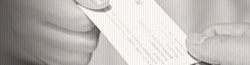
上海申弘阀门有限公司
联系人:李贤
手机:15901754341
传真:86-021-31662735
邮箱:494522509@qq.com
地址:上海市青浦区金泽工业园区
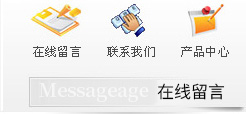
耐磨阀在煤化工应用
上海申弘阀门有限公司
之前介绍三台气体减压阀串联减压,现在介绍耐磨阀在煤化工应用介绍了现代煤化工中的2 种工艺———直接液化与间接液化的异同点。通过对现代煤化工中的煤液化工艺的分析,提出了在该类装置上使用的阀门的选择要求,还从材料、工艺、抗腐蚀、结构及耐磨特性等方面进行了分析,以期能够为煤化工企业及阀门制造企业提供参考。耐磨材料是新材料领域的核心,约占新材料研究领域中85%,特种耐磨材料对高新技术的发展起着重要的推动和支撑作用,是二十一世纪世界各国新材料领域研究发展的重点,也是世界各国高技术发展中战略竞争的热点,跟随我们的脚步关注耐磨材料发展动态。
耐磨阀在煤化工应用产品工艺特点:
1、化学成份匹配: 合理的化学成份是宁国南方公司全体科研人员通过多年的摸索逐步优化形成的控制曲线,具有*化学成份匹配方法,使它能更好的服务韧性和硬度相结合,达到*状态。
2、熔炼工艺特点: 采用电熔炼调质有效解决了材质偏析和成份控制问题,确保了钢水的质量,充分发挥了熔化炉的熔化能力和有害气体的排放能力。
3、温控工艺特点: 温控工艺是铬系铸球生产中一项非常重要、复杂的工艺,不同的出炉温度、浇注温度、出模温度及热处理温度,非常敏感地反应在产品质量上,掌握适宜的浇注温度、出模温度,使产品从液态到固态过程中达到良好的境界。
4、成型工艺特点: 在浇注温度与模具温度温差在1500℃时浇注,可以使产品内部组织晶粒细化而更加致密,使碳化物呈放射状排列,在研磨工作中,这种碳化物再次嵌入基体,不断形成硬质层,从而使硬度和韧性保持在合理的交会点上,大大提高了铸球的韧性和硬度相结合。
5、热处理工艺特点: 采用全自动油淬火生产线,进行淬火、回火处理,使它烧的透、淬的透,均能达到研磨材料基体不破碎、不失圆、耐磨系数高等特点。
6、检测手段: 有光谱直读仪、自动碳检测仪、高空落球试验机、金相显微镜等仪器追踪检测,确保不合格产品不出厂。
1、引言
现代煤化工在我国尚属新兴产业,现代煤化工装置与其他生产化工装置一样,离不开管道、阀门等设备,煤液化所使用的阀门与一般石油化工装置所使用的阀门既有相同之点,又有不同之处。不同之处,zui明显的就是阀门的抗蚀、耐磨损能力。耐磨阀门在许多领域都有应用,如硅化工中的多晶硅装置,电力系统的发电站等都使用耐磨阀门。但在现代煤化工中,所使用的耐磨阀门,由于其使用工况不同,工艺介质不同,危险程度不同,腐蚀性不同,其技术要求也不同。
2、现代煤化工工艺
图1 是现代煤化工中煤液化的流程简图,从图中可以看出,煤通过直接液化或者间接液化2种不同的工艺路线,zui后得到需要的汽油、柴油、航煤等,当然,也可以继续进行深加工,得到高附加值的pp、pe 等聚烯烃产品及其它石油化工下游产品。直接液化和间接液化的流程有一定区别。煤直接液化是在高温(400℃ 以上) 、高压(10mpa 以上) ,在催化剂和溶剂作用下使煤的分子进行裂解加氢,直接转化成液体燃料,再进一步加工精制成汽油、柴油等燃料油,所以又称加氢液化。
煤制油化工工艺简图
图1 煤制油化工工艺简图
