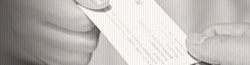
上海申弘阀门有限公司
联系人:李贤
手机:15901754341
传真:86-021-31662735
邮箱:494522509@qq.com
地址:上海市青浦区金泽工业园区
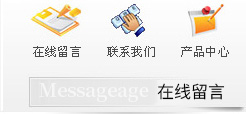
阀门加工对刀及走刀什么是对刀?什么是走刀? 阀门加工对刀及走刀 加工阀门对刀及走刀
之前介绍,现在介绍 阀门加工对刀及走刀调整刀具切削刃相对工件或夹具的正确位置的过程称为对刀。大,多次切削。数控车削加工中,应首先确定零件的加工原点,以建立准确的加工坐标系,同时考虑刀具的不同尺寸对加工的影响。这些都需要通过对刀来解决。数控机床本身有个机械原点,你对刀时一般要试切的啊,比如车外径一刀后z向退出,测量车件的外径是多少,然后在g画面里找到你所用刀号把光标移到x输入
x...按测量机床就知道这个刀位上的刀尖位置了,内径一样,z向就简单了,把每把刀都在z向碰一个地方然后测量z0就可以了.这样所有刀都有了记录,确定加工零点在工件移里面(offshift),可以任意一把刀决定工件原点.这样对刀要记住对刀前要先读刀.有个比较方便的方法,就是用夹头对刀,我们知道夹头外径,刀具去碰了输入外径就可以,对内径时可以拿一量块用手压在夹头上对,同样输入夹头外径就可以了.如果有对刀器就方便多了,对刀器就相当于一个固定的对刀试切工件,刀具碰了就记录进去位置了.所以如果是多种类小批量加工买带对刀器的.节约时间.以前用的mazak车床,换一个新工件从停机到新工件开始批量加工中间时间一般只要10到15分钟就可以了.(包括换刀具软爪试切)
对刀的方法
在数控加工中,对刀的基本方法有手动对刀、对刀仪对刀、atc对刀和自动对刀等。
手动对刀的基础是通过试切零件来对刀,采用“试切—测量—调整”的对刀模式。手动对刀要较多地占用机床时间,但由于方法简单,所需辅助设备少,因此普遍应用于经济型数控机床中。采用对刀仪对刀需对刀仪辅助设备,成本较高,但可节省机床的对刀时间,提高对刀的精度,一般用于精度要求较高的数控机床中。atc对刀由于操纵对刀镜以及对刀过程还是手动操作,故仍有一定的对刀误差。自动对刀与前面的对刀方法相比,减少了对刀误差,提高了对刀精度和对刀效率,但cnc系统必须具备刀具自动检测的辅助功能,系统较复杂,一般用于数控机床中。
经济型数控车床的手动对刀方法
简单的对刀过程
上海申弘阀门有限公司主营阀门有:减压阀(,可调式,手动(manual)方式下,可按以下顺序进行对刀,得出刀具偏置量。 (1)进入主菜单,进入手动方式(manual);
(2)选定对刀用的基准点(刀尖容易到达又方便观察的位置);
(3)选一把刀作为基准刀,例如1号刀,在可以换刀的位置键入t10命令(选1号刀,无刀偏);
(4)移动刀架,将基准刀的刀尖移到对刀基准点,按“命令comm”键,显示命令菜单,执行nez命令(设置新系统坐标),将系统的坐标设置为(0,0);
(5)按“命令comm”键,执行t.size命令(用系统坐标设置刀具偏置),可将基准刀对应的刀偏值置为(0,0);
(6)移动刀架到可以换刀的位置,用t20命令换2号刀; (7)移动刀架让刀尖对准对刀基准点; (8)按“命令comm”,执行t.size命令,可将刀具对应的刀偏值置为当前系统坐标值(正好是刀偏值); (9)重复(6)至(8)步骤,可得到所有刀具的刀偏值。
若使用光学对刀仪,可将对刀仪的中心线作为对刀基本点,从而得到较为的刀偏值。 试切对刀过程
(1)用“命令comm”、t.test功能设置刀偏
手动方式下,按以下顺序进行试切对刀可得出较为的刀具偏置。 ①装夹好工件和刀具;
②进入手动(manual)方式;
③选择好基准刀(如1号刀),用t10命令换刀;
④移动刀架使刀靠近工件端面,开启主轴车端面,将新端面作为z轴方向基准位置;
