目的质量和进度。供货商在投标时应根据本项目的要求提供有关的项目管理文件,如组织设计、质量保证手册、进度计划及控制、采购计划、文档控制、对分包商的管理、hse、施工组织等。
项目实施通常分为系统设计和集成、编程和组态、工厂验收试验、装箱发运、现场安装及调试、现场验收试验、预投产、投产、竣工验收等主要环节。
业主方的项目和专家将定期或不定期的对各个阶段的成果、进度、质量进行审查,并作出决定。各个阶段的工作均应获得业主的批准,特别是系统设计和集成阶段。对各个阶段成果的审查一般采用会议的方式进行。会议的地点、费用由双方协商决定。
供货商应根据本技术规格书、合同和其它相关的技术文件进行撬装设备的详细设计,并在规定的时间向业主方提交详细的设计成果,供业主审查。详细设计获业主批准后方可实施。若需对获业主批准的事项进行修改,应报业主审批。设计成果zui少应包括:
?系统设计和详细技术方案及功能说明;
?系统方框图;
?控制柜内设备布置和接线图;
?防雷系统;
?接地系统;
?操作手册;
?用户指南;
?系统中采用的各种设备和材料详细的产品说明书;
?采用的标准和规范的文本;
?详细的设备和材料清单;
?详细的软件清单;
?撬装设备与站控系统之间的通信协议;
?操作程序流程框图;
?i/o表;
?显示画面及其说明;
?在线帮助说明;
?培训内容和计划;
?项目实施计划;
?工厂验收和现场验收 的详细内容和计划;
?现场调试方案和实施计划;
?投产方案和实施计划;
?亚博竞彩网站的售后服务方案;
?建议等。
在业主认为需要时,将派遣有关专业的专家与供货商一起工作,并监督生产的全过程。业主有权对系统设计、选用的设备、材料和选用的软件等提出修改及决定性的意见。业主保留对所提交的技术及其它的资料变更的权力,供货商在项目实施过程中应充分考虑到这些因素。供货商在投标时应明确说明:工程实施组织、人员组成;在工程哪些阶段需要业主的专家参与工作,并提供便利条件,切实保证业主的专家真正了解系统功能,系统的结构。与本文相关的论文:蒸汽减压阀在宝冶应用
下一篇:化工厂废气处理微压调节阀