采用直接液化工艺液化油收率高;煤消耗量小;产品馏份油以汽、柴油为主;油煤浆进料,设备体积小,投资低,运行费用低。但是反应条件相对较苛刻,如德国老工艺液化压力甚至高达70mpa,现代工艺如igor、hti、nedol 等液化压力也达到17 ~ 30mpa,液化温度430 ~ 470℃。同时,除液化反应器的产物组成较复杂,液、固两相混合物由于粘度较高,分离相对困难。氢耗量较大。煤的间接液化技术是先将煤全部气化成合成气,然后以煤基合成气( 一氧化碳和氢气) 为原料,在一定温度和压力下,将其催化合成为烃类燃料油、化工原料和产品的工艺,包括煤炭气化制取合成气、气体净化与交换、催化合成烃类产品以及产品分离和改质加工等过程。
采用煤间接液化工艺合成条件较温和,无论是固定床、流化床还是浆态床,反应温度均低于350℃,反应压力2.0~3.0mpa;转化率高,如sasol 公司sas 工艺采用熔铁催化剂,合成气的一次通过转化率达到60% 以上,循环比为2.0时,总转化率即达90% 左右;但是受合成过程链增长转化机理的限制,目标产品的选择性相对较低,合成副产物较多;有效产物-ch2-的理论收率低,工艺废水的理论产量比较高。煤消耗量比直接液化要大。同时反应物均为气相,设备体积庞大,投资高,运行费用高。煤基间接液化全部依赖于煤的气化,没有大规模气化便没有煤基间接液化。
无论是直接液化还是间接液化,工艺介质中不仅有煤粉,而且,还含有h2、o2、h2s、co、nh3、co2、cl -、hn - 等易燃易爆及腐蚀性介质。而直接液化的温度在400℃以上、压力在10mpa 以上;间接液化的温度低于350℃,反应压力2.0 ~3.0mpa;这么多复杂的成分与工况要求,对其装置中使用的阀门从材料到制造加工都会提出一些特殊要求。
3、现代煤化工对阀门产品的技术要求
3.1、材料要求
直接液化也叫加氢液化。在加氢过程中,其阀门、管道及相关设备处于高温高压氢气中,氢损伤就是一个很大的问题。高温高压硫化氢与氢共存时的腐蚀也很严重。正因为如此,为抗高温硫化氢的腐蚀通常阀门材料会选用奥氏体不锈钢。这样又有可能出现不锈钢的氢脆、奥氏体不锈钢的硫化物应力腐蚀开裂及堆焊层氢致剥离现象等损伤。另外还有cr-mo 钢的回火脆性破坏的问题。而且,物流中存在的氨和硫化氢等腐蚀介质可能引起的损伤等也是必须加以慎重考虑的。由于煤直接液化反应中有油煤浆的存在,煤浆对阀门、管道等设备材料的磨损问题必须要进行考虑。因此要求用于制造阀门的材料要具有符合使用要求的综合性能。具体来说,应该具有:
( 1) 作为描述材料内质特性的致密性、纯洁性和均质性性能要优越,这对于厚( 或大断面) 钢材尤为重要。
( 2) 要具备满足设计规范要求的化学成分、室温和高温力学性能的要求。
( 3) 要具有能够在苛刻环境下长期使用的抗环境脆化性能。
在阀门招标文件中对于阀门的致密度有明确的要求,对于锻造阀门,一般会通过对锻件的锻造比、晶粒度等要求,来实现控制致密度的要求。但是,对于铸造阀门,只是在相关的技术文件中,提到应使铸件体致密度均匀,消除铸件的缩孔与缩松,少有见到量化指标。其实恰恰是铸造阀门,往往因为对铸造工艺的质量控制不同,造成阀门铸件的质量差别很大,主要影响因素有: 成型材料的选择不同,浇冒口的设置不同,冷铁位置与数量的选择不同,凝固顺序的差异,以及冷却时间的不同等,都会导致其致密度、均质性性能差别很大。后续的热处理工艺也是阀门质量保证的非常关键的步骤之一,热处理炉的温控、铸件在热处理炉中的码放、保温时间及冷却方式与速度等因素都会影响zui终阀门铸件的机械性能。耐磨阀门的产生:阀门是用来控制液体、气体等介质的流动方向和流量的装置,具有断流、节流、分流、止回等功能。在工作过程中,阀门长时间受到高速流动的流体的磨损或腐蚀,会发生泄漏或者出现故障,因此,阀门用内衬耐磨材料来减轻磨损,这时,阀门被称为“耐磨阀门”。耐磨阀门的品种及规格繁多,管径zui大可达10m, 可承受1000mpa的高压。阀门作用的介质也多种多样,包括粉、液、气或两相甚至三相混合介质,应用行业非常广泛。