⑤车外圆长度为5~10mm,不退刀,主轴停,测量该位置x方向直径值和z方向离基准点距离,如图1所示;
⑥按“命令comm”,执行t.test命令(用试切得到的尺寸设置刀具偏置)。显示:txtest(x为当前刀具号)
x— 输入试切位置测量出的x轴方向直径值x1 z— 输入试切z方向长度(距基准位置距离)z1
第二行提示by(表示是否为基准刀)
按“y”键,系统将根据输入的值进行刀具偏置(刀偏号=刀具号)的设置;
⑦换刀,重复⑤⑥,可得出所有刀具的偏置(按步骤⑥操作,输入x、z值后,第二行提示变为y,按“y”键,系统将根据输入值进行刀具偏置的设置。
(2)用“参数param”、t.size功能直接输入刀偏值,完成刀偏设置。①装夹好工件和刀具; ②进入手动方式;
③选择基准刀(如1号刀),用t10命令换刀;
④车端面,在x方向退刀,执行nez命令,将系统z坐标设为0,x坐标不变;
⑤车外圆5~10mm,在z方向退刀,执行nez命令,将系统x坐标设为0,z坐标不变; ⑥按“参数param”键,选t.size参数。将1号刀刀偏值修改为x0,y0; ⑦移动刀架到可以换刀的位置,用t20命令换2号刀;
⑧移动刀架,让刀尖对准工件端面,记下此时z坐标z2;然后刀尖对准外圆,如图2(b)所示,记下此时x坐标x2。
按步骤⑥方法将2号刀的刀偏值修改为x2z2;
⑨重复⑦⑧可修改其余刀具的刀偏,完成所有刀具的刀偏设置。
2.2.1加工程序中工件加工原点的设定方法
一般情况下在程序中应工件加工原点,gsk928系统数控车床工件加工原点的方法是使用g92指令,格式为:g92xz(x、z均为值),x、z后面输入坐标值,表示刀具当前位置到加工坐标原点的距离。g92指令工件加工原点的方法如图3所示。
2.2.2工件加工原点的确定
从图3可知,用g92指令设定加工原点时,工件加工原点的位置与刀具起始位置是紧密相联的,只要确定了刀具起始位置,也就确定了工件坐标原点。
gsk928系统数控车床确定刀具起始位置的工作是通过手动操作来完成的。
以图4为例,工件端面中心为编程原点,加工程序中用g92指令;g92x100z5,将编程原点变成工件加工原点,确定刀具起始位置的具体操作步骤如下:
(1)首先根据程序指令,计算出刀尖到工件端面中心的距离为:直径方向x=100(直径值) 轴向z=5;
(2)装夹好工件,起动主轴,移动刀架使刀尖(基准刀)慢慢靠近端面如图4(a)所示,用前述方法将系统z坐标设为“0”;
(3)试切外圆,切削长度约10mm(以能方便测量为准);
(4)用前述方法将系统x坐标设为“0”,然后退刀使刀具离开工件;
(5)停车并测量工件外径d1,计算100-d1值。
(6)将刀架移到坐标x=100-d1,z=5,如图4(c),此点即为刀具起始点位置。
确定刀具起始位置后,就可调入程序进行自动加工了。当执行完g92x100z5程序段后,数控系统便将工件端面中心确定为工件加工原点。
(1) 一般对刀
一般对刀是指在机床上使用相对位置检测手动对刀。下面以z向对刀为例说明对刀方法,见图1。
5-24
图1 相对位置检测对刀
刀具安装后,先移动刀具手动切削工件右端面,再沿x向退刀,将右端面与加工原点距离n输入数控系统,即完成这把刀具z向对刀过程。
手动对刀是基本对刀方法,但它还是没跳出传统车床的“试切--测量--调整”的对刀模式,占用较多的在机床上时间。此方法较为落后。
(2) 机外对刀仪对刀
机外对刀的本质是测量出刀具假想刀尖点到刀具台基准之间x及z方向的距离。利用机外对刀仪可将刀具预先在机床外校对好,以便装上机床后将对刀长度输入相应刀具补偿号即可以使用,如图2所示。
图2 机外对刀仪对刀
(3)自动对刀
自动对刀是通过刀尖检测系统实现的,刀尖以设定的速度向接触式传感器接近,当刀尖与传感器接触并发出信号,数控系统立即记下该瞬间的坐标值,并自动修正刀具补偿值。自动对刀过程如图3所示.与本产品相关论文:
下一篇:加工阀门刀具切削部分的材料