耐磨阀门主要应用在以下五个行业:
1)矿业:选矿厂中利用刀闸阀控制矿浆的流动与截止;利用夹管阀控制矿浆流量;利用止回阀防止矿浆倒流;利用三通阀实现两泵一阀的设置,省掉一条管路的投资。由于矿浆对阀门磨损较大,所以要求矿用阀门具有较高的耐磨性。
2)建筑业:空调系统中应用到的阀门种类较多,如空调循环水系流量控制及流向控制选用的闸阀,防止停电时水造成的压力采用的止回阀等。
3)石油化工行业:炼油装置中,阀门主要用于管道中油类液体的启闭、节流和调压,主要有闸阀、截止阀、安全阀等,其中阀门应用zui多的为闸阀,约占总数的80%左右。
4)冶金行业:炼钢是冶金行业中zui主要的工艺,对阀门的要求也比较苛刻,如各个部分冷却水以及氧气、氮气等压缩气体的开关,主要可采用蝶阀、四通阀、截止阀等。
5)电力行业:我国发电站逐渐向大型化发展,所以也就要求阀门的口径也较大,现主要用于控制各种设备的运行及管路上液体介质的输送情况,如闸阀、安全阀、减压阀、蝶阀等。
3.2、工艺要求
煤直接液化既有加氢装置高温、高压、临氢的特性,又有煤化工腐蚀磨损工况并存的特点,因此,原材料的来源非常关键,目前,还没有找到一个行之有效的方法来控制原材料的选用,一般来讲,对阀门材质的成分尤其是有害元素含量,如s、p、o、n 及总碳当量等,提出相应的明确的指标要求,虽然这种要求往往高于材料的基本普通要求,但是,对于zui终产品质量,仅靠这些成分指标还是不够的,因为影响原材料机械性能的微量元素远不止这些。严格的讲,我们的要求仅是对常见的危害材料机械性能的微量元素予以控制,并没有也不可能完全将所有可能出现的对金属材料机械性能有害元素成分全部罗列出来。因此,铸造厂应该严格控制原料来源,对于所加工的原料不仅应该进行熔炼,还应该进一步进行精炼,特别是加强炉前控制,只有这样才有可能保证铸件质量。
在保证原材料质量的前提下,针对该类装置还有一些特殊的要求:
(1) 对于现代煤化工装置的铸造阀门不能采用精密铸造工艺。因为煤液化即是加氢裂化工艺,由于氢分子对金属材料特殊的穿透性,而精密铸造出来的铸件比较疏松,均匀性也较差,因此,对于临氢工况和高温高压工况都不适宜采用精密铸造工艺取得阀门铸件;
(2) 奥氏体不锈钢要进行固溶化热处理( 固溶化热处理温度为1050 ± 10℃) ,对于321 和347材料,还应进行稳定化热处理( 稳定化温度为900± 10℃);
(3) 热处理炉不应采用燃煤加热炉,应采用电加热炉或者是天然气加热炉,铸件在加热炉内码放应利于炉内气流循环。由于煤加热炉会加大炉体各部位的温差,因此,不能采用燃煤加热炉;
(4) 铸件试棒的选取应为联体试件。“分体”试棒无论是浇铸过程还是热处理过程都无法真正代表铸件本身的特性,与铸件本身实际的机械性能存在较大的误差,因此,不能采用“分体”试棒检验;
(5) 所有阀门必须对铸件进行射线检查,检查的范围包括阀体、密封元件、阀盖,铸钢件在凝固过程中易产生缺陷,尤其对于铸钢件的关键部位、应力集中区域、承压能力薄弱的部位等,应特别加以关注。对于碳钢、合金钢铸造阀门,应逐件进行磁粉或液体渗透检查。检查范围: 阀体、阀盖和密封元件的外表面及可触及的内表面和阀杆。对于不锈钢铸造阀门,应逐件进行液体渗透检查。检查范围: 阀体、阀盖和密封件的外表面及可触及的内表面和阀杆;
(6) 每个承压铸件的所有补焊面积总和应不超过铸件的表面积的10%;每个承压铸件的重大补焊数量,dn50~dn100 不超过1个;dn150 ~dn250 不超过2 个;dn300 ~dn350 不超过3 个。
上述铸造缺陷的补焊应在zui终热处理之前进行;当在射线探伤时发现有缺陷,且属于可补焊修复的,允许进行1 次补焊。补焊后应重新拍片检验,检验合格后该铸件必须重新进行热处理。补焊应具备焊接规程及工艺鉴定证书,填充金属的物理、化学性能及耐腐蚀性均应与母体金属接近。所有受压组件的缺陷zui终热处理之后,均不允许通过焊补进行修理。
3.3、要具有能够在苛刻环境下长期使用的抗环境脆化性能
对于操作在高温高压氢环境下的阀门,在操作状态下,阀门内壁中会吸收一定量的氢。在停工的过程中,若冷却速度太快,使吸附的氢来不及扩散出来,造成过饱和氢残留在器壁内,就可能在温度低于150℃时引起亚临界裂纹扩展,给阀门的安全使用带来威胁。阀门制造厂在阀门焊接时需要注意控制tp347 中δ 铁素体含量,焊态时zui大值以10%为宜( 为防止焊接中产生热裂纹,下限可控制不低于3% ) ,以避免含量过多时在焊后zui终热处理过程发生较多的相变,而产生脆性。
3.4、阀门结构要求
上海申弘阀门有限公司主营阀门有:亚博安卓-亚博竞彩网站,电动截止阀阀门结构的设计应避免煤浆结焦使阀门失效并方便清洗。油煤浆有一个特点: 如果流通不畅或者静止不动,也就是介质的流况不好,将会沉积并有可能发生聚合反应,从而出现结焦并使阀门抱死。目前在直接液化煤浆管道上使用的切断阀门全部是球阀,当操作需要切断管道将球阀关闭时,阀球内部的油煤浆因为无法排出,沉积在球腔内,就有可能结焦抱死。当球阀关闭后,煤浆因为沉积结焦而致阀球无法再次打并将球阀的耐磨层毁损剥落。所以,其实在此工况下选用球阀并不是zui合适的选择。
3.5、阀门耐磨要求
浆料工况下使用的球阀应采用金属硬密封形式,且阀座与球的材质相同,确保两者有相同的膨胀系数,在高温的条件下不会出现球体‘卡死’的现象。由于阀门的很多使用工况是在高温高压下的,根据使用经验,有些阀门在常温下测试没有问题,但是在高温工况下发生启闭操作困难,究其原因是阀芯与阀体之间产生不同步热胀造成的。所以,生产厂在出厂前应做高温启闭试验。但高温启闭试验绝不是将整个阀门投入热源中,使阀门整个温度升高,这样所得到的测试结果与实际情况是不符合的。因为,在真正使用过程中,阀门是因介质温度高而升温的,此时是阀芯先热而阀体外表面随后慢热起来,如果将整个阀门投入热源中,则阀体先热而阀芯后热,与实际工况正好相反,起不到测试的目的。高温启闭试验应建立与实践工况相一致的温度梯度。
涂层与基本材质的膨胀率应相近。否则,在高温和常温交变过程或者高温下,易产生龟裂,从而更易使涂层剥落。对超音速喷涂(hvof) 或类似的方法,涂层表面硬度为64~68hrc,结合强度不小于10mpa;对冶金熔合或类似的方法,涂层表面硬度为62 ~68hrc,结合强度不小于70 mpa。涂层的有效厚度(不包括过渡层) 为0.2 ~0.5mm。阀座应采用刮刀式设计。在球体转动时可提供一个挂刷的动作,防止阀球与阀座间的颗粒沉积。在设计时,应该注意,利用刮刀可以将球体与阀座间的颗粒挂刷掉,但是,这种刮刀设计在有的工况下会带来另一个问题: 因为附带了刮刀设计,在刮刀处形成了一个锐角,而这种锐角势必产生应力集中现象,更加不利于涂层与基材之间的结合,在磨蚀工况下,更易导致涂层的剥落,致使阀座毁损。
4、结语
现代煤化工对管道和阀门的要求与选用与传统石油化工工艺的要求有着诸多不同,装备制造和选型工作面临着新的挑战,在管道与阀门方面,多年来,设计、使用单位与阀门制造企业共同努力,充分调动各自的技术资源进行技术攻关,如今在该类阀门的设计水平、制造技术等方面都有了长足的进步,并正在进一步完善结构及制造工艺,扩大应用领域。与本文相关的论文:化工碱渣截止阀
下一篇:手动蜗轮通风蝶阀d341w